Experience of PPDS labelling requirements - PPDS evaluation
This chapter covers the experience of consumers with Food Hypersensitivities (FHS), Food Business Operators (FBOs) and Local Authorities (LAs) since the Prepacked for Direct Sale (PPDS) labelling requirements were introduced. Specifically, the chapter explores behaviours and practices with regards to PPDS foods, the experience of implementing organisational changes and the sources of information and guidance used to inform changes.
Consumers
PPDS purchasing behaviour
Most FHS consumers purchased PPDS foods (91%). However, as illustrated by Figure 5.1, it was uncommon for them to purchase PPDS foods often (7%). Instead consumers most frequently reported buying them sometimes (36%) or rarely (40%). Nine percent of consumers said that they never purchased PPDs foods.
Figure 5.1 How often consumers purchase PPDS foods
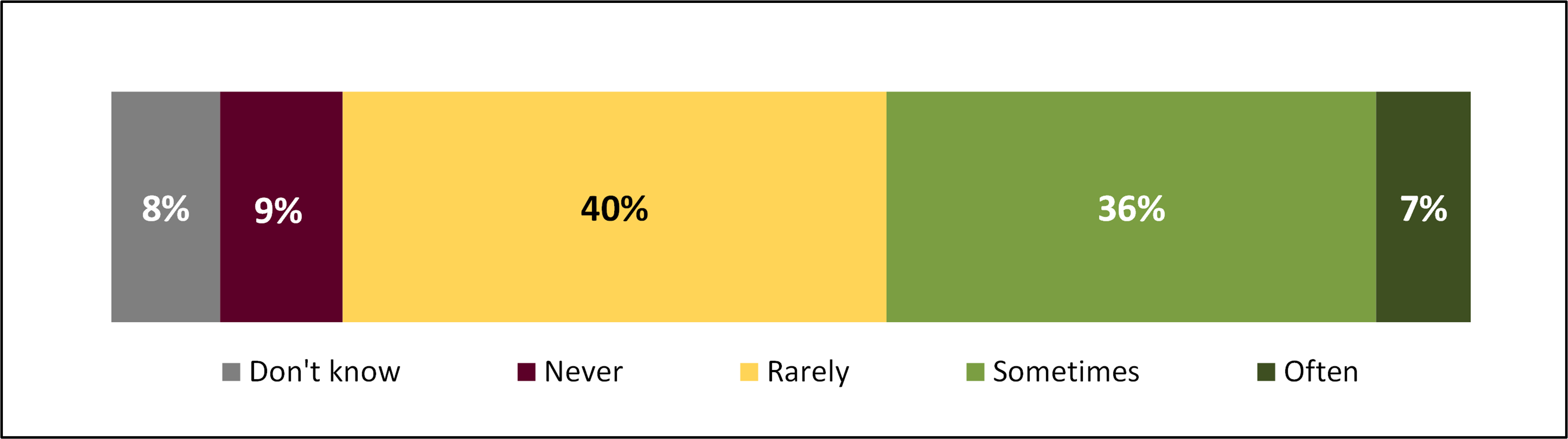
C3. How often do you buy PPDS foods? Base: All FHS consumers (1809).
Geography and age were associated with likelihood to purchase PPDS foods. Consumers in Northern Ireland (83%) were less likely than those in England (91%) and Wales (92%) to purchase PPDS foods. Meanwhile, younger consumers aged between 18 and 34 were more likely than average to purchase them (95%).
In addition, the nature of consumer’s food hypersensitivities had a bearing over their likelihood to purchase PPDS foods. Those with allergies and intolerances other than Coeliac disease were more likely to do so than those with Coeliac disease (92% vs 89%) and those with a mild (97%) or moderate (96%) allergy or intolerance were more likely to purchase PPDS foods that those with a severe allergy or intolerance (87%).
During qualitative interviews, many consumers that purchased PPDS foods, particularly those with severe food hypersensitivities, explained that they tended to do so as a ‘last resort’ due to concerns over cross-contamination and the accuracy of labelling. They tried to avoid eating food that was not prepared by themselves or someone they knew, and if they did buy food to take away they generally opted for prepacked food from a large chain (e.g. supermarket bought sandwiches). Consumers that purchased PPDS foods frequently explained that they felt comfortable doing so because they had a mild allergy or intolerance, and so the risk posed by cross-contamination and inaccurate labels was less significant.
"I'm if going to buy pre-packaged food I'll mostly get it from a supermarket… I'd definitely steer clear of bakeries… independents might have all the good intentions in the world and put all these processes in place but it's just one person in the kitchen who didn't wash the knife or whatever. That's all it takes."
Consumer, England, Severe hypersensitivity
“I have always avoided stuff packaged on the day. I have just got into the routine of not buying this. I get my food shop done weekly and that comes through the door, and I just buy the same foods.”
Consumer, Wales, Severe hypersensitivity
Consumers who reported never buying PPDS foods typically attributed this to a lack of trust and confidence. (footnote 1) Around two fifths (38%) said they do not trust that PPDS food is totally allergen free, over a quarter (27%) said they do not trust that preparation areas are free from cross-contamination and a fifth (22%) said they lack trust in the accuracy of PPDS labelling.
Experience of accessing PPDS ingredients information
As presented in Figure 5.2, four fifths (81%) of FHS consumers that buy PPDS foods said they check labels on PPDS packaging at every point of purchase. Of the remainder, 10% said they check labels most of the time, 3% said they check labels about half the time, a further 3% said they check labels occasionally and 1% said they never check PPDS labels.
Figure 5.2 How often consumers check labels on PPDS foods
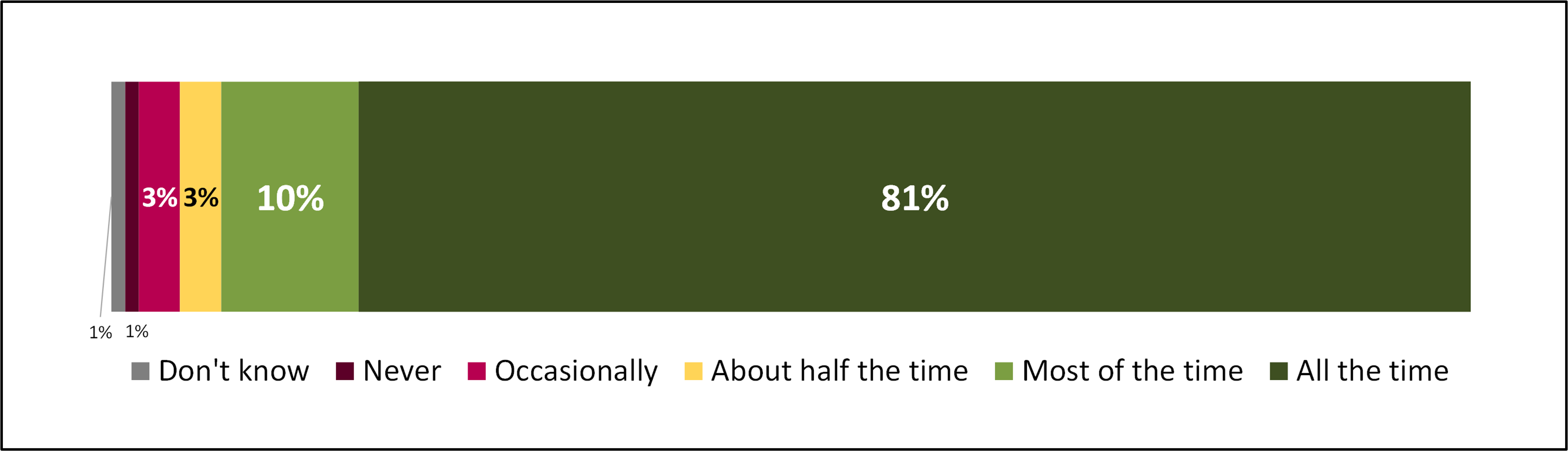
C6. How often do you look at PPDS food labels? Base: FHS consumers that buy PPDS foods (1639).
The frequency to which consumers checked labels on PPDS packaging increased with the severity of food hypersensitivity. Half (50%) of those with a mild allergy or intolerance checked labels on PPDS packaging at every point of purchase, compared to three quarters (73%) of those with a moderate allergy or intolerance and more than nine in ten (92%) of those with a severe allergy or intolerance. Furthermore, those with Coeliac disease were more likely than those with other allergies or intolerances to check labels on PPDS every time (93% vs 68%). (footnote 2)
When considering understanding and awareness, consumers who found it difficult to identify PPDS foods were more likely to check the labels more often (95% always or most of the time vs 88% of those who find it easy).
Linked to the type and severity of food hypersensitivity, consumers that reported rarely purchasing PPDS foods were more likely than those that reported purchasing PPDS foods sometimes or often to say they check labels on PPDS packaging at every point of purchase (88% vs 77%).
Amongst those that checked labels on PPDS foods, only one in twenty (5%) reported being able to always access the information they needed to be able to identify whether it contains an ingredient that would cause an unpleasant reaction. (footnote 3) As shown in Figure 5.3, a third (34%) said that this information was available most of time, a fifth (21%) said it was available about half the time and a quarter (25%) said it was only occasionally available. A further 4% said the information was never available.
Figure 5.3 How often allergen information is available on PPDS foods
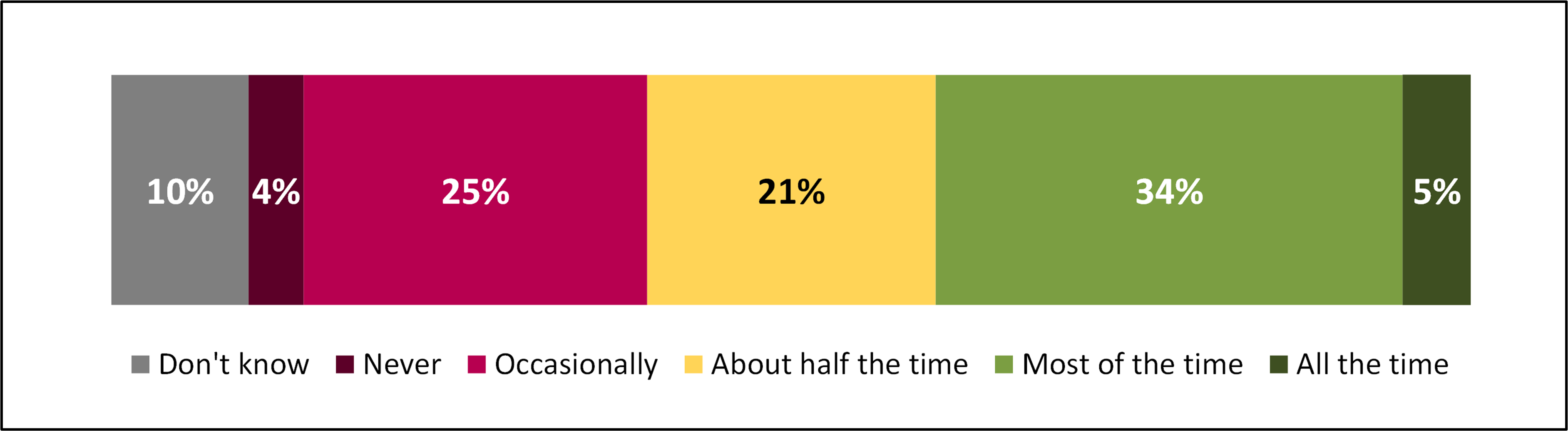
C5. How often is the information you need to identify a food that might cause an unpleasant reaction readily available? Base: FHS consumers that buy PPDS foods and check labels (1606).
Those with a mild allergy or intolerance were more likely than those with a moderate or severe allergy or intolerance to report being able to always access the information needed to identify whether PPDS foods contain an ingredient that would cause an unpleasant reaction (10% vs 5%).
There were few differences between those with a hypersensitivity to regulated allergens and those with a hypersensitivity to non-regulated allergens in the reported availability of such information, with the exception of those stating that the information is never available. Consumers who only had an allergy to a non-regulated allergen were more likely to say the information is never available (8% vs 4% of those with an allergy to a regulated allergen). Again there was a correlation with ease of identifying PPDS foods, those who found it easy to identify PPDS foods were more likely to find the information they need all or most of the time (59% vs 33% of those who found it difficult).
Consumers who reported purchasing PPDS foods sometimes or often were more likely than those that rarely made a purchase to state that they were able to access the information they needed every time (8% vs 3%) or most of the time (44% vs 26%). So too were those that reported it being easy to identify PPDS foods compared to those that reported it being difficult (every time: 12% vs 4%; most of the time: 47% vs 30%).
During qualitative interviews, some consumers gave accounts of food products they considered to be PPDS foods without full ingredients lists and the allergen information they required to make an informed decision. This was said to be more common when buying PPDS food from small independent FBOs. In such circumstances consumers were required to ask staff to provide allergen information verbally or abandon the purchase and visit another establishment.
"The likes of the big supermarkets you can find it in there it is not a problem, but the smaller independent shops are still not doing it…it's more than a year on and there is still no label on it."
Consumer, Northern Ireland, Severe hypersensitivity
Reflecting on their experience of buying PPDS foods since the associated labelling requirements were introduced in October 2021, almost two thirds (63%) of consumers reported experiencing issues with accessing ingredients information on PPDS packaging. The most common issue experienced was allergen information not being easy to read (53%). Other prominent issues with PPDS food experienced since October 2021 are listed in Figure 5.4.
Figure 5.4 Issues with labelling on PPDS food experienced since October 2021
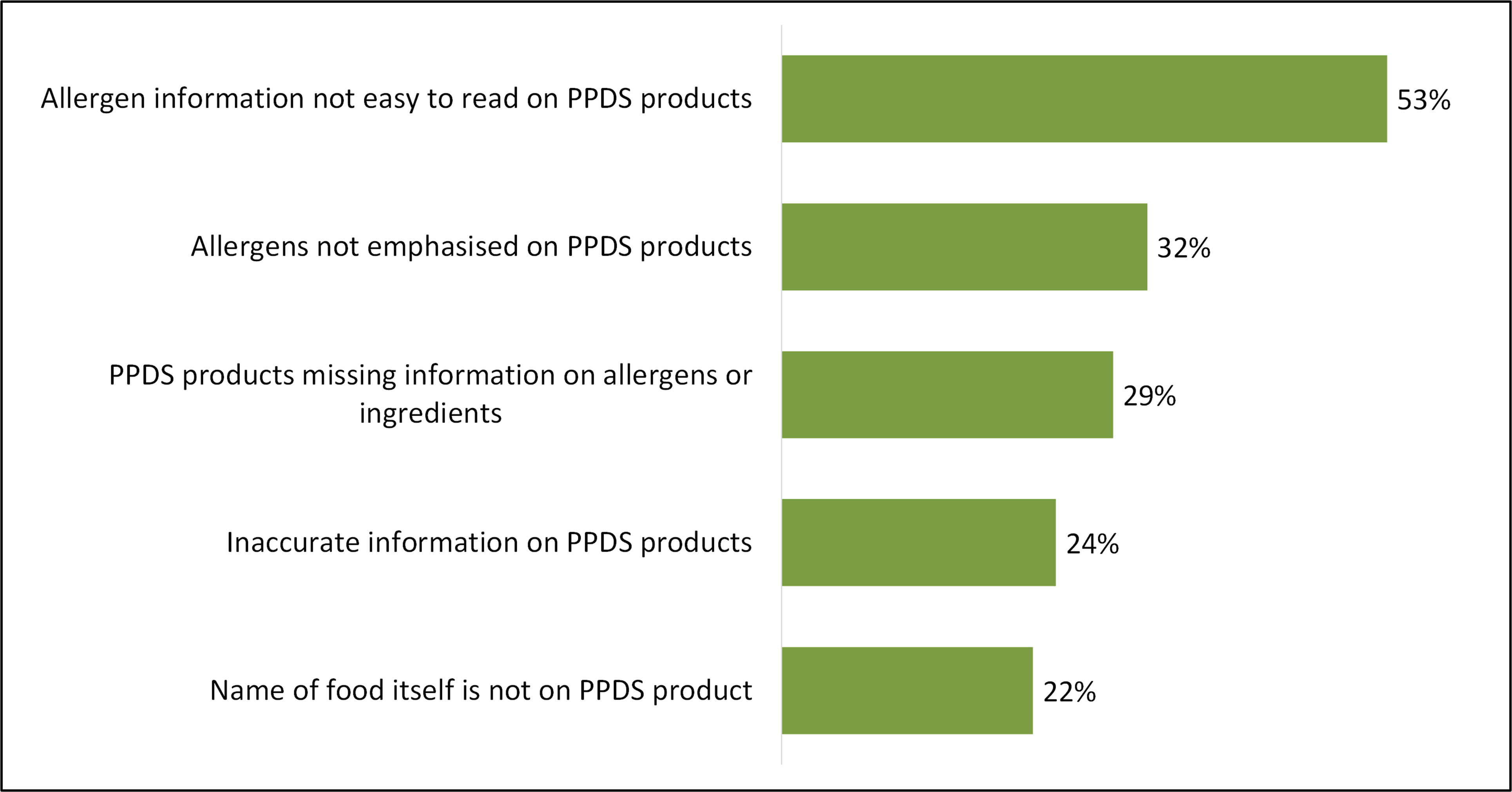
E4. Since October 2021, have you experienced any of the following issues with foods prepacked for direct sale (PPDS)…? Base: FHS consumers that buy PPDS foods (1639).
During qualitative interviews, many consumers reported that when information is present on PPDS food it is quite often unclear due to long lists, small fonts or varying label formats. A few also commented that the use of Precautionary Allergen Labelling (PAL) on PPDS packaging introduced doubt about the accuracy of ingredients lists.
"They generally all have [ingredients lists] on them now, but the quality of the labelling and the size, the ease of analysing varies massively. And there is always that caveat of ‘may contain’ as well, so it varies."
Consumer, England, Severe hypersensitivity
“When you have to start scouring the label, which is in small print and blurred I just don't bother with it.”
Consumer, England, Severe hypersensitivity
More than half (58%) of FHS consumers that buy PPDS foods were confident that the information provided on labels is accurate. Specifically, as presented in Figure 5.5, 51% of consumers were fairly confident and 7% were very confident. Around a third (30%) were not confident, with 8% not at all.
Figure 5.5 Confidence in PPDS food labels
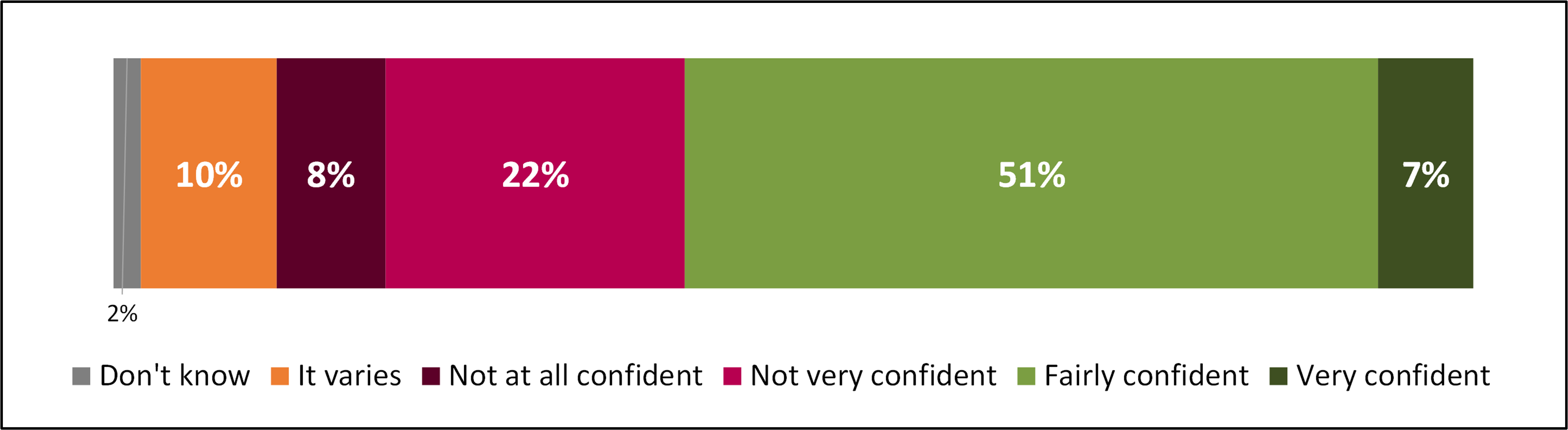
C7. How confident are you that information provided on PPDS labels is accurate? Base: FHS consumers that buy PPDS foods (1639).
Those with a mild allergy or intolerance were more likely than those with a severe allergy or intolerance to feel confident that the information presented on PPDS labels was accurate (70% vs 54%). Furthermore, consumers that reported purchasing PPDS foods sometimes or often were more likely than those that rarely made such a purchase to feel confident (70% vs 48%).
During qualitative interviews it transpired that confidence in the accuracy of ingredients information on PPDS packaging was influenced by a variety of factors. Many said their confidence varied between different FBOs and was influenced by the design of labels. For example, some said they felt more confident about the accuracy of labels used by large chains of FBOs they had visited before, while others said they felt more confident when labels were clear and easy to read.
“It depends where you’re getting the food from. I’m concerned about cross-contamination in places such as market stalls. In bigger stores I feel more confident.”
Consumer, England, Severe hypersensitivity
Some consumers attributed their confidence in the accuracy of information to having ‘faith’ and ‘trust’ in the ability and willingness of FBOs to comply with PPDS labelling requirements. From their perspective, now that it was a legal requirement to provide full ingredients lists and emphasise allergens, they felt more confident in the information provided on labels.
“You put your trust in the fact that it’s a legal requirement for an establishment to list everything. You have to have a little bit of trust that it’s being followed… [full ingredients list] give a little bit more confidence that there’s been a bit of thought put into it.”
Consumer, England, Severe hypersensitivity
Consumers who lacked confidence in the accuracy of ingredients information typically attributed this to the risk of cross-contamination. For these consumers, while lists of intended ingredients and allergens were seen to be a positive step, they did not provide them reassurance as they felt there was still the possibility of traces of other ingredients and allergens being present.
“I'm not at all confident and I don't think Natasha's Law has changed that at all. Natasha's Law has changed the way that ingredients are listed, but it doesn't talk about cross-contamination or the things that matter to me.”
Consumer, England, Severe hypersensitivity
Food Business Operators
Practices and processes
Labelling ingredients
As presented in Figure 5.6, around three quarters (76%) of FBOs that sold PPDS food reported being compliant with PPDS labelling requirements. In other words, they displayed the name of the product, listed all ingredients and emphasised allergens on ingredients lists. The number of FBOs that did some of the components of the requirements was higher; 89% emphasised all allergens, 85% displayed the name of the product and 83% labelled all ingredients.
Figure 5.6 Reported labelling practices of FBOs
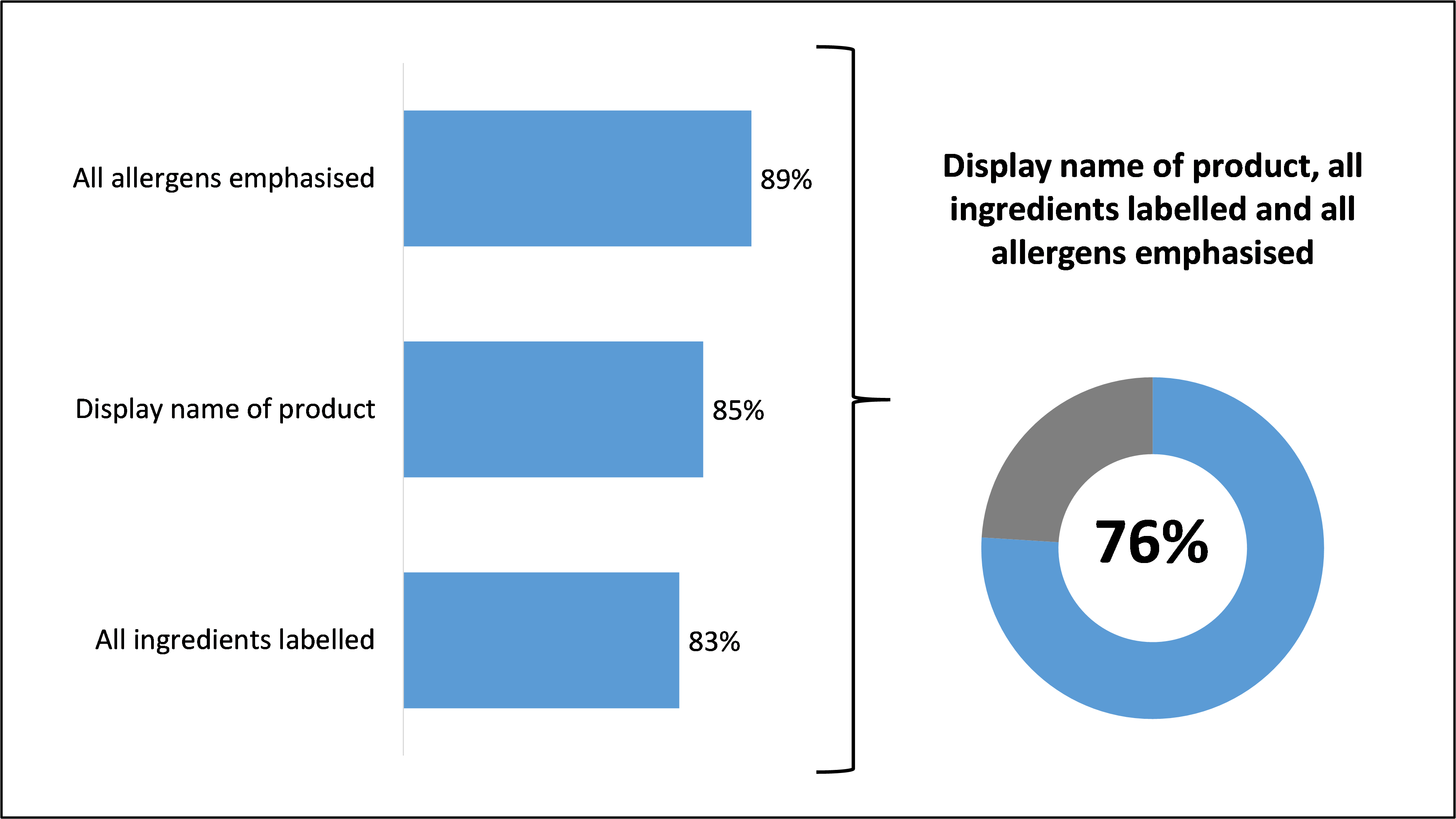
B1a. Thinking about the PPDS foods you sell, do you put the name of the food on the packaging? B1. Thinking about the PPDS foods you sell, do you display all ingredients on the packaging? B4. Are the allergens in your PPDS foods emphasised on the packaging? Base: FBOs that sell PPDS (838).
There were no statistically significant differences by country in the proportion of FBOs that were compliant with PPDS labelling requirements (England: 76%; Northern Ireland: 78%; Scotland: 79%; Wales: 74%).
However, there were notable differences in self-reported compliance by sector and size. With regards to sector, retailers were more likely than caterers to self-report compliance (87% vs 66%), with particularly high levels amongst butchers (92%), general retail (86%) and bakers (85%). Two thirds (66%) of catering businesses self-reported compliance, with particularly low levels amongst restaurants and cafés (62%).
With regards to size, the likelihood to self-report compliance increased with employee headcount. Around seven in ten (69%) of those with between 1 and 5 employees were compliant, rising to 80% of those with between 6 and 10 employees and 86% of those with 11 or more employees.
During qualitative interviews, a few FBOs that did not do all three components of the PPDS labelling requirements attributed this to low awareness and understanding. For example, a chocolatier said that they did not emphasise all allergens on PPDS foods at the time of the survey because they were unaware it was a requirement. This FBO said they had started to label in a compliant manner since participating in the survey. One FBO that operated a temporary canteen at events said that they tried their best to operate compliantly, but struggled to list all ingredients on their PPDS foods because of last minute changes to ingredients used in recipes. They did however stress that they take care in ensuring all allergens are labelled.
“In an ideal world everything would have full ingredients list with allergens emphasised. But it’s not possible to keep on top of it because of so many variables… we serve a lot of options of food and the chef might add something in last minute, like something to season a sauce, which would then have to be added.”
FBO, England, Catering, 11 or more employees
Amongst those that labelled all ingredients or emphasised allergens on the packaging of PPDS food, the most common way this information was presented was through labels printed in-house (64%). (footnote 4) A quarter (25%) used labels printed by a third party, while 8% used handwritten labels and 6% used labels supplied by their head office.
Across all sectors and sizes of FBOs, the printing of labels in-house was the most common method of presenting ingredients information on PPDS foods. However, there were some differences in the likelihood to use alternative methods. General retail businesses were more likely than average to use labels printed by a third party (33% vs 25%) and labels supplied by their head office (11% vs 6%), while restaurants and cafes were more likely than average to handwrite labels (15% vs 8%).
There were also clear differences between different sized FBOs in how ingredients information was presented on PPDS food packaging. Those with 11 or more employees were more likely than those with between 1 and 5 employees to print labels in-house (70% vs 61%). Conversely, those with between 1 and 5 employees were more likely than those with 11 or more employees to use labels printed by a third-party (18% vs 20%).
During qualitative interviews, many of those that printed labels for PPDS food in-house said they had invested in labelling software and hardware to assist them with compliance. These new systems were introduced because they were felt to be more accurate than alternatives and because they would reduce administrative burden on staff in the long run. However, a few commented that the initial financial outlay for new systems and the time required to set-up software (i.e. input ingredients information) had been significant.
“A new printer and tablet were introduced for ease of use… that's the easiest way to present the information to the customer without causing the staff headaches.”
FBO, Northern Ireland, General Retail, 1 to 5 employees
“We have a hand-held tablet so if I'm making a cheese and tomato roll, I'll put in 'large granary roll' … the label will then be generated [by the software] and put on after it’s made."
FBO, England, Catering, 6 to 10 employees
“[Ingredient information] is loaded into our labelling programme…that is the point where it puts allergens in bold and sorts the formatting … the labels we use just run off templates that have been approved by our [food safety] consultant.”
FBO, England, Delicatessen, 11 or more employees
Almost three quarters (72%) of FBOs reported using Precautionary Allergen Labelling (PAL) on their PPDS foods. Retailers were more likely than caterers to use PAL (76% vs 67%), especially general retail businesses (82%). With regards to size, those with 11 or more employees were more likely to use PAL (85%) than those with between 1 and 5 employees (64%) and those with between 6 and 10 (73%).
The most common reason for using PAL were to flag the risk of cross-contamination during preparation (44%), however it was also used to ‘pass on’ PAL used on ingredients sourced from suppliers and wholesalers (28%).
“Our deli is quite small and we do handle nut products, and unfortunately due to the size of the deli cross-contamination is probably a bit of a higher risk.”
FBO, Northern Ireland, General Retail, 1 to 5 employees
“We use ‘May Contain' when the manufacturer includes it on their packaging, but won't if it is not specified on their packaging… it means the manufacturer has been too lazy to say yes or no. That's one area that needs to be changed. It does or it doesn't, not maybe. If someone's got an allergy, they deserve better than that may contain.”
FBO, England, Catering, 11 or more employees
Checking labels
Three fifths (63%) of FBOs said they checked for changes in the ingredients of PPDS foods sourced from suppliers or wholesalers at every delivery (36%) or often (27%) (see Figure 5.7). A fifth (18%) said they conducted checks on an ad-hoc basis (e.g. when product lines or suppliers change), while 7% reported conducting checked ‘sometimes’ and 5% reported never conducting such checks.
Figure 5.7 How often the ingredients of PPDS foods sourced from suppliers or wholesalers are checked
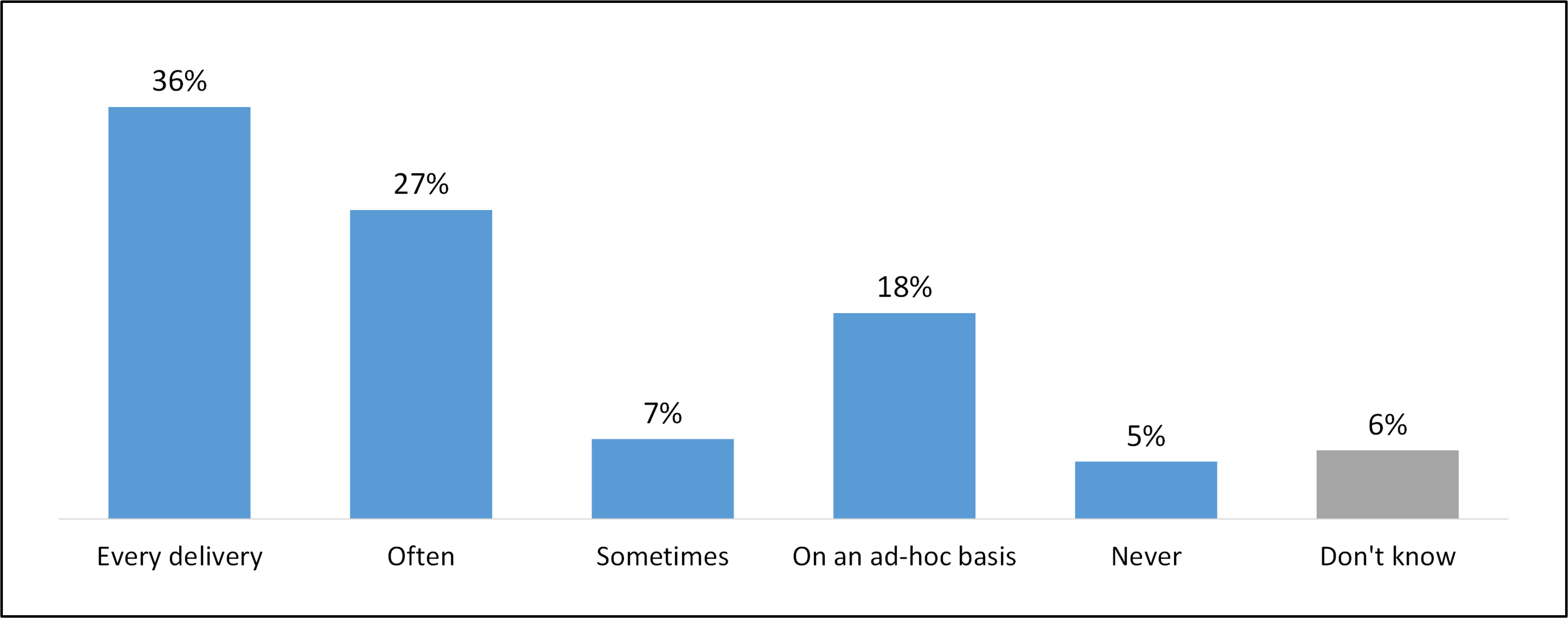
B6. How often do you check or audit the ingredients of products sourced from your suppliers or wholesalers that are used in your PPDS foods for changes? Base: FBOs that sell PPDS (838).
Of those who reported that they labelled all ingredients or emphasised allergens on the packaging of PPDS food, close to nine in ten (87%) reported checking that the ingredients and allergens listed are accurate and more than nine in ten (91%) reported updating ingredients listed on packaging when suppliers change ingredients or are unable to provide ingredients. (footnote 5)
With regards to checking the accuracy of labels, the most common circumstances in which checks were conducted were on a fixed schedule (e.g. once a day or once a week) (20%) and every time labels are printed (18%). Other circumstances mentioned by at least one in ten FBOs included when suppliers change a recipe (15%), each time a new batch of PPDS food is made (11%) and when a new PPDS product is introduced (10%).
More than three quarters (78%) of FBOs that reported updating ingredients listed on packaging when suppliers change or are unable to provide ingredients said they did this every time this situation arises. A further 8% said they did this most of the time, 3% some of the time, 2% hardly ever and 5% never. The remainder were unable to comment on the frequency of updating labels. FBOs that checked the accuracy of ingredients listed on the packaging of PPDS food every time labels were printed were more likely than other FBOs to update ingredients lists on PPDS packaging every time suppliers change or are unable to provide ingredients (90% vs 76%), indicating a correlation between the two practices.
As presented in Figure 5.8, two thirds (62%) of LAs described FBO compliance with PPDS labelling requirements in their area as ‘good’ or ‘very good’, with 3% of the opinion that compliance was ‘very good’. A third (33%) of LAs described compliance as ‘poor’ or ‘very poor’. It should be noted that LA perceptions of compliance are not directly comparable to self-reported levels of compliance amongst FBOs. The perceptions of LAs were based on observations made across multiple PPDS inspections, while FBOs were only considering compliance at their establishment.
Figure 5.8 LA views on overall levels of compliance with PPDS labelling requirements
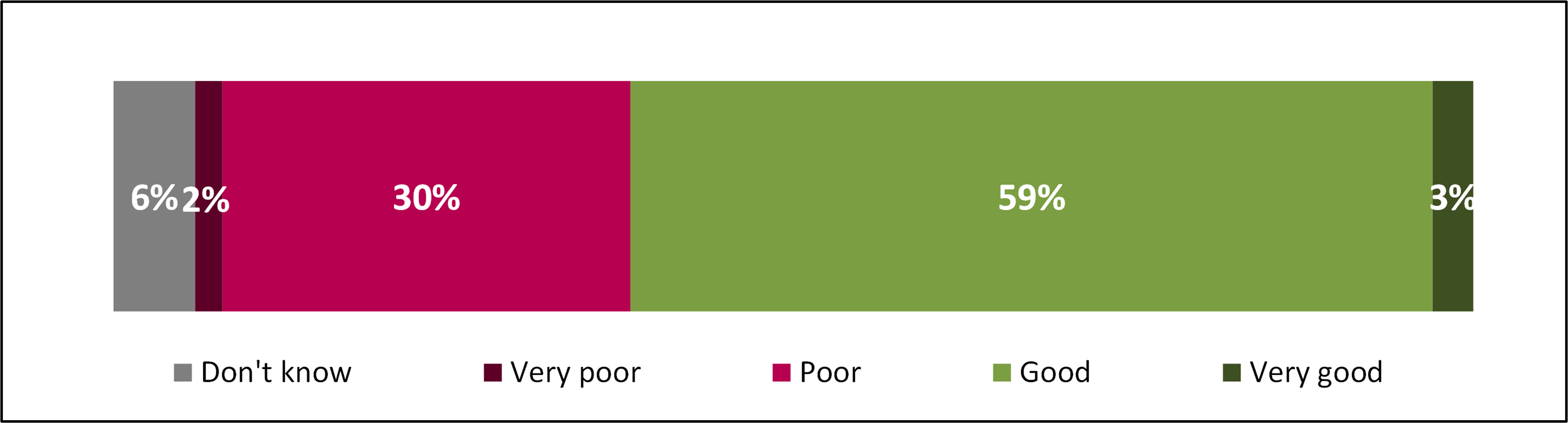
D4. How would you describe overall levels of compliance with PPDS labelling requirements among the food businesses your local authority has checked? Base: LAs that have conducted compliance checks (123).
Experience of compliance
Overall, four fifths (79%) of FBOs that sold PPDS foods and were aware of the associated labelling requirements reported that they found it easy complying with the new rules, with 41% reporting that they found it very easy (see Figure 5.9). Around one in ten FBOs (11%) said that compliance had been difficult, while a similar proportion (9%) said that compliance had been neither easy nor difficult.
Figure 5.9 Extent to which FBOs have found compliance easy or difficult
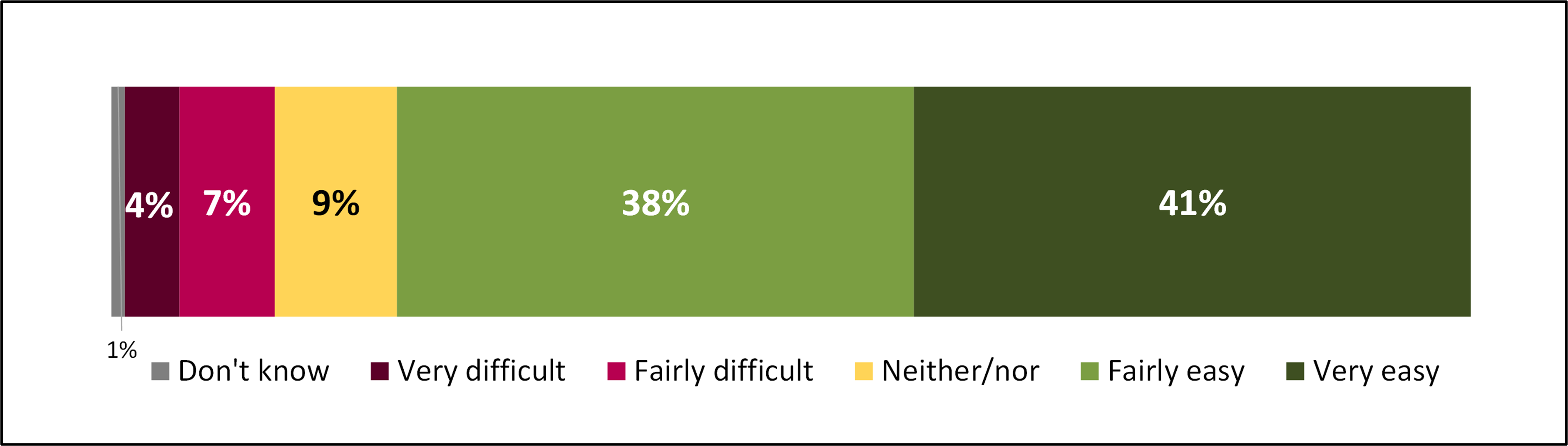
C1. To what extent have you found it easy or difficult to comply with the PPDS labelling requirements? Base: FBOs that sell PPDS and aware of PPDS labelling requirements (766).
In line with this evaluation, 79% of FBOs that participated in baseline research conducted in 2019 predicted that compliance with the PPDS labelling requirements would be easy. (footnote 6) However, compared to expectations held in 2019, significantly fewer FBOs in this evaluation reported experiencing difficulty with compliance (11% vs 15%) and significantly more FBOs reported that compliance was neither easy nor difficult (9% vs 4%).
Across each of the four nations, the majority of FBOs reported finding it easy to comply with PPDS labelling requirements (England: 81%; Northern Ireland: 73%; Scotland: 72%; Wales: 65%). However, FBOs in England were more likely than those in Scotland and Wales to report finding it easy (81% vs 72% in Scotland and 65% in Wales).
With regards to sector, retailers were more likely than caterers to report finding it easy to comply with PPDS labelling requirements (85% vs 74%). Amongst retailers, general retail businesses stood out as being significantly more likely than average to have found compliance easy (91% vs 79%). Within the catering sector, FBOs which delivered events catering were significantly less likely than average to have found compliance easy (60% vs 81%).
With regards to size, larger FBOs were more likely to report finding compliance easy; 86% of those with 11 employees or more said it was easy compared to 77% of those with between 1 and 5 employees and 78% of those with between 6 and 10 employees.
Reflecting the results of the survey, during qualitative discussions many FBOs explained that they found compliance with PPDS labelling requirements to be easy. Most had experienced challenges to begin with but had typically overcome these with time following receipt of guidance or training and once new systems and processes had bedded in. A few FBOs said that the introduction of PPDS labelling requirements posed them little or no difficulty because they were meeting the PPDS labelling requirements before they became mandatory or because their head office had guided them through the transition.
"It was a bit of a shock ... it affected so much of the stuff that we sold ... but we do have all of the ingredient information … When we found out about it, we did an allergen course through the FSA."
FBO, Wales, Baker, 6 to 10 employees
“It's not difficult at all. With our till, we basically put it in and weigh it and it prints out the label for us with the allergens on it … we had always done it that way because it just makes sense.”
FBO, England, Delicatessen, 1 to 5 employees
As presented in Figure 5.10, amongst the minority (11%) of FBOs that found compliance with PPDS labelling requirements difficult, the top two causes were the time taken (46%) and the cost (31%) of introducing and updating labelling. Some FBOs attributed difficulty with compliance to awareness and understanding of the requirements, with 14% highlighting staff training and awareness as a source of difficulty and 11% reporting uncertainty around the definition of PPDS foods as a source of difficulty. Others said difficulties with compliance were associated with accessing (6%) and auditing (5%) ingredients from suppliers. The majority (75%) of FBOs reported one (40%) or two (35%) causes of difficulty, while around quarter (24%) reported experiencing three or more. (footnote 7)
Figure 5.10 Reasons why compliance was difficult
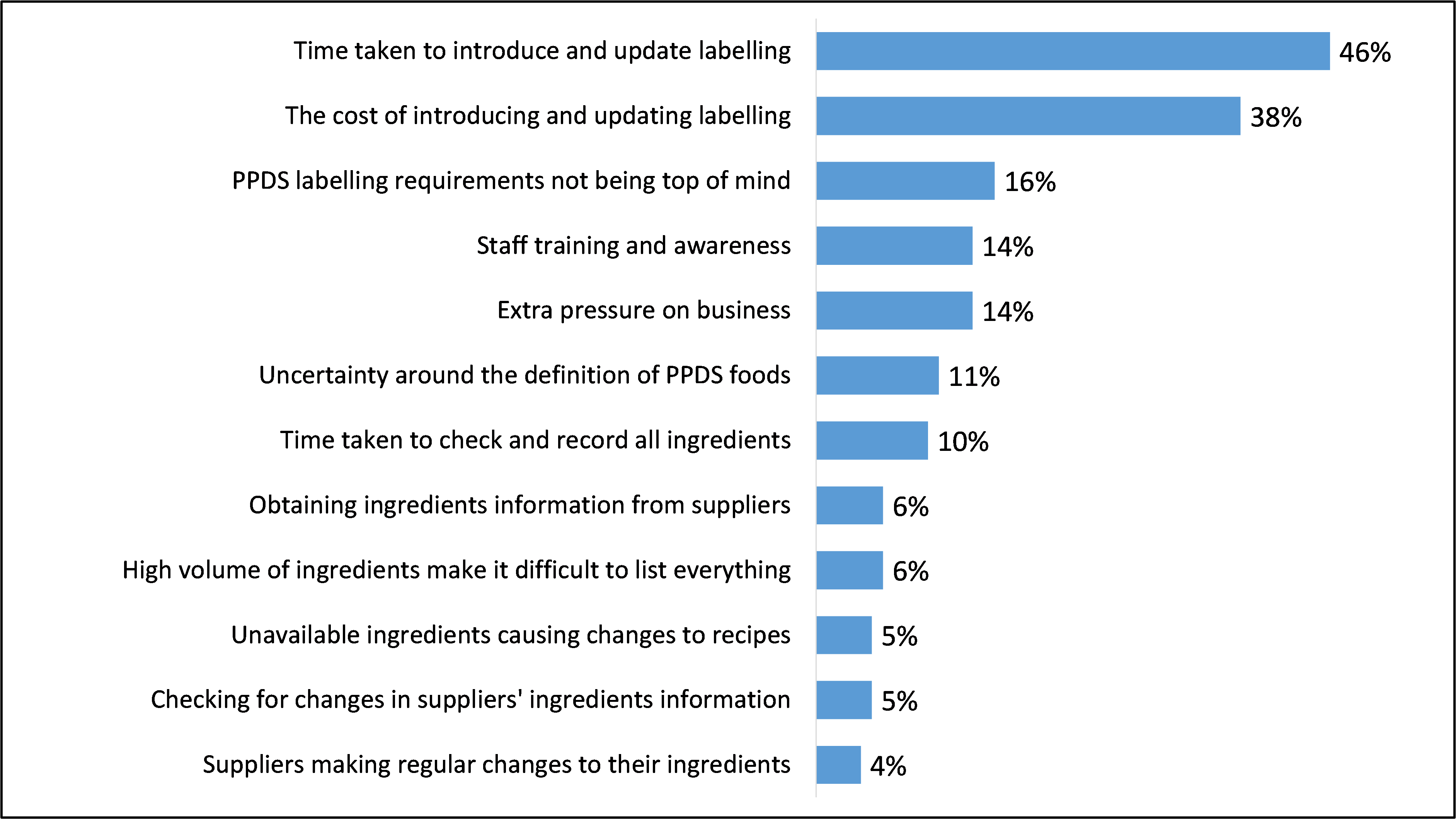
C2. What has made compliance with PPDS labelling requirements difficult? Base: FBOs that found compliance difficult (93). Responses under 5% have not been presented.
The causes of difficulty listed above were echoed during qualitative interviews, often by FBOs that had found compliance to be challenging, but also by some FBOs that reported finding compliance to be easy overall. Although this latter group had generally found meeting PPDS labelling requirements to be straightforward, there were also negative aspects to their experience.
Like the survey findings, the most prominent challenge mentioned during qualitative interview was the time required to introduce and update labelling. For some, this challenge had eased over time as investments in labelling software and printers took effect, but considerable time had been required up-front to programme software and an ongoing time commitment was needed to check ingredients and labels. For others, particularly those that had not invested in labelling software and printers and those with extensive PPDS product lines, the time required to introduce and update labelling had been an ongoing challenge. A few commented that they were considering investment in labelling software and printers to reduce administrative burden.
"I purchased a new labelling system 10 years ago that was unable to meet the requirements, so I had to buy a new one that was quite expensive. It was very time consuming initially for me, to formulate ingredients and allergens onto that system. Now, it's relatively easy but I must have spent 50 hours of my time programming it.”
FBO, England, Catering, 6 to 10 employees
“I'd say [our overall experience] is fairly positive, but it's too long winded now … the challenge is having to check if the allergens have changed on delivery, and the time it takes to change this and print off an extra label.”
FBO, England, Catering, 1 to 5 employees
Where the time required to introduce and update labelling for PPDS foods were highlighted as a challenge, often so too were costs. This was typically because of the cost of staff time to prepare and check labels of packaging. Some FBOs identified the need to purchase labels and ink for printers as overheads brought about by PPDS labelling requirements. Further detail on the impact of PPDS labelling requirements on business costs is presented in Chapter 6.
Furthermore, as covered in Chapter 4, some FBOs explained during qualitative interviews that they occasionally encountered confusion about the definition of PPDS. This was a source of difficulty in terms of compliance as it meant that some businesses were unclear whether they had applied labelling to all relevant food products.
In contrast to FBOs self-reported experiences of compliance, close to nine in ten LAs (87%) felt that FBOs had found compliance with PPDS labelling requirements to be difficult, with a third (33%) of the opinion that they had found it very difficult (see Figure 5.11). One in ten LAs said that FBOs had found compliance easy (10%), with only 1% of the view that they had found it very easy. It should be noted that LA views on the extent to which FBOs have found compliance to be easy or difficult are not directly comparable to the self-reported experience of FBOs. The perceptions of LAs were based on observations made across multiple PPDS inspections, and there is a potential for them to be skewed by instances of non-compliance. Conversely, there is a possibility that the accounts of FBOs are influence by a self-report bias.
Figure 5.11 LA views on the extent to which FBOs have found compliance easy or difficult
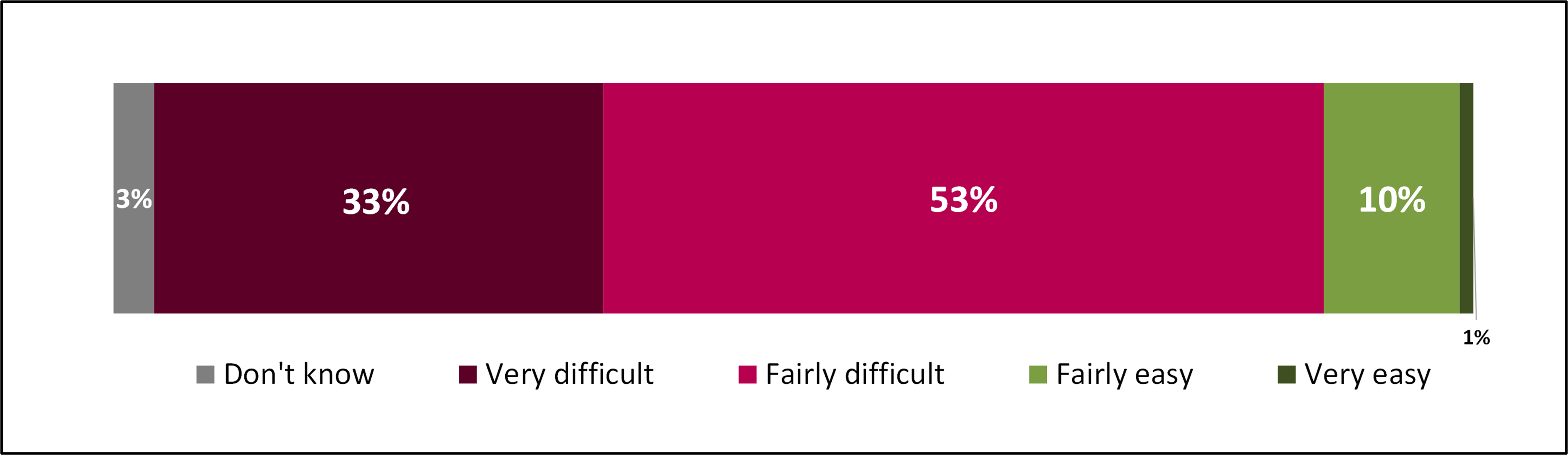
F3. Overall, how easy or difficult do you think food businesses have found complying with PPDS labelling requirements? Base: All LAs (126).
Despite LAs having a different perspective on the prevalence of difficulty, the reasons why they felt FBOs found compliance difficult were closely aligned with those identified by FBOs themselves. Indeed, the top four causes of difficulty were the same across both audiences. These were centred on the time and cost of labelling, the knowledge of staff and labelling requirements not being top of mind. Outside of these top four, there were some causes of difficulty that were not mentioned by FBOs, notably technical limitations at the premises (83%), staff turnover (59%) and information not being available in languages others than English (48%). These are shown in Figure 5.12.
Figure 5.12 LA views on why FBOs have found compliance difficult
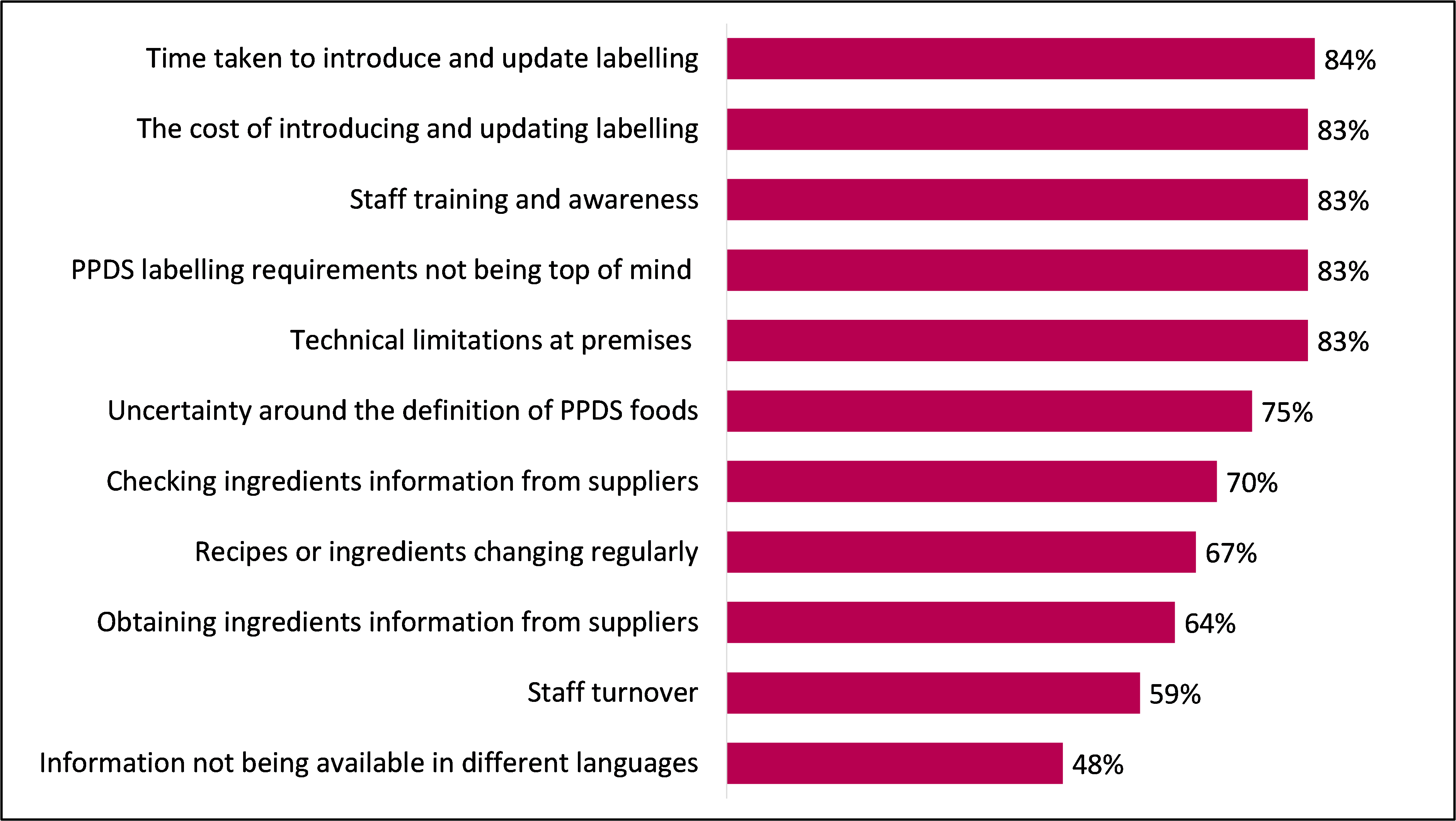
F4. What has made it difficult for food businesses to comply with PPDS labelling requirements? Base: LAs that thought FBOs have found compliance difficult (109).
Amongst the LAs that said FBOs had difficulty with compliance, around half (47%) identified smaller FBOs as those that have the most difficulty. (footnote 8) A quarter (26%) highlighted takeaways as having particular difficulty with PPDS labelling requirements, followed by convenience stores (22%), sandwich bars and delicatessens (17%), bakers (16%) and butchers (15%).
The suggestion that smaller businesses have the most difficulty with compliance chimes with the findings of previous research the FSA conducted with LAs in April 2022, in which 72% said they had concerns about the level of compliance amongst micro FBOs and 58% said they were concerned about compliance amongst small FBOs. (footnote 9) By comparison, only 4% said they were concerned about compliance amongst large FBOs.
During qualitative interviews, some LAs said that smaller FBOs have difficulty with compliance because of lower awareness and understanding of PPDS labelling requirements. (footnote 10) This was often attributed to smaller FBOs not having the time or dedicated staff to oversee food allergen labelling. Some attributed it to smaller FBOs being more likely to have informal and shifting supply chains which make managing ingredients information challenging, while others said smaller FBOs have limited financial capability to be able to invest in training and systems, which has been compounded by the recent economic climate.
“Some understand what they need to do, but we do see non-compliance. The main reason is a lack of time, especially amongst the smaller businesses. Some do not have PPDS on their radar at all, have no idea what they need to do."
Local Authority, England
"If one week a business uses one supplier and the next week, they use a different one, they might have completely different ingredients. And small businesses are having to change their labelling very often to comply with that ...They are small businesses, they aren't a big food manufacturer with quality assurers, it's usually just one business owner who has a million other things to do."
Local Authority, England
Larger FBOs, particularly those that formed part of a chain, were considered by LAs to be less likely to experience difficulties with compliance. These FBOs were said to possess the resources and financial capabilities to be able to deliver training on PPDS labelling requirements, employ staff to oversee implementation and invest in new systems. Some LAs also highlighted the centralised supply chains of larger FBOs as a factor which makes compliance easier.
“Where you've got larger businesses like the national chains… they can get people in to work out the legislation and they've got fairly good controls over the ingredients and the suppliers and the products that are coming in.”
Local Authority, Wales
“Bigger businesses have quality assurers, and may have a primary authority partnership, so they are generally going to get it right.”
Local Authority, England
Takeaways were highlighted by LAs as a group of smaller FBOs that face distinct challenges in terms of meeting PPDS labelling requirements. It was explained that the common mixture of direct and distance sales amongst these FBOs created additional administrative burden and confusion, with different labelling requirements applying to the same food products depending on whether they are collected by the consumer (where PPDS labelling requirements apply) or delivered to the consumer (where they do not). Some said that the frequent sale of prepacked condiments and sauces was a cause of difficulty as it meant there was a considerable amount of labelling required, while others said that, where English is not the first language of staff, takeaways had difficulty following guidance and writing compliant labels.
“If you go into a takeaway and ask for a pot of mayonnaise and they squeeze it out in front of you, it doesn't have to have a label and allergen information can be provided verbally. But if businesses fill those pots in advance to save time, they have to label those same mayonnaise pots."
Local Authority, England
“Sometimes there are language barriers where English is not their first language so they have a difficulty understanding what is required and then need to get the labels right where the wording may not be easy for them.”
Local Authority, Scotland
Support and guidance
Of FBOs that sold PPDS and were aware of the PPDS labelling requirements, nearly all (97%) had accessed support or guidance to learn about the requirements and how to comply with them. (footnote 11) As presented in Figure 5.13, the most common source used by FBOs was the FSA and FSS (68%), followed by LAs (49%) and Trading Standards or Environmental Health Officers (47%).
Figure 5.13 Sources of support and guidance used by FBOs
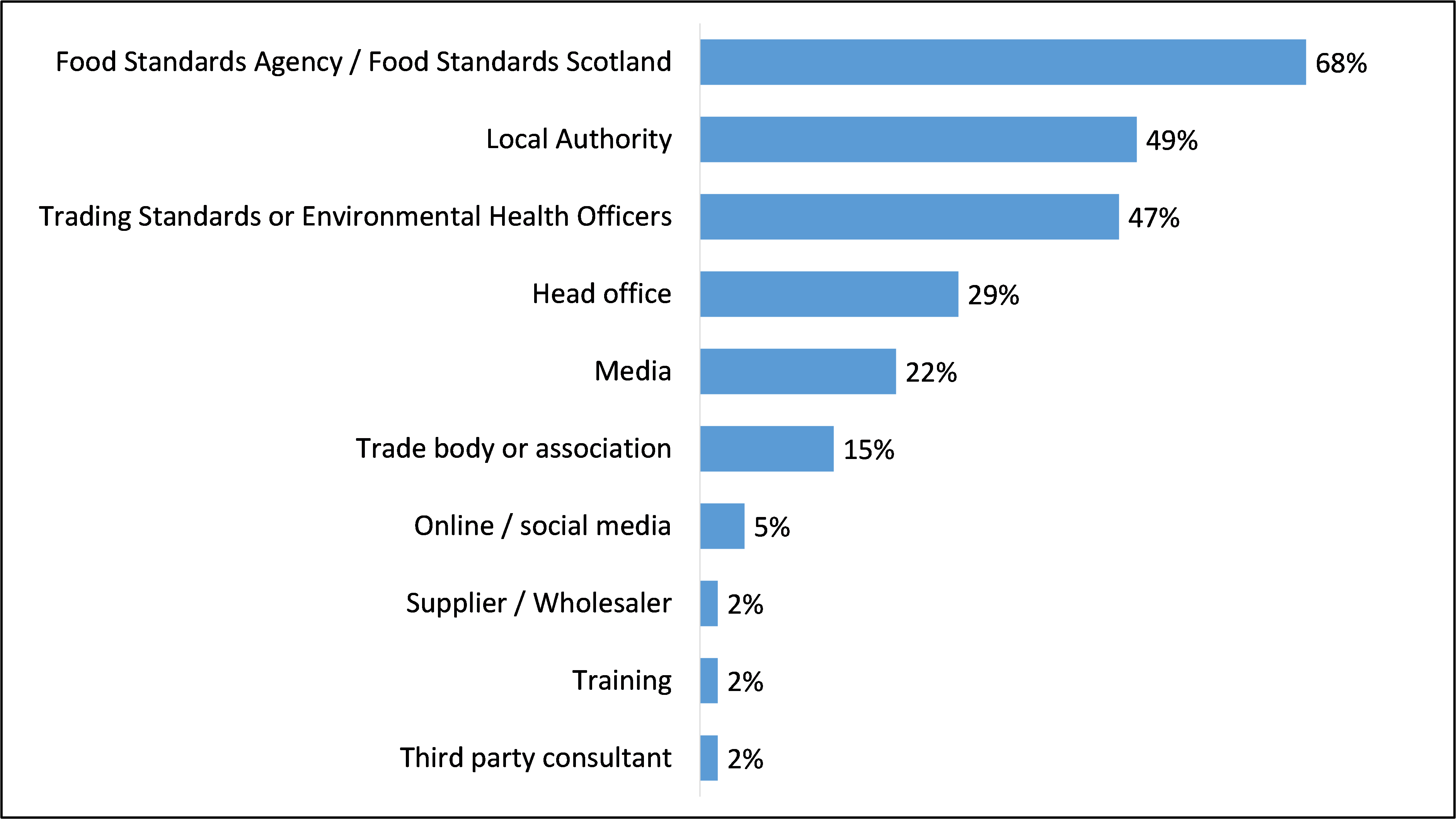
C8. Which, if any, of the following sources of support and guidance have you used to learn about the PPDS labelling requirements and how to comply with them? Base: FBOs that sell PPDS and aware of PPDS labelling requirements (766).
Support and guidance accessed from the FSA, FSS and LAs was highly regarded, with nearly all FBOs that had used these sources considering them to be useful.
- 96% of those that used support and guidance from the FSA or FSS considered it useful, with more than three fifths (62%) considering it to be very useful (n=502)
- 92% of those that used support and guidance from LAs considered it useful, with half (51%) considering it to be very useful (n=371)
During qualitative interviews, FBOs that had accessed support and guidance from the FSA or FSS explained that this typically involved accessing online resources (e.g. written guidance and videos). Most had a positive experience of using these resources, commenting that they came away equipped with a good understanding of what counts as PPDS and what needs to be included on the label.
“Guidance on FSA website is good… it tells you what constitutes PPDS and what you have to have on the labels, fairly self-explanatory if you take the time to look at it and read it, it's a very simple job to understand.”
FBO, England, Catering, 1 to 5 employees
A couple of FBOs that took part in qualitative interviews reported that they did not find FSA and FSS content helpful. This was typically down to difficulty understanding the definition of PPDS and applying it to their business setting. These FBOs therefore opted to access support and guidance from alternative sources (e.g. suppliers and consultants). Some FBOs had support and guidance from the FSA or FSS by participating in training on food labelling.
“I felt that [our supplier] had much better and simplified information than the Food Standards Agency. They had more information and they had streamlined the information, so you knew exactly what you needed to do.”
FBO, England, Catering, 11 or more employees
During qualitative interviews, many FBOs that had received support and guidance from their LA explained that this occurred at the point of an inspection or visit. This was often described as a positive experience as it gave FBOs the opportunity to get a professional opinion on whether their practices were compliant and clear up any areas of uncertainty. A few FBOs had proactively reached out to their LA for assistance via email or telephone, and a couple had received communication from their LA signposting them to support and guidance without request.
“We had a visit from [Local Authority] before Christmas…to have someone from the Authority come in and say, ‘you're doing it in the right way, whatever processes you're using is working’, that gave us a bit of confidence.”
FBO, Wales, Butcher, 1 to 5 employees
“We got sent a letter from [Local Authority] informing us when the law would be implemented about 6 weeks in advance. It contained various links to FSS web pages which were useful. Particularly the video and examples given about some common products.”
FBO, Scotland, Baker, 1 to 5 employees
Amongst those that did not access support and guidance from the FSA, FSS or LAs, the most common reasons were that they did not require support and guidance (FSA or FSS: 29%; LAs: 37%), that they received the help they needed from their head office (FSA or FSS: 21%; LAs: 15%) and that they thought other sources would be more useful (FSA or FSS: 16%; LAs: 15%). (footnote 12)
More than two thirds (68%) of FBOs said they did not require any additional information to help make compliance easier, suggesting that they were content with the support and guidance already available. A quarter (26%) of FBOs felt they would benefit from additional information. This was more likely amongst FBOs in the catering sector than those in the retail sector (31% vs 21%).
However, it was delicatessens, who sit within the retail sector, that displayed the strongest appetite for additional information (51%). With regards to size, FBOs with between 1 and 5 employees were more likely than those with 11 or more employees to identify a type of additional information that would be beneficial (29% vs 19%).
The most common topics of interest were information on the legal requirements for providing food information in general (6%), the allergens that need to be emphasised on PPDS labels (4%) and how to identify PPDS food (4%). These FBOs typically wanted this additional information to be made available in written form, either as online resources (41%) or hard copy resources (39%).
Although there was a low appetite amongst FBOs for additional support and guidance, nearly all (95%) LAs felt that further action could be taken to make it easier for FBOs to comply with PPDS labelling requirements. As presented in Figure 5.14, these actions often related to additional support and guidance, with three quarters (75%) suggesting that FBOs would benefit from general training on how to comply with the requirements, and two thirds identifying an opportunity for more guidance from the FSA and FSS on compliant packaging (67%) and best practice in terms of labelling (65%).
In addition to actions related to support and guidance, some LAs felt that that it would be easier for FBOs to comply if the scope of the PPDS labelling requirements were altered. Two thirds (67%) said that suppliers and wholesalers should be mandated to notify businesses about recipe changes, and more than half (55%) said that the requirement to label PPDS foods with full ingredients lists should be removed, with the emphasis of the legislation being placed on allergens instead.
“Previously there were labels available that had the fourteen allergens on them and businesses could tick these labels and put it on the lid of the container saying contains egg or wheat and that was quite successful. Most don’t do that now because this other requirement has come in for PPDS so in some ways it has taken us backwards.”
Local Authority, Scotland
Figure 5.14 LA views on how FBO compliance with PPDS labelling requirements could be made easier
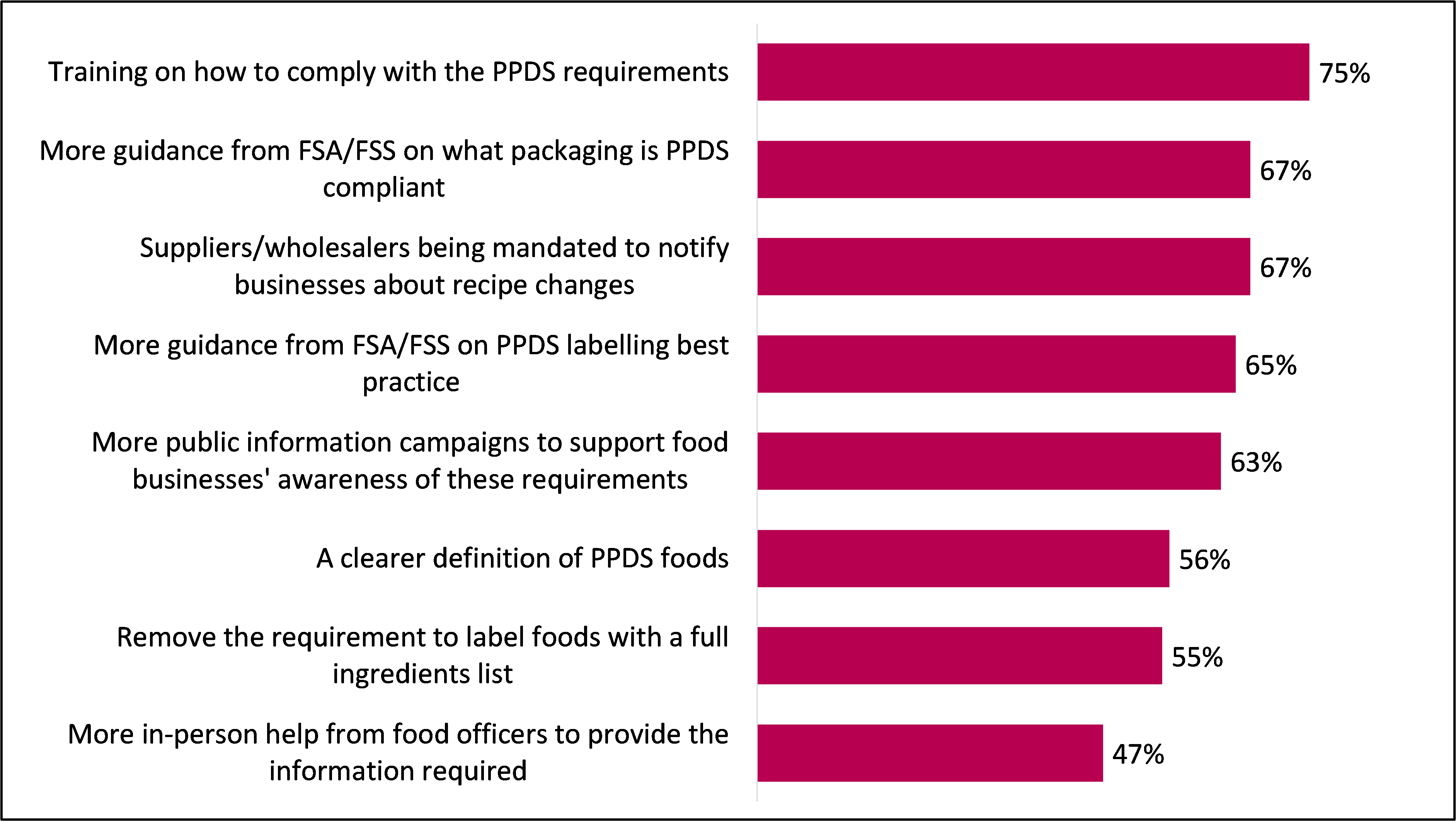
F6. What, if anything, do you think would help make it easier for food businesses to comply with PPDS labelling requirements? Base: LAs that thought FBOs find compliance less than very easy (121).
Local Authorities
Practices and processes
Nearly all LAs had checked FBO compliance with PPDS labelling requirements since they were introduced in October 2021 (98%). The small minority (2%) of LAs that had not conducted compliance checks explained that this was because their team was not responsible for checking food business compliance.
Where checks on FBO compliance with PPDS labelling requirements had been conducted, most LAs (95%) had done so by performing checks specific to PPDS foods at the same time as routine food safety inspections. However, this was seldom the only circumstance in which compliance checks were undertaken; around three quarters (73%) had also conducted reactive PPDS inspections (e.g. in response to complaints from consumers) and half (51%) had conducted visits to FBOs that were specifically focused on PPDS foods.
"It's been incorporated into routine inspections … if we're in a business for another reason like a complaint, we'll also check PPDS then if applicable. It's an additional task, not a separate activity."
Local Authority, Scotland
“There is a food standard inspection done as well as food hygiene because it is now under food law [in Scotland] so every premise will be checked for PPDS, and advice will be given if needed or if found to be deficient then it would be raised as a contravention and followed up.”
Local Authority, Scotland
“We prioritise serious allergen incidents because we get quite a number of those. And we want to deal with that rather than going around and checking every food business ... We are reactive rather than proactive with this legislation.”
Local Authority, England
LAs reported checking various aspects of the PPDS labelling requirements during visits to FBOs. As presented in Figure 5.15, nearly all (98%) checked that allergens are emphasised in ingredients lists, that the name of the food is displayed on packaging (97%), that there is a system for labelling in place (97%) and checked where food is packed (96%).
Figure 5.15 Aspects checked during PPDS compliance checks
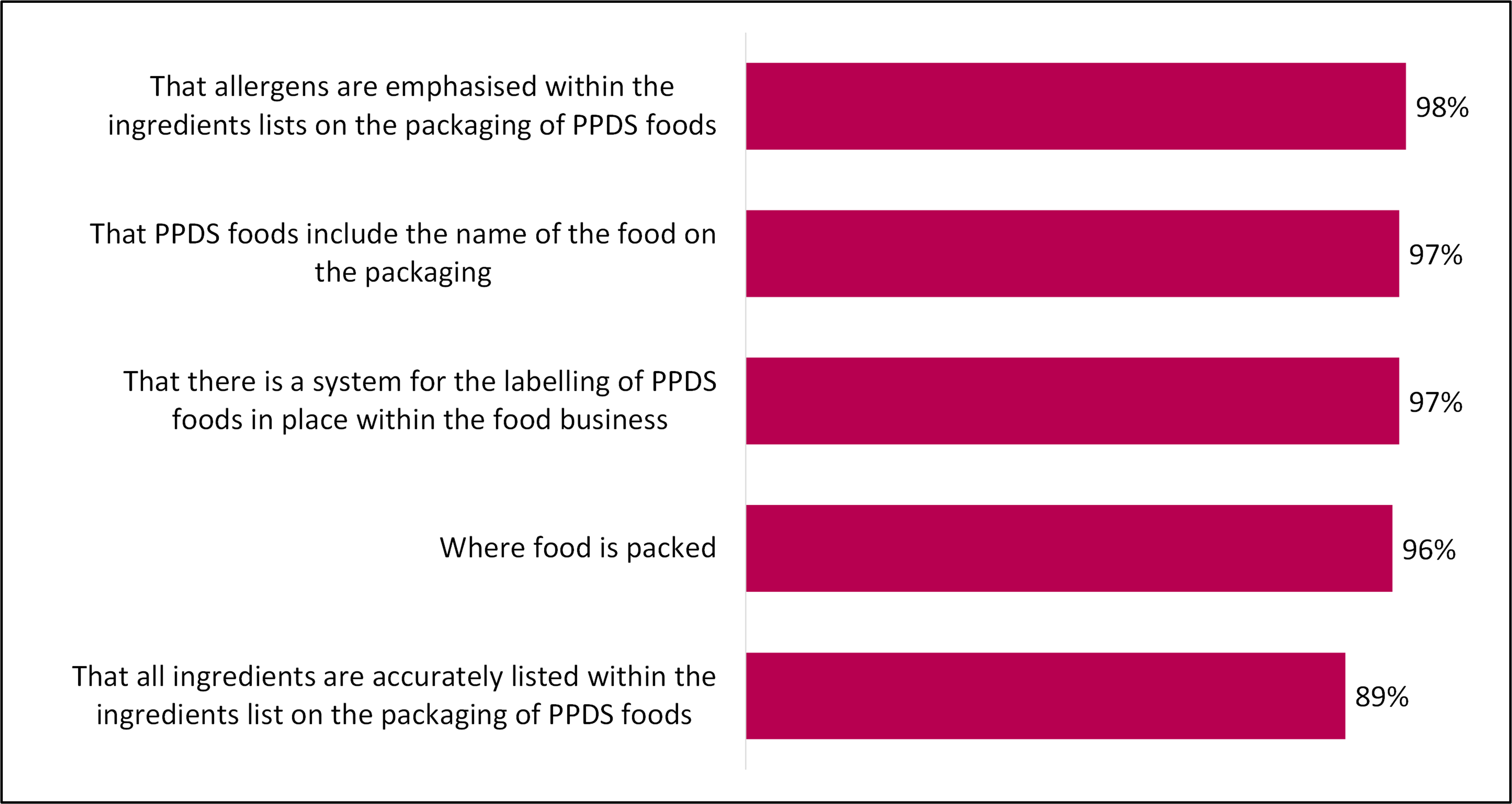
C2. When checking food business compliance with PPDS labelling requirements, do you check any of the following? Base: All LAs that have conducted compliance checks (123).
Nearly all (95%) LAs had encountered at least some cases of non-compliance during visits to FBOs since PPDS labelling requirements were introduced. Close to nine in ten LAs (89%) had observed there being no labels on the packaging of PPDS foods, and more than four fifths (84%) had observed no ingredients lists with a similar percentage (82%) observing incomplete ingredients lists. Other forms of non-compliance encountered by LAs are presented in Figure 5.16.
Figure 5.16 Types of non-compliance observed by LAs
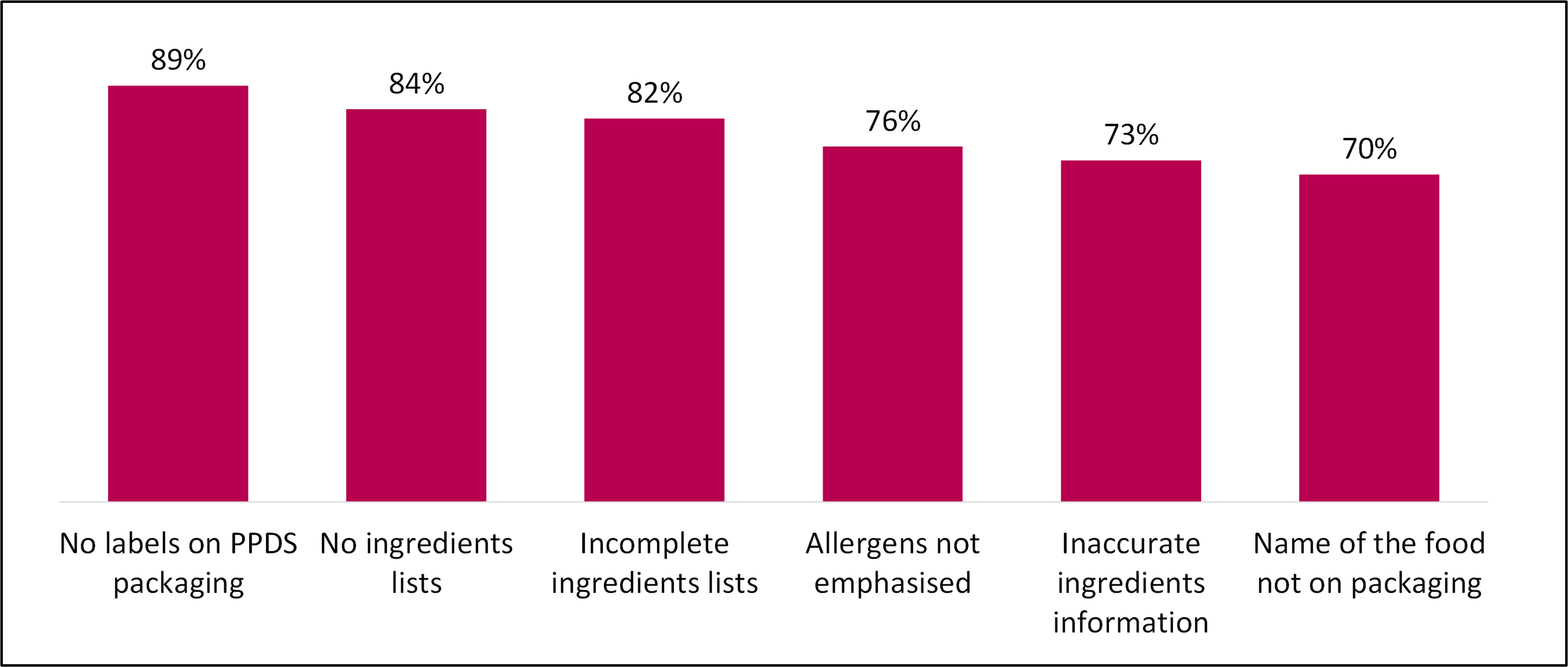
D5. Have you found any of the following examples of non-compliance in relation to PPDS foods in the businesses you've checked? Base: LAs that have conducted compliance checks (123).
When non-compliant practices were encountered, most LAs (91%) had responded by signposting FBOs to guidance and support , or by providing them with written (86%) or verbal (84%) advice. Some LAs reported escalating incidents of non-compliance and taking enforcement action. For example, written warnings had been issued by 40%, improvement notices had been issued by 8% and cautions had been issued by 2%.
During qualitative interviews, many LAs explained that their focus for the first year of the PPDS labelling requirements had been to educate FBOs and support them with compliance rather than pursuing enforcement. Where FBOs were found to be non-compliant, LAs had typically explained the contravention to FBOs, advised them to stop selling the PPDS food in question and arranged a re-visit. When LAs did report taking enforcement action, this was typically in instances where FBOs did not heed their advice or were found to still be non-compliant at the point of re-inspection. It was widely expected by LAs that enforcement action would become more commonplace over time as FBOs become more familiar with PPDS labelling requirements and repeat visits are conducted.
“We have made businesses aware of a contravention if they haven’t complied but no further action like notices of court. We have taken a softer approach to make sure people are aware first and if they don’t follow through, we issue a contravention and follow up to make sure that is remedied.”
Local Authority, Scotland
“We would always follow a graduated approach anyway with a new requirement and at this stage it is still about education, advice, and guidance … two businesses had no labelling so we told them ‘until you have the correct labelling you cannot sell it’. They acted on it straight away.”
Local Authority, England
Experience of compliance checks
As presented in Figure 5.17, most LAs said that checking compliance with PPDS labelling requirements was easy (71%), with 7% of the view that it was very easy. However, a quarter (25%) of LAs said that compliance checks were difficult.
Figure 5.17 LA experience of compliance checks
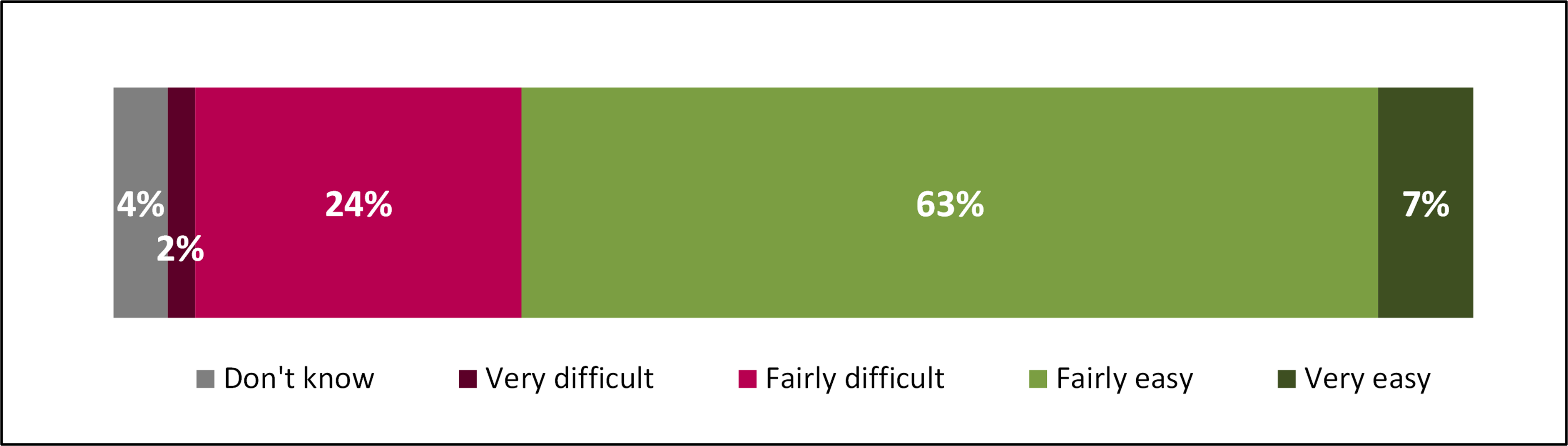
D1. How easy or difficult have you found it to check compliance with the PPDS labelling requirements? Base: LAs that have conducted compliance checks (123).
Of the small number of LAs that reported having difficulty with compliance checks (25%, n=31), the main reasons were: not having enough internal resource to visit and inspect all businesses to check for PPDS compliance (n=21), uncertainty around the definition of some or all PPDS foods (n=20) and difficulty checking the accuracy of PPDS ingredients lists (n=14).
During qualitative interviews, these same challenges were commonly mentioned by LAs that reported finding compliance checks to be easy overall. Many of these LAs said that compliance checks had been complicated by a lack of awareness and understanding amongst FBOs under their jurisdiction and, in some cases, amongst their own staff. Particularly in the early stages of the PPDS labelling requirements being introduced.
“It was difficult for officers to get their heads around what things were PPDS and what were not. So, trying to explain it to FBOs was difficult.”
Local Authority, England
“SMEs [small medium enterprises] struggle with these things, because they don't have the technical guidance and they quite often rely on us to be almost their consultants and help them. This is not supposed to be our job, but sometimes it's easier just to try explaining everything and this requires our officers sitting there and trying to help them. And that means spending a lot of time with businesses.”
Local Authority, Scotland
Many LAs said that constraints on internal resource and time had made it more difficult for them to check FBO compliance with PPDS labelling requirements. This was sometimes attributed to LAs having a backlog of FBO inspections to conduct following the COVID-19 pandemic.
“Time constraints are a big issue because we are limited to the time we can spend on an inspection and there are other inspections we have to carry out with a lot of admin we have to do.”
Local Authority, Scotland
“When PPDS came in, we were already facing a massive backlog of the ordinary work, without having something else to work on.”
Local Authority, Wales
Amongst the LAs that had conducted compliance checks and found the process less than ‘very easy’, the top three things that they felt would make compliance checks easier were: more resources for LAs (e.g. funding and staff) (29%), greater clarity on what food products are covered by PPDS labelling requirements (22%) and materials for LAs to share with FBOs (e.g. guidance handouts) and issue to FBOs (e.g. improvement notices) (21%).
Support and guidance
Virtually all (99%) LAs had undertaken activities to support and increase compliance with PPDS labelling requirements since they came into effect. As illustrated by Figure 5.18, the most common activity was signposting to FSA or FSS guidance and resources (85%). This was followed by visits to establishments to offer guidance in person (52%) and sending information with FBOs via physical letters and newsletters (44%) or email and digital newsletters (44%).
Figure 5.18 LA activities to support and increase compliance
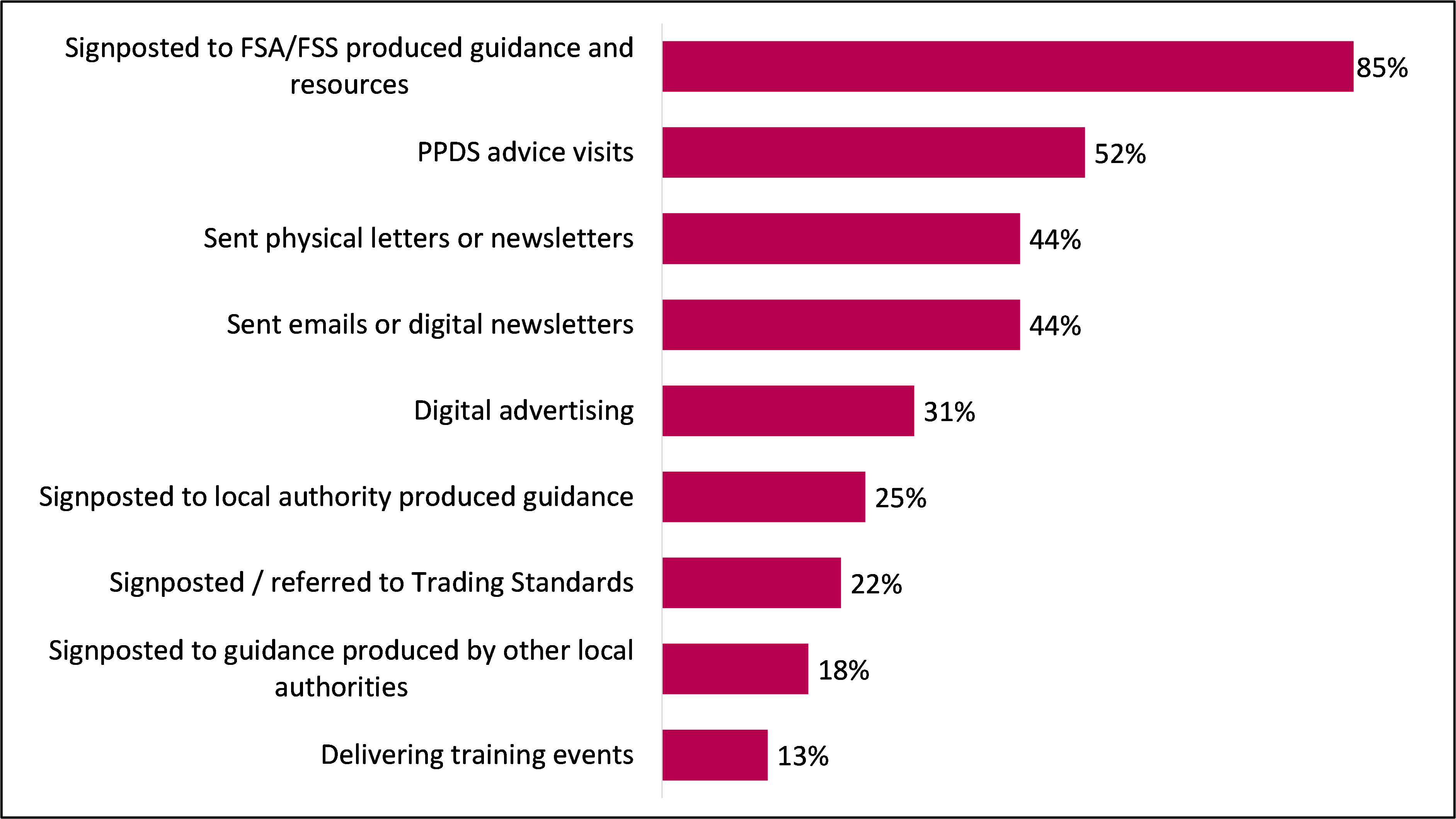
C6. What activities, if any, have you used to support and increase compliance with PPDS labelling requirements since October 2021? Base: All LAs (126).
During qualitative interviews, many LAs explained that they had undertaken a blanket approach to activities designed to support and increase compliance with PPDS labelling requirements, encompassing all businesses in the LA. For example, many reported distributing links to FSA and FSS resources or to resources they had developed themselves via email ‘mailshots’, postal campaigns, and social media campaigns ahead of 1 October 2021. A few said they held webinars on PPDS labelling requirements which were open to any businesses that were interested in attending.
“We have provided free online webinars for businesses on allergens and PPDS. It was successful, with hundreds of businesses attending and positive feedback. The drawback is that these businesses are the ones that are keen to comply, and generally these are not the businesses that are failing [on compliance checks].”
Local Authority, England
“We used email to get in touch with all the businesses we had on our database to say this is coming in and what it will mean for your business; ‘here is the guidance and links so have a look online’ and we encouraged them to use the online allergen training again, which is on the FSS website.”
Local Authority, Scotland
Some LAs that took part in qualitative interviews said they had decided to take a targeted approach and only conducted activities with FBOs where the PPDS labelling requirements were thought to be most relevant. For example, a few LAs had focused their efforts on bakers and butchers while one LA said they had sent communications to FBOs where there was a greater risk of non-compliance.
“I drafted an email using an FSS template and information that they had provided to do promotional work, and basically took a list of food businesses within [Local Authority] that we thought would potentially have this type of product, and we sent out emails.”
Local Authority, Scotland
Some LAs did a combination of general and targeted activities. An example of this can be seen in the case study presented in Figure 5.19, which covers the experience of a Scottish LA and an FBO under their jurisdiction.
A few LAs had not carried out any activities beyond the delivery of advice and guidance during routine inspections. Some of these LAs said that they lacked the time and resources to be able to undertake a communications campaign or host training events, while a few were of the opinion that it was not their responsibility to carry out such activities.
“It's something we'd expect the FSA to publicise rather than us, we certainly don't have the resources for it… there aren't enough Food Officers out there, so we have to be reactive rather than proactive.”
Local Authority, England
Figure 5.19 Case study: support and guidance (accessible version)
A Scottish Local Authority that had undertaken multiple activities to support and increase compliance with the PPDS labelling requirements. This included:
- Sending physical letters
- Digital advertising
- Signposting to FSS produced guidance and resources
- In-person visits by Environmental Health Officers
- Creating a dedicated PPDS mailbox
The Local Authority began delivering these activities in the lead up to the PPDS labelling requirements being introduced. Most activities were aimed at all businesses within the Local Authority. However, they also targeted catering facilities within institutions (e.g. schools and hospitals) with physical letters as they were considered to be high-risk.
"There was some proactive stuff we shared with businesses in late 2021 through visits and we had information on social media.”
A bakery, located in the same Local Authority, with between 1 and 5 employees. The owner recalled receiving a visit from an Environmental Health Officer ahead of the PPDS labelling requirements being introduced, and being advised to change their labelling practices from October 2021.
“An Environmental Health Officer visited our market stall as part of a drive to inform all local businesses…. we had a chat about the requirements and he also gave an example of something we'd need to change… he pointed at a cake that was wrapped in plastic and told us that from October 1st we’d have to label it.”
They had not received any further support and guidance from the Local Authority. With hindsight, while the conversation with the Environmental Health Officer was useful, they would have liked to have been given a physical document to reference. The FBO has used FSA and FSS resources to develop an understanding of the PPDS labelling requirements and how best to comply with them. Video clips were identified as particularly useful.
-
9% of all consumers with food hypersensitivities reported never buying PPDS foods (n=170).
-
89% of all consumers with food hypersensitivities purchased PPDS foods and checked labels on PPDS foods (n=1,606).
-
90% of FBOs that sold PPDS food reported labelling all ingredients or emphasising allergens on the packaging (n=781).
-
90% of FBOs that sold PPDS food reported labelling all ingredients or emphasising allergens on the packaging (n=781).
-
The food industry’s provision of allergen information to consumers | Food Standards Agency.
-
[1] 1% of FBOs that found compliance difficult were unable to comment on the source of difficulty.
-
87% of all LAs reported that FBOs found compliance difficult (n=109).
-
Unpublished internal research conducted by the FSA.
-
This aligns with the findings presented Chapter 4, where it was reported that those with between 1 and 5 employees were less likely than those with 11 or more employees to be aware of the PPDS labelling requirements (87% vs 97%).
-
83% of all FBOs that sold PPDS foods and were aware of the PPDS labelling requirements (n=766).
-
33% of FBOs that sold PPDS foods and were aware of the PPDS labelling requirements did not use FSS or FSA support and guidance (n=264). 52% of FBOs that sold PPDS foods and were aware of the PPDS labelling requirements did not use LA support and guidance (n=395).