Chapter 2.6 Transmissible Spongiform Encephalopathy (TSE) Testing
1. Introduction 2. BSE Testing in Cattle 3. Sheep TSE Sampling and Submission 4. Sheep TSE Testing: Form Completion 5. Annexes
Sections
3. Sheep TSE Sampling and Submission
1. Introduction
In this section
1.1 Purpose
1.1.1 Background
Cattle, sheep and goats can be susceptible to a group of brain diseases known as transmissible spongiform encephalopathies (TSEs). The best known of these diseases is Bovine Spongiform Encephalopathy (BSE) (mad cow disease) in cattle. BSE has been linked to the human TSE disease, variant Creutzfeldt-Jakob disease (vCJD).
Since 1990 the European Community (EC) has adopted a series of measures to protect human and animal health from the risk of TSE.
It is appropriate in the view of the magnitude of the risk posed to human and animal health by certain TSEs to adopt specific rules for their prevention, control and eradication.
EC Member States must carry out an annual programme for monitoring BSE and scrapie (a similar disease affecting sheep and goats).
In order to ensure that the rules concerning the prevention, control and eradication of TSEs are observed, it is necessary for samples to be taken for laboratory testing on the basis of an established protocol which would give a full epidemiological picture of the situation as regards TSE.
The TSE disease surveillance statistics for UK are published online.
1.1.2 TSE suspects
These instructions are not intended to apply to animals suspected of suffering from a TSE which must be dealt with in accordance with chapter 6 on ‘Notifiable diseases’.
1.1.3 Health and safety
When following these instructions all FSA staff must adhere to the FSA health and safety guidelines.
Reference: See guidelines in the Health and Safety Manual located on Digital Workplace.
1.2 Legislation
1.2.1 Relevant legislation
(EC) 999/2001 (as amended) lays down rules for the prevention, control and eradication of certain TSEs.
The Transmissible Spongiform Encephalopathies (England) Regulations 2018 and The Transmissible Spongiform Encephalopathies (Wales) Regulations 2018 implement Regulation (EC) 999/2001 in England and Wales.
(EU) 2019/627, Article 29 enquires official controls to check that the FBOs procedures guarantee compliance with relevant community legislation on TSEs.
The Transmissible Spongiform Encephalopathies (England) Regulations 2018 (S.I. 2018 No. 731)
1.2.2 Monitoring programmes
(EC) 999/2001 requires that Member States monitor and test for TSE in certain animals from different categories, including
- bovine animals slaughtered for human consumption
- bovine animals not slaughtered for human consumption
- ovine and caprine animals slaughtered for human consumption
- ovine and caprine animals not slaughtered for human consumption
- monitoring in infected flocks
1.2.3 Legislation relating to TSE testing of cattle
The official controls on cattle slaughtered for human consumption and BSE tested are based on the following pieces of legislation:
- Regulation (EC) 999/2001 (as amended) which sets out the TSE controls including those for Specified Risk Materials (SRM) and Bovine Spongiform Encephalopathy (BSE) testing
- Regulation (EC) 1069/2009 which sets out specific rules for the handling and disposing of animal by-products
- Regulation (EU) 2019/627 Article 29 which sets out specific rules for Official Veterinarians (OVs) in slaughterhouses
- Commission Decision 2009/719/EC (as amended) which authorised certain Member States to revise their annual BSE monitoring programme
- the Transmissible Spongiform Encephalopathies (England) Regulations 2018
- the Transmissible Spongiform Encephalopathies (Wales) Regulations 2018
1.3 Disposal
When the text refers to material being disposed of as Category 1 Animal By-Product (ABP) SRM must be destroyed by incineration or rendering and then incineration at approved premises (as opposed to other Category 1 ABP, which can be rendered and land filled).
The OV must verify that this material is consigned to approved premises and obtain confirmation that it has been incinerated.
Reference: (EC) 999/2001 and (EC) 1069/2009, Chapter II, Article 12 (a).
Reference: See chapter 2.7 on ‘SRM’ and chapter 2.8 on ‘ABP’ for additional information.
Note: List of approved premises in Great Britain can be accessed on the APHA website.
2. BSE testing in cattle
In this section
2.2 BSE testing of bovines in slaughterhouses
2.3 Standard operating procedures for BSE sampling and testing
2.4 Identification of cattle to be tested
2.7 Alternative sampling techniques
2.8 Traceability of sample to carcase
2.9 Samples packaging and delivery
2.10 Traceability of all parts: tested animal to carcase
2.12 Retention of all body parts
2.17 ‘Insufficient test’ result
2.18 ‘Inconclusive test’ result
2.1 BSE testing requirements
2.1.1 Bovines born in UK or certain other Member States- testing requirements from 1 March 2013
The BSE testing requirements outlined in this paragraph apply from 1 March 2013 and relate only to cattle born in one of the EU Member States listed in the table below:
- All ‘at risk cattle’ aged over 48 months (birth date + four years and 1 day) (O48M).
Note: See the sub topic 2.1.3 on ‘Animals that require testing’ for definition of ‘at risk cattle’.
Country | Eartag ID prefix |
---|---|
Austria | AT |
Belgium | BE |
Croatia | HR |
Cyprus | CY |
Czech Republic | CZ |
Denmark | DK |
Estonia | EE |
Finland | FI |
France | FR |
Germany | DE |
Greece | EL |
Hungary | HU |
Ireland | IE |
Italy | IT |
Latvia | LV |
Lithuania | LT |
Luxembourg | LU |
Malta | MT |
Netherlands | NL |
Poland | PL |
Portugal | PT |
Slovak Republic | SK |
Slovenia | SI |
Spain | ES |
Sweden | SE |
United Kingdom (including Channel Islands and Isle of Man) | UK |
2.1.2 Bovines born elsewhere- testing requirements
Cattle with ear tags that do not have the prefixes listed above must be BSE tested if: over thirty months of age (OTM) if healthy at slaughter or over 24 months of age (O24M) in cases of emergency slaughter or where identified as sick at ante mortem inspection.
Note: See sub topic 2.1.3 on ‘Animals that require testing’ for definition of ‘at risk cattle’.
Note: Cattle born in a Third Country (not one of the 28 EU Member States) and imported into a Member State will be re-tagged with a tag showing the importing Member State’s prefix (unless slaughtered within 20 days). The Third Country import information should be available in the passport.
2.1.3 Animals that require testing
The following animals require testing:
- all O48M (EU26) / O24M (non EU26) bovine animals that have undergone:
- emergency slaughter in accordance with, point 1 of Chapter VI of Section I of Annex III to Regulation (EC) No 853/2004, or
- an ante-mortem inspection with observations concerning accidents, or serious physiological and functional problems, or signs in accordance with 2019/627, Article 43(4):
- that welfare has been compromised; or
- of any condition which might adversely affect human or animal health, paying particular attention to the detection of zoonotic diseases and animal diseases for which animal health rules are laid down in EU legislation.
- animals OTM (non EU26) healthy at slaughter.
2.1.4 Exceptions
Some casualty animals or animals with abnormalities may be exempted from the testing requirement. These animals are:
- TB reactors and TB inconclusive reactors – unless suffering from a concurrent disease or abnormality as outlined in this instruction
- cattle with localised lesions or conditions with no systemic affects – examples include minor foot lameness, ringworm, superficial tumours, minor hernias, minor abscesses, localised mastitis or mild conjunctivitis; in such cases, the OV must be content that there are no signs of concurrent disease
Note: The above examples are intended as a guide. It is for the OV to make a professional judgement in each situation as it arises, in line with these instructions.
The following table illustrates the BSE testing requirements for all cattle:
Exceptions
Country of birth | Ear tag country codes |
BSE testing age from 1 March 2013 Healthy slaughter cattle |
BSE testing age from 1 March 2013 Emergency slaughter and sick at ante mortem (fit for human consumption) |
BSE testing age from 1 March 2013 Fallen stock (not fit for human consumption) |
---|---|---|---|---|
Austria | AT | No Testing Required | Over 48 Months | Over 48 Months |
Belgium | BE | No Testing Required | Over 48 Months | Over 48 Months |
Croatia | HR | No Testing Required | Over 48 Months | Over 48 Months |
Cyprus | CY | No Testing Required | Over 48 Months | Over 48 Months |
Czech Republic | CZ | No Testing Required | Over 48 Months | Over 48 Months |
Denmark | DK | No Testing Required | Over 48 Months | Over 48 Months |
Estonia | EE | No Testing Required | Over 48 Months | Over 48 Months |
Finland | FI | No Testing Required | Over 48 Months | Over 48 Months |
France | FR | No Testing Required | Over 48 Months | Over 48 Months |
Germany | DE | No Testing Required | Over 48 Months | Over 48 Months |
Greece | EL | No Testing Required | Over 48 Months | Over 48 Months |
Hungary | HU | No Testing Required | Over 48 Months | Over 48 Months |
Ireland (ROI) | IE | No Testing Required | Over 48 Months | Over 48 Months |
Italy | IT | No Testing Required | Over 48 Months | Over 48 Months |
Latvia | LV | No Testing Required | Over 48 Months | Over 48 Months |
Lithuania | LT | No Testing Required | Over 48 Months | Over 48 Months |
Luxemburg | LU | No Testing Required | Over 48 Months | Over 48 Months |
Malta | MT | No Testing Required | Over 48 Months | Over 48 Months |
Netherlands | NL | No Testing Required | Over 48 Months | Over 48 Months |
Poland | PL | No Testing Required | Over 48 Months | Over 48 Months |
Portugal | PT | No Testing Required | Over 48 Months | Over 48 Months |
Slovakia | SK | No Testing Required | Over 48 Months | Over 48 Months |
Slovenia | SI | No Testing Required | Over 48 Months | Over 48 Months |
Spain | ES | No Testing Required | Over 48 Months | Over 48 Months |
Sweden | SE | No Testing Required | Over 48 Months | Over 48 Months |
UK (including Channel Islands and Isle of Man) | UK | No Testing Required | Over 48 Months | Over 48 Months |
Bulgaria | BG | Over 30 months | Over 24 months | Over 24 months |
Romania | RO | Over 30 months | Over 24 months | Over 24 months |
All other countries | UK (if not slaughtered within 20 days of import; import information is shown on the inside back page of the cheque-book style passport) | Over 30 months | Over 24 months | Over 24 months |
2.2 BSE testing of bovines in slaughterhouses
2.2.1 Introduction
FBOs processing bovines that require BSE testing must comply with the specific legal requirements for the testing and should have standard operating procedure (SOP) for ensuring their correct implementation.
An approved required methods of operation (RMOP) is no longer required but FBOs are expected to have agreed a SOP with the FSA. The previously agreed RMOP could be used as an SOP if it remains valid and up-to-date.
The agent of the BSE is a food safety hazard and should be included in the HACCP based procedures for the establishment. The SOP for BSE testing along with the SRM removal should be part of the control measures for that hazard (i.e. prions).
2.2.2 Sampling area
The sampling area must be suitable, safe and clean with hygienic facilities for the taking of brain stem samples, for example, dedicated table or room or sampling on the line.
2.2.3 Trained plant staff
Sampling cannot be undertaken unless the FBO provides staff that are suitably trained and competent to carry out brain stem sampling. The OV should use the FBO’s training records to ascertain that there are sufficient suitably trained staff.
The FBO may contact CSCOneHealthGeneral@apha.gov.uk for the training requirements of their staff. The FBO should keep the training records as set by APHA and update them for any internal cascading among other members of the FBO’s staff.
2.2.4 Passport handling
The FBO must have a system to ensure (as far as reasonably possible) that slaughtered cattle match the details shown on the passport (ear tag number, breed, sex and age).
2.2.5 Traceability system
A robust traceability system must be established through which the ear tag number and kill number is associated with the sample, carcase and body parts.
This system must also:
- define the criteria by which the FBO identifies the animal/s requiring testing
- reconcile the number of cattle that should have been tested and the number of samples despatched to the laboratory
2.2.6 Ensuring eligibility
It is the FBOs responsibility to ensure that cattle presented for slaughter:
- have the correct ear tags in place
- are accompanied by a valid passport
- are eligible for slaughter
The FBO must keep a record of cattle movements onto the premises.
Reference: The Cattle Identification Regulations 2007 and the Cattle Identification (Wales) Regulations 2007.
Reference: See chapter 2.5 on ‘Animal identification’ for additional information.
2.2.7 Storage facilities
Suitable and secure facilities must be available to retain the carcase, body parts including hide and blood, and by-products, until the test results are received.
Note: Hides can be delivered to a hide premises before the test result is received, provided that the hides are kept under official control until the BSE test results are received.
Note: if the test results are not received when the body parts are disposed of, they must be disposed of as SRM by incineration.
2.2.8 Cold inspection
Delayed post-mortem inspection (‘cold inspection’) may be permitted in small establishments after an assessment has been made by the FVC as to the suitability of the premises.
When permitted, removal of the brain stem sample will need to be done in the presence of FSA staff.
The SOP for the establishment must place special emphasis on the measures to be taken to ensure full traceability of carcases and all body parts.
2.2.9 Office equipment
There should be suitable office facilities with:
- a photocopying machine
- a system for the receipt of the test results from the laboratory, either by fax or by other electronic means
2.2.10 FSA pre-requisites
OVs and MHIs must have received training before carrying out official controls on the processing of cattle requiring BSE testing.
The training contains further guidance to that recorded in this document. Refer to training or your line manager for any further assistance.
2.3 SOP for BSE sampling and testing
2.3.1 SOP agreement
FBOs should agree a SOP with the FSA, which will continue to maintain food safety and BSE controls. The SOP should be part of the HACCP-based procedures and could be based on the previously agreed RMOP.
Reference: See Annex 1 for a sample of the former RMOP which could be used as a reference for drafting or checking the SOP.
OVs must ensure that the SOP contains all the steps of production with detailed procedures for each step.
OVs must only accept a SOP when they are satisfied that the controls are robust enough to provide confidence in the security of the entire system.
2.3.2 Audit and verification
SOP will be subject to verification or audit by:
- FVC
- Veterinary Assurance Team
- Internal Audit Unit
- Independent auditors
2.3.3 Hazard identification and control plan
The FBO must review their HACCP plan when slaughtering cattle that require BSE testing, to ensure hazards are identified and controlled. The control measures for BSE related hazards should include the SOP for BSE sampling and testing.
2.4 Identification of cattle to be tested
2.4.1 Identification procedure
Lairage procedures and pre-slaughter checks must be robust to ensure all cattle that require BSE testing are identified. The table on the following page details both FBO and FSA responsibilities.
FBO responsibility | FSA responsibility |
---|---|
Must implement in the lairage a positive release system for cattle that require BSE testing. Must ensure bovines born in or imported into the UK before 1 August 1996 are rejected for slaughter for human consumption. Must ensure BSE testing of cattle that were born in one of the countries listed in the Annex to Commission Decision 2009/719 [as amended] aged 48 months and one day or more that were subject to emergency slaughter or where the OV judges testing is necessary at ante mortem inspection. Must ensure cattle that were not born in one of the countries listed in the Annex to Commission Decision 2009/719 (as amended) are tested if aged over 30 months or over 24 months if subject to emergency slaughter or where the OV judges testing is necessary at ante mortem inspection. (The countries listed in the Annex are the 25 EU Member States as listed in the table in sub-topic on ‘Bovines born in UK or certain other Member States’ in this chapter.) Bovines for BSE testing must be marked by a suitable, robust and reliable method prior to slaughter (for example, spray marking, tagging). |
FSA staff must verify
FSA staff must also perform 10% physical checks of ear tag / passport reconciliation in the lairage. Passport and ID checks, including DOB and age on the % of animals required according to the percentage in force at the establishment in question (See chapter 2.5 on ‘Animal identification’, section 4). The OV must ensure that a form TSE 6/4 is completed and issued to the FBO for all animals requiring BSE testing intended for human consumption and not identified by the FBO |
2.4.2 Bovines not eligible for human consumption
Animals born in or imported into the UK before 1 August 1996 are prohibited from entering the food chain.
Animals identified by the FBO as being born prior to 1st August 1996 (or having the default birthdate 11/11/1111 on their identity documents) must be notified to the OV, who must inform the FVC.
These cattle must be destroyed as fallen stock and be BSE tested when they are culled or die.
Guidance on fallen stock can be found online.
If the premises are already approved for BSE testing of bovines, the abattoir may submit a sample for BSE testing using BSE test code FSCA2 and arrange for the body to be disposed of as Category 1 ABP for incineration.
OVs must be vigilant that these cattle are not slaughtered for human consumption unless they were imported into the UK on or after 1 August 1996.
Reference: The TSE (Wales) Regulations 2018
The TSE (England) Regulations 2018
2.4.3 Issue of form to test animal not for human consumption
The OV is to issue to the FBO form TSE 6/5 for animals identified as requiring BSE testing, but that are not eligible for human consumption.
Reference: See chapter 9 on ‘Forms’ for a copy of TSE 6/5.
2.4.4 Identification documents
For the different types of documents that accompany the cattle and the different tagging systems, depending on the age, see chapter 2.5 on ‘Animal Identification’.
2.4.5 Lairage facilities
The establishment should have a lairage with suitable facilities to:
- check information on the passports prior to slaughter and make a physical check to match the passport numbers with the ear tags
- segregate cattle that require BSE testing from those that do not
2.5 Slaughtering schedule
2.5.1 Segregation of animals requiring testing
All eligible animals requiring BSE testing must be identified following the means of identification detailed in the SOP (for example, spray marking, tagging) and slaughtered separately (preferably as the last down the line) clearly identifiable from other animals and their products.
2.5.2 Exception
For welfare reasons, an animal requiring BSE testing may need to be slaughtered immediately.
2.6 Sampling procedure
2.6.1 Sampling technique
The collection of the brain stem sample could be carried out either:
- when the head is still attached to the carcase
OR
- after separating the head from the carcase and placing it on a dedicated table or on a line
The low-pressure water / hose and the low pressure compressed air methods may be used only once the head has been separated from the carcase.
The FBO must ensure that they have sufficient stock of consumable equipment required for sampling (including labels where used) before commencing processing.
2.6.2 Sampling on a dedicated table
A dedicated table and associated facilities for record keeping must be made available.
The distance of the sampling area from the line does not need to be excessive but sufficient to avoid any risk of cross-contamination (splashing) of fresh meat during the sampling process.
2.6.3 Sampling with the head attached to or separated from the carcase
If sampling is carried out when the head is still attached to or separated from the carcase, preventive measures such as spoon washing and sterilisation (if a stainless steel spoon is used for sampling) or disposal of sampling equipment as clinical waste (if plastic spoon and forceps are used) after each sample is taken, must be employed to avoid the risk of cross-contamination of the sample.
2.6.4 Operatives undertaking sampling
Brain stem samples must be taken by trained plant operatives only.
The FBO:
- is responsible for ensuring there are sufficient staff trained and competent in taking brain stem samples
- should keep a record of all trained operatives
- MUST notify FSA staff if any training is to be undertaken using heads of bovines that don’t require BSE testing
2.6.5 FSA supervision
FSA staff must not undertake any sampling but must carry out the following supervision:
Check | Frequency | Records |
---|---|---|
|
|
Day Book |
|
|
TSE 6/9 |
|
|
TSE 6/11 |
2.6.6 Loss of correlation
If correlation or sample identity has been lost, carcases and offal after the last correctly correlated brain stem sample must be disposed of as Category 1 SRM by incineration. All samples must still be sent for testing.
Reference: See also sub-topic 2.8.7 on ‘FSA action: loss of correlation’ in this chapter.
2.6.7 Brain stem sample quality
The FBO is responsible for ensuring that the brain stem sample submitted for analysis is of adequate quality to allow the lab to carry out the test and provide a result.
Note: All parts of all tested cattle for which results are not yet available must either be retained under official control or destroyed as Category 1 (SRM) by-product by incineration.
2.6.8 Disposal of sampling equipment
Following sampling, all testing equipment (for example, plastic spoon, plastic forceps and gloves) must be disposed of by the FBO as clinical waste in accordance with legal requirements.
The FBO must be aware that if the sampling material is not disposed of after each use there is a potential risk of cross contamination from a possible positive brain stem sample to other brain stem samples.
2.7 Alternative sampling techniques
2.7.1 Sampling with low pressure water/hose method
The following pre-requisites must be met before the extraction of the brain stem sample with low water pressure / hose method is carried out:
- the tongue has been removed
- any harvesting of head meat has been carried out
- the risk of cross- contamination with brain exudate of other meat is minimised or avoided
To minimise or avoid the risk of cross-contamination the following procedures should be carried out before and during the removal of the brain stem sample:
Step 1 | Minimise or avoid the risk of cross contamination |
Before the brain stem is removed | After the head is removed from the carcase:
|
Step 2 | Minimise or avoid the risk of cross contamination |
During the removal of the brain stem |
Once the above procedures are complete the use of the low-pressure water / hose method in obtaining the brain stem sample can be applied. The primary measures to be used to ensure that cross-contamination of any other meat nearby with brain exudate is minimised or avoided are: (i) Ensuring adequate space between the head and any other meat intended for human consumption so as to minimise cross-contamination dependent on direct contact, splash or possibly aerosol spray. This can be done in a number of ways such as:
(ii) Minimising cross-contamination from personnel by:
Given that each abattoir will be different, it will be for the FBO to agree with the OV and the FVC the most effective combination of methods required to minimise cross-contamination. |
2.7.2 Sampling using low pressure air compression
The following pre-requisites must be met before the extraction of the brain stem sample by means of the low pressure compressed air method is carried out:
- the tongue has been removed
- harvesting of head meat has been carried out
- the risk of cross-contamination with brain exudate of other meat is minimised or avoided
- the head complies with the following criteria:
- the bolt hole is not too large, obstructed or wrongly orientated and multiple bolt holes are absent; good stunning practices will be required to ensure these criteria
- aside from the bolt hole there are no other entry points into the cranial cavity / sinuses; in effect, if horns are removed care should be taken not to breach the cranial cavity
If the above criteria are not complied with, samplers must be competent in resorting to use of the spoon method in extracting the sample.
To minimise or avoid the risk of cross-contamination the following procedures should be carried out before and during the removal of the brain stem sample:
Step 1 | Minimise or avoid the risk of cross-contamination |
Before the brain stem is removed | After the head is removed from the carcase:
|
Step 2 | Minimise or avoid the risk of cross-contamination |
During the removal of the brain stem |
Once the above procedures are complete, the use of the low pressure compressed air method in obtaining the brain stem sample can be applied. The primary measures to be used to ensure that cross-contamination of any other meat nearby with brain exudate is minimised or avoided are as follows: (i) A plastic bag – ideally 100-gauge, clear polythene, 250 x 400mm – should be placed over the head and lightly knotted at the top (the muzzle area of the head).Then:
(ii) The optimum air pressure of 6 and 8 Bar is used – lower or higher pressures can result in increased spray. (iii) There should be adequate space between the head and any other meat intended for human consumption so as to minimise cross-contamination dependent on direct contact, splash or possibly aerosol spray which may escape beyond the plastic bag. This can be done in a number of ways such as:
(iv) Minimising cross-contamination from personnel by:
Given that each abattoir will be different, it will be for the FBO to agree with the OV and the FVC the most effective combination of methods required to minimise cross-contamination. In all cases it should be ensured that personnel undertaking sampling using the low-pressure air extraction method are adequately trained in both the method itself and the precautions required when doing so. |
2.8 Traceability of sample to carcase
2.8.1 Maintenance of traceability
The FBO is responsible for and must maintain robust traceability from animal to sample to carcase and all retained parts throughout the entire process.
Sample pots must be properly identified and correlated to the head, the carcase and retained body parts of the animal that has been sampled.
2.8.2 Records
The FBO is responsible for implementing a robust recording system for traceability purposes.
2.8.3 Sample identification
FBOs have two options for identification and submission of samples to the laboratory: either an electronic or a manual system. If using a manual system FBOs are responsible for sourcing their own supplies of barcode labels.
FBOs must ensure that all sample pots are identified with the vertical application of a barcode label. Pot lids can also be identified with the kill number as an additional precaution.
Barcode labels take the following formats:
- 9999DDD000001 for ‘dummy run’ or trial samples
- 9999MMM000001 manually submitted data
- 9999EEE000001 for electronically submitted data
Where 9999 is the establishment approval number and 000001 is the serial number of the sample. Barcode labels must not be reused.
Manual system | Electronic system |
---|---|
Apply a label to the sample pot when the sample is taken. Apply label to the movement card taken from the animal’s passport. Submit movement card with the sample for animal’s ID in barcode form. On the blue / green passports (CCP 01), or where no movement card is available, the FBO must photocopy the front cover of the passport and apply label. |
If using the electronic system, no hard copy passport will be necessary. The details of the barcode must meet the requirements of the testing laboratory and contain sufficient information to allow subsequent tracing of individual carcases and related body parts. It is recommended that the FBO thoroughly tests their bar code system by sending ‘dummy’ labels to the testing laboratory for scanning and reading, before the system is used on actual samples from bovine animals requiring BSE testing. Any failure to read the bar code labels by the testing laboratory will result in a ‘no test’ result and the subsequent disposal of affected carcases and body parts by incineration. |
2.8.4 Test code categories
A table of test codes to be used to submit samples can be found at Annex 3. It is essential the correct codes are used for disease surveillance purposes. The number of animals tested as emergency slaughter, sick at ante-mortem, and healthy are reported as part of the UK’s BSE surveillance programme.
2.8.5 Contaminated / leaking pots
Contaminated / leaking pots will delay the testing process in the lab and could result in delayed results.
Sampling staff must take care to avoid splashes of blood on the outside of the sampling pots and to ensure that the sample pot lid is firmly screwed and securely tightened and checked prior to being packed.
Note: Tamper-evident pot lids are available from an approved laboratory.
2.8.6 FBO responsibility
FBOs must ensure that sample pots are correctly identified and that correlation of the animal and the carcase and parts is maintained at all times.
2.8.7 FSA action- loss of correlation
If FSA checks show correlation has been lost, the OV must
- notify the FBO
- stop processing
- check all animals to the point that correlation has been lost
- instruct the FBO to dispose of all non-correlated carcases / offal as Category 1 SRM by incineration
Note: If the OV is satisfied that all animals that require BSE testing have been sampled, even if individual correlation is lost, carcases may be passed fit for human consumption if all of the submitted sample tests return a negative test result.
This does not affect any enforcement actions to be taken as a non-compliance with the TSE regulations.
2.9 Samples packaging and delivery
2.9.1 Same day delivery
The FBO is responsible for ensuring that samples are despatched as soon as possible on the same day of the sampling
2.9.2 Storage
If samples cannot be despatched the same day of sampling, they can be chilled in a fridge (samples can be stored for up to 4 days at 4oC).
The FBO must ensure that any storage arrangements for brain stem sample pots do not allow cross contamination with food / meat intended for human consumption.
2.9.3 Packaging and delivery
The FBO is responsible for the labelling and packaging of samples, and arranging their delivery to the approved testing laboratory specified in the SOP. A list of approved laboratories can be accessed online.
FBOs must arrange for the samples to be delivered to an approved testing laboratory under the TSE Regulations (England) 2018 Schedule 2, paragraph 9 or the TSE Regulations (Wales) 2018 Schedule 2, paragraph 5. The laboratory can be approved by the UK or another member state of the EU.
The FBO is responsible for ensuring that there are sufficient slaughterhouse staff trained and competent in the labelling, packaging and despatch of brain stem samples.
2.9.4 Packaging and labelling requirements
The FBO must ensure that brain stem samples are packed and labelled in accordance with the packaging instructions P650 of the European Agreement Concerning the International Carriage of Dangerous Goods by Road (version applicable as from 1 January 2005).
2.9.5 FBO verification of number of samples despatched
The FBO must:
- reconcile the number of samples with the number of bovines slaughtered that require BSE testing before the samples are despatched
- notify the number of samples being delivered to the testing laboratory in advance of their despatch by fax or by e-mail
2.9.6 FSA controls
FSA Staff must:
Check | Frequency | Records |
---|---|---|
|
Every day sampling takes place. |
TSE 6/11 |
Note: For sample copy of TSE 6-11 see chapter 9 on ‘Forms’.
2.10 Traceability of all parts: tested animal to carcase
2.10.1 FBO traceability system
The FBO must arrange for a reliable and robust traceability system which satisfies the OV that the carcase and all retained parts can be traced to the brain stem sample, with
- identification of both carcase and brain stem sample
- individual or batch identification of offal, hides, blood, trimmings, feet, udders, fat and by-products
If a batching system is adopted, all material in the batch must be disposed of as SRM by incineration if a positive, insufficient or ‘no test’ result is obtained.
2.10.2 FSA responsibility
FSA staff must confirm that the system for traceability is robust and adequate to ensure that all parts of any positive carcase and the one before and two afterwards on the slaughter line (1b2a) and all parts of any ‘no test’ carcase can be identified and disposed of appropriately. Where the obex is not present and there is ‘insufficient’ material to run three check-tests, the carcase will be treated as a positive and the 1b2a will also need to be destroyed.
2.10.3 FBO by- product records
The FBO must keep records of all SRM material requiring incineration despatched from the premises prior to receipt of negative test results.
2.10.4 FSA supervision of FBO records
The OV must verify the FBO records of disposal to confirm that the destination for disposal is approved for incineration of SRM.
2.10.5 Health marking of carcases and offal awaiting BSE test results
Carcases of animals that require BSE testing must only be health marked after satisfactory Post-Mortem inspection. All health marked carcases must be kept under FSA secure controls until a negative test result has been verified.
Offal may also be health marked or identification marked prior to the receipt of a BSE test result, however the offal must be kept under FSA secure controls until a negative test result has been verified.
2.11 Retention of carcases
2.11.1 FBO retention facilities
The FBO must have sufficient and suitable facilities for holding all the carcase(s) (and the one before and two after as appropriate) and all body parts of animals requiring BSE testing until results are received.
Hides, however, may be sent to an approved hide premises under official control.
All carcases and body parts must be stored as per the SOP.
2.11.2 FBO retention of carcases
Carcases retained pending a test result must be held by the FBO in accordance with one of the following options:
Food business operator retention of carcases
Retention area | Action |
---|---|
In a detained chiller: | Carcases awaiting test results must not come into contact with detained carcases awaiting further examination by an inspector or OV. |
In a chiller other than a detained chiller: | Carcases awaiting test results (including the one before and two after, if appropriate) must be batched and stored together and must not come in to contact with any other carcases. |
2.11.3 Storage in non-sequential kill order in chillers
Carcases awaiting BSE test results must be stored in chillers in kill order unless the criteria below are applied:
- a draft protocol is drawn up by the FBO outlining the procedures to be followed and is agreed with the OV and the FVC for the premises
- the OV and FVC for premises that rely primarily on IT systems for traceability of animals / carcases within the premises should be satisfied that such IT systems demonstrate traceability and also, that there are manual back-up procedures in place in the event of IT systems failing
- the OV and FVC for premises which do not rely primarily on IT systems for traceability of animals / carcases within the premises should be satisfied that their manual traceability systems are such that they provide the necessary assurances with regard to traceability
- in the event that the traceability systems fail to identify the relevant carcases (the positive, insufficient or the ‘no test’ carcase and the 1B2A from the kill line) the OV must consult the FVC as there may be a need to destroy the whole batch
2.11.4 FBO retention of detained carcases
Carcases detained for other reasons, must also be retained pending a test result. They should be held securely and not come in to contact with other detained carcases.
Under these circumstances, it may be inevitable that carcases are not held in the order of kill.
2.11.5 FSA security of the retention facilities
FSA staff must ensure that at the end of each day the holding area is secure and that all parts of tested animal(s) (and one before and two after, if appropriate) are retained under official controls until the results are provided by the FBO to FSA staff.
Chillers must be secured by FSA either sealing the chillers or the rails that contain carcases pending test results.
Seals may not be broken except by FSA staff.
All procedures relating to chiller controls must be recorded by FSA staff on form TSE 6/10:
Reference: See chapter 9 ‘Forms’ for a sample copy of TSE 6/10.
2.11.6 Test carcases or its parts not fit for human consumption
Test carcases or parts of test carcases (pending a test result) found unfit for human consumption must not be stored with other carcases or part carcases that have been passed fit for human consumption.
These carcases or part carcases may be dealt with differently depending on the following situations:
Test carcases or its parts not fit for human consumption
If... | Action |
---|---|
the FBO does not wait for the test result | Dispose of as SRM by incineration |
a negative test result is received | Retain hygienically and once the negative test result is received dispose of as required depending on the by-product category of the material |
a positive, insufficient or ‘no test’ result is received | Retain hygienically and once the positive, insufficient or ‘no test’ result is received dispose of the positive and the 1B2A carcases by incineration as appropriate |
2.12 Retention of all body parts
2.12.1 Identification and retention of body parts
After slaughter, all parts of the animal under test which have been retained must be traceable to the carcase held during retention, and must be treated as below.
Identification and retention of body parts
Part of the carcase | Action |
---|---|
Offal intended for human consumption | Must be retained under official control:
|
Blood | All blood must be retained separately or batched pending a test result, unless disposed of as SRM by incineration before test results are received. FSA controls must be as follows:
|
Green offal | Parts of green offal not classified as SRM (such as stomachs) must be:
|
Offal not intended for human consumption | Offal not intended for human consumption must be retained before the test results are received or disposed of as SRM by incineration before a test result is obtained |
Hides | Reference: See topic 2.13 on ‘Retention of hides’ in this section for additional information |
2.12.2 SRM
SRM removed from carcases must be stained and disposed of by incineration if not held until a negative result is available.
2.12.3 Rumen and gut contents
Rumen contents and gut contents must be disposed of in accordance with existing procedures.
2.13 Retention of hides
2.13.1 Retention at the premises
Hides must be held in the hide room either batched or individually identified.
If batched without individual identification, they must be clearly labelled ‘pending test result’, including the number of hides in the batch and the date of slaughter.
2.13.2 Despatch of hides to a hide premises
Hides may be despatched to a hide market or tannery before a test result is received.
If any of the carcases subsequently test positive or there is no negative test result, the hide must be identified by APHA staff at the hide market or tannery and destroyed by incineration. If batched, the entire batch will need to be destroyed by incineration.
FBOs must agree a hide protocol with APHA to allow hides to be despatched prior to receipt of test results. The OV must be aware of the hide protocol.
2.13.3 Official controls
Hides must be detained under official control until the test results are received.
Official controls
Hide | FSA control |
---|---|
retained at slaughterhouse pending test result | FSA AOs are to do:
|
removed to an approved hide market before test result obtained | Note: At hide premises APHA checks disposal if a positive result is received. |
2.13.4 Hides from positive, insufficient or ‘no test’ result
If hides are individually identified then any positives must be disposed of as SRM by incineration.
If they are batched, the entire batch must be incinerated in the event of a positive or ‘insufficient’ test result.
2.14 Test results
2.14.1 FBO responsibility
The FBO is responsible for:
- having facilities in place to receive tests results, and
- giving FSA staff in plant copies of the test results
Copies of the test results must be kept by the FBO for 24 months.
2.14.2 FSA responsibility
FSA staff are to read the test results and take all necessary actions. Form TSE 6-7 must be completed and, together with copies of the test results, kept on file in the FSA office for 12 months.
Poor quality samples reported by the lab will need to be investigated. The SLA and contracts team will notify the local team from the plant affected to request an investigation. Results of the investigation and where necessary further preventative action need to forwarded to sla.contracts@food.gov.uk , FVC and FVL.
2.14.3 FSA access to test results
Upon completion of a successful approval trial, the approved laboratory will work with SLA and Contract team to provide access to the results for FSA staff.
2.15 Positive test result
2.15.1 Notification of positive test result
When a positive BSE test is identified, the approved laboratory will inform:
- the FBO
- the FSA staff at plant
- APHA
APHA will be responsible for DNA testing of samples collected by FSA.
2.15.2 DNA Sampling kits
APHA will deliver the sampling kits to the plant.
The sampling kit will include:
- an outer box
- sample pots
- labels
- tamper-evident bag
- freezer pack
2.15.3 FSA responsibility for DNA sampling
FSA staff are to take samples for DNA testing from the positive carcase and the one before and one after.
Samples, approximately the size of a 50p coin, are to be taken from the diaphragm of each carcase ensuring there is no cross contamination between carcases. These must be sealed into separate sample pots and placed into the pot tray and sealed into the tamperproof bag and then frozen for 24 hours under FSA control.
Once the samples are frozen, FSA staff should contact APHA by email at: lab.services@apha.gsi.gov.uk to inform them of the plant number and the samples to expect for the Cattle Microsatellite Identification test (DNA test).
FSA staff should then contact PDP couriers on 01784 420466 using the ‘VETLAB’ account, to organise collection of the samples, which are to be sent to:
Central Sequencing Unit
APHA Weybridge
Woodham Lane
New Haw
Addlestone
KT15 3NB
Once the collection time has been arranged place the samples in the box with the freezer packs for collection.
2.15.4 Carcase and body parts
If a positive test result is received, the carcase and all parts of the positive animal, or the whole batch if a batching system is in operation, together with all parts of the animal slaughtered before and the two animals slaughtered afterwards (‘1B2A’) must be destroyed by incineration unless there have been effective arrangements put in place for preventing cross contamination between carcases during processing and storage.
Note: The 1B2A rule applies.
Note: The FBO is responsible for identification and disposal by incineration of the relevant carcases and parts.
Note: The OV must confirm the identity of the positive carcase (and the one before and two after (‘1B2A’) during the process), offal (which may have been batched), hide and blood and will verify that this material is consigned to a site approved to incinerate ABP Cat 1 SRM.
Note: AOs must check 100% of carcases and body parts for full traceability and disposal and should verify the slashing and staining of positive carcases.
2.15.5 Hides
If the hides are stored in the slaughterhouse hide room until the test result is received and there is a positive result the individual hide or the entire batch (if not individually identified) must be identified under FSA supervision and destroyed by incineration.
Note: The 1B2A rule applies.
Note: For the action to be taken for hides delivered to a hide premises refer to the ‘Hide protocol’.
2.15.6 SRM records
The FBO is responsible for maintaining accurate records of the weight disposed of as SRM by incineration.
2.16 ‘No test’ result
2.16.1 Carcase and body parts
If a ‘no test’ report is received, for example, due to the target area of the obex being unavailable, the carcase and all parts of the ‘no test’ animal must be destroyed by incineration.
Note: The 1B2A rule does not apply. However, the whole batch must be destroyed if a batching system is in operation.
Note: If the target area of the obex is not available, the testing laboratory will carry out three further tests. Only when these further tests return negative, will the sample be reported as a ‘no test’. If the laboratory cannot assign negative results to the three additional tests or there is insufficient material to test, then the 1B2A rule applies
The FBO is responsible for identification and disposal by incineration of the relevant carcases and parts.
2.16.2 Hides
If the hides are stored in the slaughterhouse hide room until the test result is received and there is a ‘no test’, the individual hide or the entire batch (if not individually identified) must be identified and despatched for destruction by incineration.
Note: The 1B2A rule does not apply to individually identified hides.
2.16.3 FSA responsibility
The OV must confirm the identity of the ‘no test’ carcase, offal (which may have been batched), hide and blood and will verify that this material is delivered to be destructed by incineration.
Note: AOs must check 100% of carcases and body parts for full traceability and disposal.
2.16.4 SRM records
The FBO is responsible for maintaining accurate records of the weight disposed of as SRM by incineration.
2.17 ‘Insufficient’ test result
2.17.1 Carcase and body parts
If an ‘insufficient’ test result is received indicating that the approved testing laboratory has not been able to carry out the three further tests on the submitted sample because of a shortage (or complete absence) of suitable brain stem material, the FBO must immediately dispose of as SRM:
- the carcase and all parts of the body (including the blood) of that animal
- the carcase and all parts of the body (including the blood) of the animal immediately preceding that animal on the slaughter line and the two animals immediately following it
- the whole batch if a batching system is in operation
2.17.2 Hides
If the hides are stored in the slaughterhouse hide room until the test result is received and there is an ‘insufficient test’ result, the individual hide or the entire batch (if not individually identified) must be identified and despatched for destruction by incineration.
Note: The 1B2A rule does not apply to individually identified hides.
2.17.3 FSA responsibility
The OV must confirm the identity of the ‘insufficient test’ carcase, offal (which may have been batched), hide and blood and verify that this material is delivered to be destroyed by incineration.
Note: AO’s must check 100% of carcases and body parts for full traceability and disposal.
2.17.4 SRM records
The FBO is responsible for maintaining accurate records of the weight disposed of as SRM by incineration.
2.18 ‘Inconclusive’ test result
2.18.1 Carcase and body parts
An ‘inconclusive test’ should be treated as a ‘positive’.
Note: The EU TSE Regulations set out what action should be taken in the event of an ‘inconclusive test’ result. However, this category is not recognised in the TSE statutory instrument (SI) because in practice, the BSE tests used by approved laboratories provide either positive or negative results.
2.19 ‘Outstanding’ test result
2.19.1 Carcase and body parts
If an ‘outstanding’ test result is received, indicating that some of the paperwork is missing or incomplete, the approved testing laboratory has not been able to correlate the sample to the animal details and further information is required from the FBO. In this case, the FBO must immediately submit any information required.
Meanwhile:
- the carcase and all parts of the body (including the blood) of the ‘outstanding’ test result animal, must remain under official control until the laboratory receives the information from the FBO and is able to release the test result
- the carcase and all parts of the body (including the blood) of the animal slaughtered immediately before the ‘outstanding’ test result animal and the two animals immediately following it (1B2A), must remain under official control until the laboratory receives the information from the FBO and is able to release the test result
- if a batching system is in operation, the whole batch must remain under official control until the laboratory receives the information from the FBO and is able to release the test result
2.19.2 Hides
If the hides are stored in the slaughterhouse hide room until the test result is received and there is an ‘outstanding’ test result, the individual hide or the entire batch (if not individually identified) must be identified and kept under official control or despatched for destruction by incineration.
Note: The 1B2A rule applies.
2.19.3 FSA responsibility
The OV must confirm the identity of the ‘outstanding’ test carcase (and the one before and two after (1B2A) during the process), offal (which may have been batched), hide and blood and will verify that these remain under official control until the test result is obtained from the laboratory.
Note: AO’s must check 100% of carcases and body parts for full traceability and disposal.
2.20 Negative test result
2.20.1 Carcase release
When a negative result is received, the carcase and offal may be released as fit for human consumption unless they need to be destroyed under the 1B2A requirements.
2.20.2 Vertebral column removal
The vertebral column of OTM cattle slaughtered for human consumption must be removed in an approved cutting plant additionally authorised for vertebral column removal, then disposed of as SRM.
Reference: See instructions on the removal of the vertebral column in authorised cutting plants in chapter 2.7 on ‘Specified risk material’.
Note: A list of these cutting plants is available on the FSA website.
2.21 Enforcement
2.21.1 Enforcement responsibility
The FSA is responsible for enforcement within authorised premises, acting on behalf of Defra, Scottish Government and Welsh Government.
The local authority (LA) is responsible for enforcement outside authorised premises, including the consignment of cattle born or reared in the UK before 1st August 1996 to slaughterhouses.
Reference: See chapter 2.5 on ‘Animal Identification’ for additional information on eligibility of cattle for slaughter.
3. Sheep TSE Sampling and Submission
In this section
3.11 Packaging and storage of samples: Bioshield box and Bioshield bottle
3.14 Collection and disposal of sharps and clinical waste
3.1 Survey requirements
3.1.1 Regulations
(EC) 999/2001 requires Member States to have a survey in place to monitor the presence of Transmissible Spongiform Encephalopathies (TSEs) in sheep.
The above regulation is enacted in GB by The Transmissible Spongiform Encephalopathies (England) Regulations 2018 and the Transmissible Spongiform Encephalopathies (Wales) Regulations 2018, as amended.
3.1.2 Relevant establishments
These instructions are relevant to FSA staff at slaughterhouses participating in the Sheep TSE Survey.
3.1.3 Authorisation
Under the TSE Regulations, FBOs and their employees are required to comply with such reasonable requirements as the inspector considers necessary. An inspector in this case is any FSA officer who has been issued with an authorisation, after the satisfactory completion of the necessary training, in accordance with the TSE Regulations.
3.2 Sampling plan
3.2.1 Sheep sampling plan
APHA, in consultation with Defra and the FSA, determine the required percentage to be sampled. The SLA and Contracts team will notify this percentage to FSA staff in participating plants.
The sampling plan enables the epidemiological requirement of the survey to be met and completed by the end of each calendar year.
APHA assesses the sampling survey throughout the year, which means that sampling percentages may be adjusted during the year to achieve the required target.
Brain stem samples must be collected in order to test selected animals in compliance with the sheep survey.
Samples are sent to the TSE Testing Laboratory for testing.
To meet the increased EU requirement (Regulation (EC) 36/2005) for TSE testing and increase the analytical sensitivity of the testing program, it is required that the cerebellum is included in the sample along with the brain stem. This allows classical scrapie to be differentiated from atypical scrapie should the sample test positive.
3.2.2 Suspect scrapie cases
Suspect scrapie cases must be reported immediately to the local APHA Regional Operational Director (ROD) / Divisional Veterinary Manager (DVM) and the animal(s) must not be allowed to enter the slaughterhall.
Reference: See chapter 6 on ‘Notifiable diseases’ for the procedures that must be followed.
3.2.3 Dead on arrival and dead in lairage
(EC) 999/2001 requires a number of sheep over 18 months of age that have died other than by being slaughtered for human consumption to be tested for TSE.
Brain stem and cerebellum samples are collected for testing instead of whole heads being sent to the TSE Testing Laboratory.
3.2.4 Compulsory scrapie flock scheme
On confirmation of TSE in sheep flocks, current EC Regulations ((EC) 999/2001, (as amended), Annex III, Chapter A) require further testing of these flocks over a three year ‘restriction period’ under the Compulsory Scrapie Flock Scheme (CSFS).
A random selection of sheep aged over 18 months slaughtered for human consumption is to be tested. Such animals must not be included in the percentage of sheep required to be tested under the normal sampling plan.
CSFS animals can only go to slaughterhouses currently participating in the survey or that have previously participated and trained staff are available, and where the FBO is happy to take them.
Reference: See sub-topic 3.4.10 on ‘Selection CSFS’ for further information.
3.2.5 Goat sampling plan
At present, FSA staff are not required to sample adult goats.
3.3 When to sample
3.3.1 When to collect samples: sheep/goat surveys
Samples must only be collected Monday to Thursday, and ideally spread out over the four days. Samples must be taken on any of these days when eligible animals are selected.
Note: Sampling of goats, including those dead on arrival (DoA) or dead in lairage (DiL), is currently not required.
Samples must not be collected on Fridays or when the following day is a public holiday.
3.3.2 When to collect samples: CSFS
CSFS animals may be presented on any day of operation but the Specialist Service Centre (SSC), Worcester (formerly the National Scrapie Plan Administration Centre – NSPAC) will endeavour to ensure they are slaughtered Monday to Thursday.
Should any CSFS animals be slaughtered on a Friday, weekend or Public Holiday, samples must be taken and stored in a refrigerator until they can be despatched.
3.3.3 When to collect samples: All
Caution: Failure to comply with these instructions will result in a delay in testing and return of the results to the slaughterhouse, as the laboratory will not be able to cope with incorrect or excessive supply.
Note: During religious festivals, sheep that have been selected by a family may be excluded from the sampling process; however, any shortfall must be made up during the same week.
3.4 Selecting eligible animals to sample
3.4.1 Selection: sheep survey
Sheep are selected by either the OV or MHI (the ultimate responsibility rests with the OV).
Only sheep with a flockmark or individual ear tag are to be selected.
Selection within the pen should be at random, avoiding over-representation with regard to:
- origin
- age (confirmed by a post-slaughter dentition check)
- production system
- any other characteristic
Reference: See chapter 2.5 on ‘Animal identification’ for additional information.
Note: Animals should not be selected and then held overnight for slaughter the following day. However, in exceptional circumstances such as when animals are unacceptably dirty, animals may be held overnight. In this case, the lab must be informed, so they can expect the samples the following day.
Note: Sheep born and raised in Great Britain (GB) are preferred for sampling. If there are no GB sheep available, sheep born and raised overseas may be selected.
Establishments participating in the survey must sample a given percentage of their weekly throughput of ewes and rams aged over 18 months (eligible animals).
Whenever eligible sheep are killed, the minimum number of samples to collect is one, never zero.
Calculate the number of samples required by:
a. divide the number of eligible sheep by 100 (for example, 256 / 100 = 2.56)
b. multiply the result by the given percentage (for example, 2.56 x 1.0 = 2.56 or 2.56 x 0.5 = 1.28)
c. round the result to the nearest whole number (for example, 2.56 = 3 or 1.28 = 1)
The daily percentage number should only be used as a guide.
The total number of samples collected during the week should reflect the given percentage of the weekly throughput of eligible sheep. Any shortfall should be made up the following week.
3.4.2 Worked example: sheep survey
Sheep survey sampling days
Day | Mon (Sampling day) | Tue (Sampling day) | Wed (Sampling day) | Thu (Sampling day) | Fri | Sat | Sun | Total |
---|---|---|---|---|---|---|---|---|
Eligible throughput | 256 | 301 | 124 | 0 | 13 | 104 | 0 | 798 |
Samples required (1%) | 3 | 3 | 1 | 0 | 1 | 1 | 0 | 9 |
Samples collected | 4 | 0 | 3 | 0 | 0 | 0 | 0 | 7 |
+/- | +1 | -3 | +2 | 0 | -1 | -1 | 0 | -2 |
Eligible throughput | 256 | 301 | 124 | 0 | 13 | 104 | 0 | 798 |
Samples required (0.5%) | 1 | 2 | 1 | 0 | 1 | 1 | 0 | 6 |
Samples collected | 4 | 0 | 3 | 0 | 0 | 0 | 0 | 7 |
+/- | +3 | -2 | +2 | 0 | -1 | -1 | 0 | +1 |
3.4.3 Identifying selected sheep
Options | Method |
---|---|
1 |
The fleece of all eligible animals must be marked in the lairage using the green colour identifier spray. Mark each animal with a number starting at one (1) each day. This will allow sheep to be presented for slaughter in number order and facilitate correlation. Sprays are ordered by FSA staff from the TSE Testing Laboratory using the TSE Testing Laboratory consumable order form (Annex 5). |
2 |
The lairage staff should handle and tag each selected animal with the red ear tag under FSA supervision, post-slaughter but before head removal. This is an FBO requirement and the FSA officer can direct the FBO to do so. If local conditions do not permit this then the lairage staff should restrain the sheep for the OV to insert the tag, although this should be avoided. |
3.4.4 Form completion
At the point of selection you should begin completion of the Daily Record Sheet (TSE 6/6) and the Rapid Testing form (TSE 6/2).
For more information, see topics 4.1 and 4.2 in this chapter.
3.4.5 Selection: goat survey
If the sampling of goats is required, 100% of adult goats presented for slaughter must be sampled.
3.4.6 Dentition check: sheep / goat surveys
A dentition check must be made by FSA staff post slaughter. Only sheep and goats that have more than two permanent incisors erupted may be sampled. Enter the number of incisors for the animal’s TSE 6/2 at this point.
Otherwise, do not take the sample and discard the TSE 6/2 that was completed in the lairage. The carcase can be processed as normal and does not need to be retained.
Older animals that have lost some or all of their permanent teeth (‘broken mouthed’) are still eligible for testing.
3.4.7 Selection: dead on arrival (DoA) and dead in lairage (DiL)
In participating establishments, adult sheep found DoA or DiL must be tested for TSE as part of the fallen stock survey.
The animal(s) may have to be moved by the FBO to a suitable place, for example, the isolation pen in the lairage.
Adult sheep or goats are those with more than two permanent incisors erupted through the gum.
Brain stem samples are collected from DoA and DiL animals and are to be identified with ‘DoA / DiL’ on the pot lids.
Note: If the slaughterhouse is not part of the survey the animal should be disposed of as Category 1 (Cat 1) Animal By-product (ABP) (Specified Risk Material (SRM)), by incineration.
3.4.8 Health and safety
FSA staff must wear suitable protective clothing including disposable gloves.
Reference: See FSA ‘Health and safety manual’.
3.4.9 Tagging
If any sheep do not have an ear tag they must still be sampled. Place a red tag in the ear, and record this number in the ‘other ear tags’ field on the TSE 6/3 form.
3.4.10 Body disposal
After removal of the head for sampling, the body (and any contaminated material) must be disposed of as Cat 1 ABP (SRM) by incineration. An additional allowance of 30-40kg must be allowed per animal in terms of the overall calculation of daily SRM weights.
3.4.11 Selection: CSFS
SLA and Contracts Team will be notified in advance by the SSC (Worcester) of the number of CSFS animals to be slaughtered and sampled to ensure that enough sampling equipment and resources are available.
SLA and Contracts Team will contact the OV and / or Inspection Team Leader (ITL) upon receipt of the details.
Animals will be accompanied by forms NSP 61 and NSP 61A, which will already have been partially completed.
The NSP 61A will show the details of every animal selected to be culled. Some will be identified with an orange ear tag and these are the animals to be sampled (‘‘selected animals’’). This tag can be used to uniquely identify the animal during processing.
Animals not identified with an orange ear tag must not be sampled.
CSFS animals selected for testing (with an orange ear tag) that are found DoA or DiL must be sampled. The relevant sections in form NSP 61 and NSP 61A must be completed. There is no need to complete a TSE 6/3 form.
Sheep that are DoA or DiL which are not selected (do not have an orange tag) must also be tested. See sub-topics 3.4.6 to 3.4.9 in this chapter.
Such animals must not be included in the percentage of sheep required to be tested under the normal sampling plan.
3.5 Slaughter arrangements
3.5.1 Slaughter protocol
The OV should ask the FBO to produce and agree a written protocol for slaughter, sample collection, identification and retention of split carcases, offal and waste and cleaning of equipment and premises. The FBO, OV and FVC must sign these and retain copies.
To ensure traceability, the OV should liaise with the FBO to agree a reliable method for identifying and correlating the retained carcases and body parts (including organs, tissues, blood and fleece / skin), as part of the protocol.
3.5.2 Hygiene
Slaughter procedures for sample animals must not jeopardise hygiene at the premises. Captive bolts can be used in the slaughter process.
3.5.3 Batch slaughter
The most efficient way to collect samples is to slaughter the selected animals in one batch. This may also minimise the time between slaughter and despatch of samples.
3.5.4 Time of slaughter
FSA staff are to record in the plant daybook the time the first sample animal is slaughtered.
3.5.5 On-line splitting
Splitting of carcases may be undertaken on the slaughter line during dressing where the OV is satisfied that there is full compliance with the legislative requirements relating to cross-contamination between carcases.
3.6 Correlation
3.6.1 Requirement for correlation
The carcase and all body parts of the sampled animal must be identifiable and retained under the control of the FSA until a test result has been obtained, unless they are immediately disposed of as Cat 1 ABP (SRM) by incineration.
It is the OV’s responsibility to decide what system should be used to ensure that correlation between carcase, blood, body parts, offal, fleece and sample is maintained at all times.
3.6.2 Correlation essentials
It is essential that:
- each half of the carcase and any retained body parts are correlated with the number on the red ear tag (routine sampling) or orange ear tag (CSFS)
- all body parts of the carcase are identifiable to the sample animal during retention
- each half carcase is identified using matching numbered detention tags
3.6.3 Carcase correlation
After the fleece has been removed, attach to the carcase a detention tag numbered (colour of the day) with the spray number on the fleece. This correlates the carcase with the red or orange ear tag number.
3.6.4 Animal by-products
Use matching numbered detention tags to identify retained red and green offal. The low value of these may mean that the FBO opts to dispose of all the offal as Cat 1 ABP (SRM) by incineration or, alternatively, to batch retained offal without individual correlation pending the result.
3.7 Blood collection
3.7.1 Collection options
Blood must be collected either:
- in containers used for individual animals, the dimensions of which must be such that the splashing of blood into the surrounding area is avoided
- in a blood tank or container separate to that used for collection of blood from non-test animals
- in a blood tank or container used for collection of blood from test and non-test animals
Note: Blood collected from test animals can only be mixed with blood from non-test animals if in the case of a positive test result all blood is disposed of as Cat 1 ABP (SRM) by incineration.
3.7.2 SRM allowance
If blood is disposed of as Cat 1 ABP (SRM) by incineration, an additional weight of 2.5kg must be allowed per animal in terms of overall calculation of daily SRM weights.
3.8 Sampling arrangements
3.8.1 Suitability
In considering suitability of sampling arrangements at individual establishments, the OV must take the following points into consideration:
- there must be adequate, effective separation between the sampling location and fresh meat so as to ensure that cross-contamination of fresh meat intended for human consumption does not occur
- no aspect of hygiene must be breached
- no aspect of the SRM rules must be breached
- functional wash hand basin, soap and hand drying facilities must be within easy access of the sampling table
- only the stainless steel sampling table provided by APHA must be used for sampling; the table is the property of APHA and not the FBO
3.8.2 Sampling within the slaughterhall
If the sampling location is within the slaughterhall it should not be situated beyond the point at which the fleece is removed from the carcase.
3.8.3 Sampling equipment supplies
The TSE Testing Laboratory will supply all sampling equipment directly to FSA staff at the slaughterhouse. If supplies are running short re-order direct from the stores using the TSE Testing Laboratory consumables order form. It takes on average five working days from the placement of an order to the receipt of equipment at the slaughterhouse. Place the order before supplies run out. It is recommended that plants hold sufficient supplies for at least two weeks if possible.
See Annex 5 for a sample copy of the order form.
3.9 Sampling preparation
3.9.1 Head removal
The OV must check that the FBO removes the head ensuring that the brain stem and cerebellum remain intact within the skull. Cross-contamination between heads must be prevented.
3.9.2 Who performs sampling
Removal of the brain stem and cerebellum must only be undertaken by FSA staff trained in this process by a fully trained OV/ITL or by the TSE Testing Laboratory.
Note: Only the TSE Testing Laboratory may train staff in plants which are new to the scheme.
3.9.3 Equipment
One set of disposable equipment must be used to collect both brain stem and cerebellum from one head. Sufficient equipment to undertake testing of the day’s quota is to be laid out in preparation for undertaking brain stem and cerebellum removal, and is as follows:
- sampling table
- head tray
- instrument tray
- tag cutting scissors
- heavy duty undergloves and disposable latex gloves
- bioshield box and inner frames for pots or biobottle with packing box
- benchkote dispenser and sheets
- forceps
- scissors
- sampling spoons
- sample pots
- snap lock plastic bags
- forms bag
- sharps box and clinical waste unit
- SRM label
- disposable apron
- plastic refuse bag and paper towels
3.9.4 Cross-contamination
The brain stem and cerebellum must be collected in a manner that prevents any risk of contamination between the samples. Use new instruments and latex gloves for each head sampled, keep all parts of the sampling workstation clean and neat, and keep the pots, containers and packaging clean and dry.
3.9.5 Packaging
To prevent contamination of the bioshield box by water or blood during sampling, the bioshield box and inserts should be stored separately in a dry area. Completed sample pots can first be placed on a tray on the table and then packaged in the bioshield box on completion of the sampling.
Prior to filling with completed sample pots the bioshield box or bottle should be made ready by placing a sheet of frozen Techni-Ice at the base of the box or an ice-brix in the bottom of the bottle.
3.9.6 Procedure
For each head to be sampled the FSA officer must follow the steps in the table below:
Step | Action |
---|---|
1 |
Ensure that the safety helmet, visor (or goggles / face mask supplied as an alternative) and undergloves are worn to comply with health and safety risk assessments Note: The undergloves may be household rubber gloves or latex gloves |
2 | Put on a pair of latex gloves over the undergloves |
3 | Place a new piece of benchkote on the instrument board |
4 | Place new forceps, scissors and sampling spoon on the benchkote |
5 | Open a pot and place pot and lid on benchkote |
6 | Open one small plastic bag, open out and insert into the open pot |
3.9.7 Transfer of heads
Heads should be transferred either individually or collectively to the sampling site in the slaughterhouse. Brain stem and cerebellum samples are easier to remove without causing damage if they are left to cool for at least five minutes.
3.9.8 Head position
Place head upside down in the head tray with foramen magnum facing the sampling officer.
See diagrams 1 and 2 below for anatomy and outline of the dissection method.
3.9.9 Brain stem removal
Diagram 1: Anatomy and sampling steps
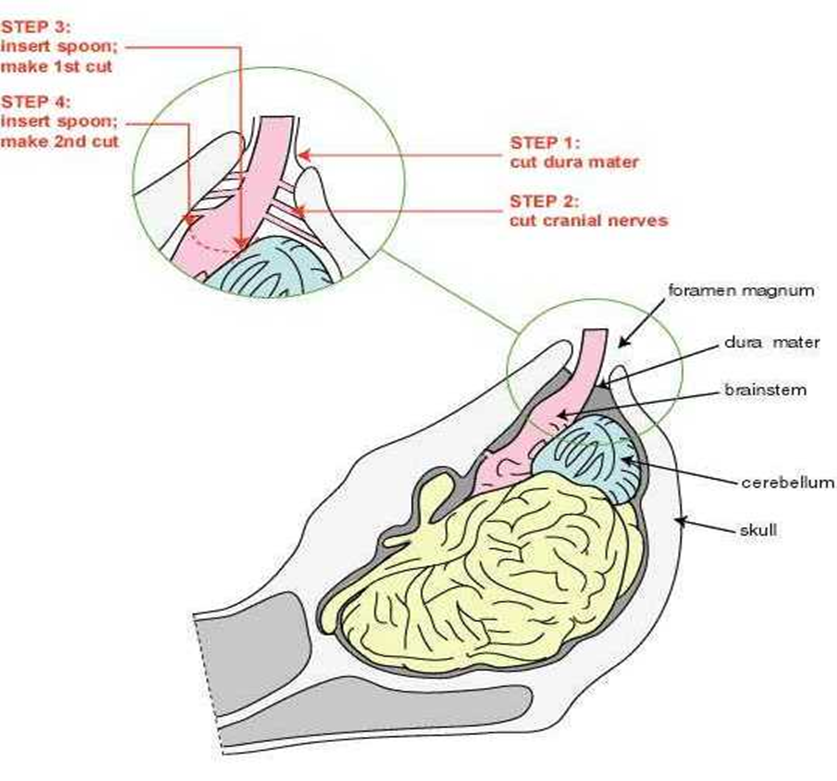
Diagram 2: the area of tissue (obex) to be targeted
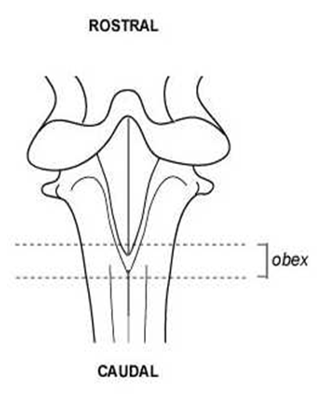
3.9.10 Removal procedure
Follow the steps in the table below to remove each brain stem sample.
Step | Action |
---|---|
1 | Firstly, remove any blood clots (using scissors and forceps) obscuring the view of the brain stem and identify the dura mater. Using a fresh pair of scissors cut free the dura mater from the brain stem and its attachment to the skull. Gently hold the brain stem as close to the end as possible with the forceps. If possible hold any remaining dura mater on the surface of the brain stem as this will provide a better grip of the brain stem. |
2 | Identify the position of the cranial nerves within the skull. Holding the brain stem with the forceps, move the brain stem to the side and insert the scissors into the foramen magnum and cut through the cranial nerves (VII –XI) that originate from the brain stem at three and nine o'clock positions. Take care not to cut the brain stem. Do this on both sides of the brain stem. |
3 | Using the forceps, very gently pull the brain stem until it is straight and insert the spoon underneath it with the cutting edge of the blade facing down. Keep the blade and the spoon against the bone as it is inserted. Insert to the level of the notch of the spoon – approximately 8-10cm. When in position, point the cutting edge of the blade downward by lifting the handle upwards. Cut through the cerebellar peduncles by moving the handle from side to side. |
4 | After completing the cutting, carefully withdraw the spoon and insert it with the blade pointing downwards on top of the brain stem until it enters to a depth of 8-10cm. Gently move the blade side to side and downwards, and cut through the rostral medulla. Avoid rotating or excessive side to side movements of the spoon, as this will damage the obex. |
5 | Gently pull with the forceps, and using the spoon as a scoop or lever, remove as much brain stem as possible from the skull. If resistance is encountered, check that the cranial nerves and dura mater have been freed from the brain stem. If not, repeat step 1. However, if this area is free, reinsert the spoon and continue to cut through the brain stem with a gentle side to side and downward motion of the handle. |
6 |
Place the brain stem in the snap-lock plastic bag in the pot. Note: This same bag will be used to put both the brain stem and cerebellum from the animal. |
3.10 Cerebellum removal
3.10.1 Cerebellum removal procedure
After removing the brain stem, follow the procedure set out below for removing the cerebellum.
Step | Action |
---|---|
1 | With the ventral aspect of the head uppermost, look downwards through the foramen magnum and identify the cerebellum. Insert the spoon underneath the cerebellum and lever it upwards into the centre of the space vacated by the brain stem. |
2 | If the cerebellum is not moving freely, loosen it by moving the spoon gently around and underneath it. |
3 | Lift the cerebellum towards the foramen magnum using the spoon to support and guide, and gently take hold of the cerebellum with the forceps. Remove the cerebellum through the foramen magnum. |
4 | Place the cerebellum in the same bag with the brainstem sample. Close the bag. |
3.10.2 Equipment / hygiene procedures
After removing the cerebellum the steps in the table below must be followed.
Step | Action |
---|---|
1 | Remove the numbered section of all ear tags using the tag cutting scissors, and place them in the pot on top of the snap-lock plastic bag. Ears must not be placed with the ear tag in the pot. However, to avoid injury from sharp edges when removing metal ear tags, a small piece of ear is allowed to remain on the tag. Seal the pot. |
2 | Put the head and any pooled blood from the head tray in the SRM bin. Wipe down the tray with disposable paper as necessary. |
3 | Place the disposable scissors in the sharps box. |
4 |
Put the forceps, spoon, used benchkote, paper towels and apron in the clinical waste container, then remove the latex gloves and put them in the clinical waste container. See topic 3.14 on ‘Collection and disposal of sharps boxes and clinical waste units’ in this chapter. |
5 | Place the lid on the pot, seal and write sample number on the lid. |
6 | Place in the box or biobottle. |
7 | Repeat the process until sampling is complete and then go to Packaging and Storage of Samples on the following page. |
3.11 Packaging and storage of samples
3.11.1 Bioshield box procedure
The table below lists the steps that must be followed if using a bioshield box to despatch samples. A box can hold up to 40 samples.
Step | Action |
---|---|
1 | Ensure a pre-frozen Techni-Ice sheet is in the bottom of the box. |
2 | Fill lower frame with sample pots before using a second frame. |
3 | Place a second sheet of Techni-Ice on top of the samples. If there are no pots, still place the Techni-Ice sheet in the box. |
4 | Place all the TSE 6/2 / NSP 61/61A / TSE 6/3 forms in the large plastic document bag. On the outside of the bag record:
|
5 | Place plastic bag containing TSE 6/2 / NSP 61/61A / TSE 6/3 forms on top of Techni-Ice. |
6 | Apply the SRM label to the outside of the bioshield box. |
7 | Place the bioshield box in a plastic refuse bag to protect the surface of the box from contamination while carrying it through the slaughterhouse and during storage. |
8 |
Close the plastic refuse bag with a cable tie or other secure means. Ensure that all blood and any other contamination is washed off the temporary plastic refuse bag or use a new one. The plastic refuse bag must be labelled with the pre-printed temporary packaging label to prevent accidental disposal as waste. |
9 | Place samples in a detained chiller prior to despatch. |
3.11.2 Bioshield bottle procedure
The table below lists the steps that must be followed if using a bioshield bottle to despatch samples. A bottle can hold up to seven samples.
Step | Action |
---|---|
1 | Ensure a pre-frozen ice-brix is in the bottom of the biobottle. |
2 | Place a maximum of 7 pots in the biobottle. |
3 | Place the second ice-brix on top of the pots in the biobottle. |
4 | Place the bottle in its cardboard box. |
5 | Place all the TSE 6/2 / NSP 61/61A / TSE 6/3 forms in the large plastic document bag. On the outside of the bag record:
|
6 | Insert plastic bag containing the TSE 6/2 / NSP 61/61A / TSE 6/3 forms round the bottle in the biobottle box. |
7 | Apply the SRM label to the outside of the biobottle box. |
8 | Place the biobottle box in a plastic refuse bag to protect the surface of the box from contamination while carrying it through the slaughterhouse and during storage. |
9 |
Close the plastic refuse bag with a cable tie or other secure means. Ensure that all blood and any other contamination is washed off the temporary plastic refuse bag or use a new one. The plastic refuse bag must be labelled with the pre-printed temporary packaging label to prevent accidental disposal as waste. |
10 | Place samples in a detained chiller prior to despatch. |
3.12 Problems with sampling
3.12.1 Problems that may be encountered
If problems arise during sampling the following action is to be taken.
Problems that may be encountered (Sheep TSE Survey):
Problem | Action |
---|---|
No ear tags present in the ear (it may have fallen out) | The sample procedure for this animal should be abandoned and the carcase processed as normal |
No brain stem present in the head (it has been pulled out during separation of the head) | The sample procedure for this animal should be abandoned and the carcase processed as normal |
No cerebellum collected | Do not send sample; deselect brain stem and carcase |
Problems that may be encountered (Sheep TSE Survey, CSFS):
Problem | Action |
---|---|
Lost Orange Tag OR No brain stem | Do not sample; inform SSC (Worcester), record as ‘Not Sampled’ in NSP 61A and process carcase as normal |
No cerebellum collected | Send brain stem only |
3.13 After sampling
3.13.1 Cleaning
After sampling, the sampling workstation and surrounding area must be cleaned in accordance with local protocols. Cleaning is to be supervised by FSA staff.
3.13.2 Sharps
Close, but do not seal the sharps box at the end of sampling and store it in a dry area until re-use.
See topic 3.14 on ‘Collection and disposal of sharps and clinical waste’.
3.13.3 Glove disposal
The heavy-duty gloves are to be disposed of in the clinical waste container.
See topic 3.14 on ‘collection and disposal of sharps and clinical waste’.
3.14 Collection and disposal of sharps and clinical waste
3.14.1 Service provider
SRCL provides a sharps and clinical waste collection and disposal service on behalf of FSA and Defra for slaughterhouses participating in the Sheep TSE Sampling Survey.
Sharps Box
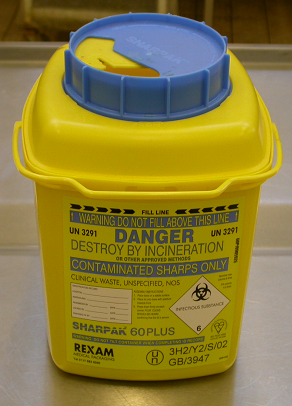
Capacity: 12 litre
Clinical Waste Unit
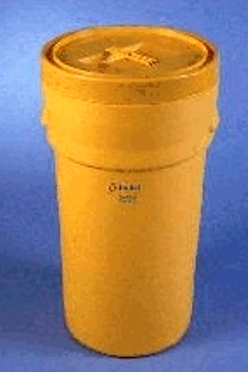
Capacity: 60 litre
The exchange of sharps boxes and clinical waste units will be on an agreed frequency basis, at an agreed collection time and day.
Collection will take place regardless of whether the box is full or not.
Replacement containers will be left by SRCL after each collection.
3.14.2 Setting up or changing sharps / theatre unit arrangements
Contact the SLA and Contracts team, giving your name, the slaughterhouse approval number and the establishment’s opening hours to:
- arrange a new service
- to change the frequency of collections and numbers of sharps boxes or theatre units
SRCL then confirm by email the date of installation or acceptance of service frequency to the SLA and Contracts team and FSA staff.
SRCL will then contact the FSA staff in plant to confirm delivery arrangements. If SRCL are unable to confirm delivery details with FSA staff in plant then they will contact SLA and Contracts team to arrange alternative delivery.
FSA staff in plant must contact the SLA and Contracts team within 5 working days to confirm delivery or amendment to service.
3.14.3 Disposal of sampling equipment
All sheep TSE sampling consumables (except sharps) must be disposed in the clinical waste units. The consumable must first be put into a ‘Bio-Hazard’ polythene bag (DIF 0011).
At the end of each day the bag must be sealed and placed into the clinical waste unit. A new bag must be used each day of sampling.
Note: The unit’s sealable lid must not be ‘clicked shut’ until prepared for collection.
3.14.4 Responsibilities of the ITL
The ITL is responsible for sharps boxes and the clinical waste units, and must ensure the following are complied with:
- boxes and units must be sealed according to instructions on the box before collection
- boxes and units must be left in the agreed collection point where the replacement box will be left
- the outside of the box and unit must be clean and free of blood
- the slaughterhouse licence number must be marked on the box and unit lid in indelible ink
3.15 Storage and retention pending results
3.15.1 Retention options
Carcases and offal retained pending a test result should be held in accordance with one of the following options:
Option 1 | In a detained chiller / area | Carcases awaiting test results must not come into contact with other detained carcases awaiting further examination by an inspector or OV |
---|---|---|
Option 2 | In a chiller other than the detention chiller | Carcases should be retained in a single batch that can be easily identified in a specified part of the chiller and must not come into contact with other meat |
3.15.2 Chiller control
Areas where carcases are retained must be under the control of the OV. They should be sealed, in which case the seals may not be broken except by the OV, ITL or MHI.
3.15.3 Form completion
At this point you should return to the completion of the Daily Record Sheet (TSE 6/6).
All procedures relating to chiller controls should be recorded on the TSE 6/6 including:
- date and time of sealing and person responsible
- seal number
- date and time of unsealing and person responsible
3.15.4 Body parts
Unfit material must not be stored with any other carcases or body parts that have been passed fit for human consumption. The table below details the specific requirements for various body parts of the animal.
Body parts
Part | Action |
---|---|
Any offal passed fit for human consumption | Must be retained and identifiable, unless disposed of at Cat 1 ABP (SRM) by incineration |
Fleece | Must be retained in the hide / skin room but separately from other hides / fleeces / skins; must be appropriately marked or tagged and clearly labelled ‘pending test result, retain until test result is available’ |
Blood | Must be retained separately and identified pending a test result, unless disposed of as Cat 1 ABP (SRM) by incineration |
SRM | Must be disposed of by incineration |
Rumen contents and gut contents | Should be disposed of in the normal way |
Sampled carcase or body parts of sampled carcases that are not passed fit for human consumption at post-mortem inspection | Must be held as an animal by-product until a test result is received; if a FBO does not wish to hold this material until test results are obtained it must be disposed of as Cat 1 ABP (SRM) by incineration |
3.16 Despatch of samples
3.16.1 Labelling
Both bioshield and biobottle boxes are pre-printed with a diagnostic specimen label and a black UN3373 label. In addition to these labels, an SRM label should be applied to each box.
3.16.2 Collection of samples
Predict the following weeks sampling days and times that the samples will be ready for collection.
To book a collection use the Topspeed online booking system (See Annex 4 for instruction on the despatch process).
Reference: Topspeed
Under exceptional circumstances, ad-hoc changes and collections can be made on the same day of sampling by contacting BSE Customer Care Team (0844 057 0110) before noon.
3.16.3 Transport containers
Top Speed collect the bioshield box or biobottle at a pre-notified collection time for overnight delivery to:
TSE Laboratory
Eurofins Forensic Services
Darwin House
Faraday Street
Birchwood Park
Risley
WA3 6FW
Telephone: 0844 057 0110
3.16.4 Ensure sample despatch
All samples are to be despatched to the laboratory. Any sheep samples lost prior to despatch due to an error on behalf of the FSA or an issue with the FBO will have to be made up as part of the week’s deviation.
If, for any reason, Topspeed do not collect samples, DO NOT dispose of these samples at the slaughterhouse. Samples are to be despatched to the TSE Testing Laboratory irrespective of time between harvesting and eventual despatch.
3.16.5 Notify laboratory
FSA staff should advise the TSE Testing Laboratory that samples have been taken and the courier has collected the brain stem and cerebellum samples by completing a Notification of TSE Sample Sent form and faxing (01925 248876) or emailing it to them (bse.services@lgcgroup.com). A copy of the form can be obtained from SLA and Contracts Team.
(If you require the results to be sent to a single email address rather than by fax, this should be detailed in the comments section at the bottom of the form).
See Annex 6 for a sample copy of the form.
3.16.6 Arrival time of sheep samples at laboratory
Top Speed provides a same day direct delivery service to ensure that the samples arrive at the TSE Testing Laboratory in time for the results to be provided by 4pm the following day of sampling.
3.16.7 Top Speed collection problems
In the event that samples are not collected at the correct time by Top Speed, and providing it is the fault of the courier, then the OV should contact the TSE Testing Laboratory on 0844 057 0110 to request a same day collection and delivery service to the TSE Testing Laboratory.
The TSE Testing Laboratory require samples within 24 hours of slaughter and the OV must try to ensure that samples are despatched. If a delay in the delivery occurs, the results will be issued late. The OV must ascertain whether the abattoir is willing to detain the carcases for an extended period.
Any delays in the collection or delivery of samples must be reported immediately to the SLA and Contracts Team. Delays in the provision of test results caused by the courier must not impact on the FBO. Samples not picked up from Halal abattoirs are not to be held over for collection the following day.
If the samples cannot be sent to the TSE Testing Laboratory, then an ovine animal can be deselected for testing and the samples must be disposed of as Cat 1 ABP (SRM) by incineration. Such deselection and application of the Health Mark must await confirmation from SLA and Contracts team. Samples that have been taken but then are deselected cannot be counted towards the totals on the TSE 6/1 form and these numbers must be made up.
If the TSE Testing Laboratory has started a test then an animal cannot be deselected, health marked or released until a test result has been received.
3.17 Test result and health marking
3.17.1 Test result
The test result should be received at the slaughterhouse by 4 pm on the day after sampling.
Test results will either be faxed to the plant fax number or (if requested in the comments section of the Notification of TSE Samples Sent Form) to the single email address provided.
3.17.2 Negative result
Any sheep selected for testing must not have the Health Mark applied until a negative result has been obtained by fax/email from the testing laboratory. Carcases yielding a negative result must have the Health Mark stamp applied before being released for human consumption. Any remaining material, whether or not for human consumption, may be released. The FBO must apply the identification mark to the offal.
3.17.3 Positive result
In the event of a faxed / emailed positive result from the testing laboratory, the OV should ensure that all body parts of an animal found to be positive which have been retained, including the fleece, are disposed of as Cat 1 ABP (SRM) by incineration. In addition, the OV should inform the ROD via the APHA central contact number (in England), or the DVM at the local APHA office (in Wales) of the case. A copy of the TSE 6/2, TSE 6/3 or NSP 61 and NSP 61A should be faxed to the relevant APHA office and the SLA and Contracts Team.
On occasion, retesting of a positive sample and its associated negative samples may delay release of results until 9.00 am the day following testing at the TSE Testing Laboratory. The TSE Testing Laboratory will inform FSA officers and the FBO of delays.
3.17.4 Unsuitable test result
In the event that the sample is unsuitable the OV will receive a faxed / emailed notification from the laboratory on the results form and the carcases treated in the same way as negative results.
Deselection and application of the health mark must await this faxed report.
Only APHA can give permission for sheep to be deselected from testing except when they have been selected for CSFS in which case all samples must be tested. The carcase, fleece, blood and body parts can then be released.
However, if the tests are from the annual cull animals (CSFS) all unsuitable results must be treated as positive results.
Poor quality samples reported by the lab will need to be investigated. The SLA and contracts team will notify the local team from the plant affected to request an investigation Results of the investigation and, where necessary further preventative action, need to forwarded to sla.contracts@food.gov.uk , FVC and FVL.
3.17.5 Inconclusive result
In the event of an inconclusive test result, the OV should treat all of the animal body parts in the same way as for a positive result.
3.17.6 Test result flow chart
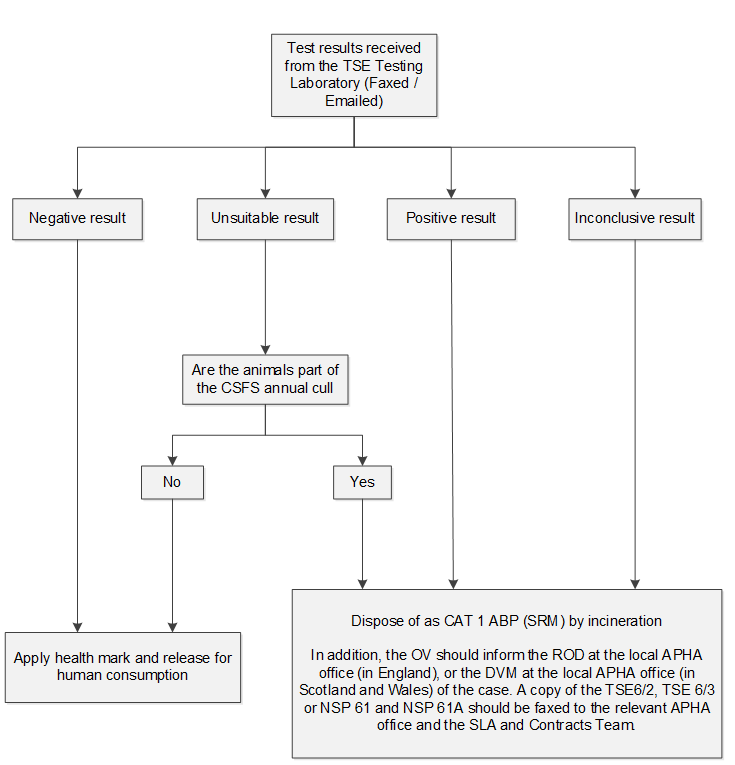
3.17.7 Non co-operation
If selected animals are not sampled and / or tested because the FBO fails to co-operate, the selected animals must not be health marked. The OV must inform SLA and Contracts Team of this action.
See chapter 7 on ‘Enforcement’ when considering any enforcement action.
4. Sheep TSE Testing: Form Completion
In this section
4.1 TSE 6/6 (Daily record sheet)
4.1 TSE 6/6: Daily record sheet (sheep and goats surveys / CSFS)
4.1.1 When and by whom?
The FSA section of the form should be filled in by an FSA AO at the dentition point. The orange tag number must be recorded in the TSE 6/6 and provides the only record that will ensure correlation between orange tag and carcase / skin.
Always protect forms against contamination (such as blood and tissue).
4.1.2 Form completion
To ensure correlation, enter the ear tag number on Daily Record Sheet (TSE 6/6) next to the spray (the kill number sprayed on the fleece) and detention (red ear tag) number with an indelible marker.
This correlates the fleece with the red tag number and ensures the ear tag number can be correctly recorded on the Rapid Testing Form (TSE 6/2) post slaughter.
Once the fleece is removed, a detention tag (colour of the day) must be applied to the carcase with the spray number written on with indelible marker.
Offal can be correlated individually or by batch, or disposed of as Cat 1 ABP SRM.
4.1.3 Filing
Retain the completed TSE 6/6 in the FSA office with a photocopy of the TSE 6/2 for matching against the test results.
4.2 TSE 6/2: Rapid testing form (sheep and goat surveys)
4.2.1 When and by whom?
A TSE 6/2 form must be completed for each sample taken from selected sheep intended for human consumption or from DoA/DiL eligible sheep in participant slaughterhouses.
The FSA section of the form should be filled in prior to slaughter (at the point of animal selection) in the case of sheep intended to slaughter and when identified in the case of DoA/DiL sheep by an FSA AO, except for the insertion of the number of permanent incisors erupted which must be done after the dentition check.
Always protect forms against contamination (such as blood and tissue).
4.2.2 Form completion
The following points should be noted when completing the TSE 6/2 form:
- it is critical that only one of the options in the TSE 6/2 form for the Scrapie surveillance is clearly marked. This allows the laboratory to assign the sample and the result in the correct sampling category
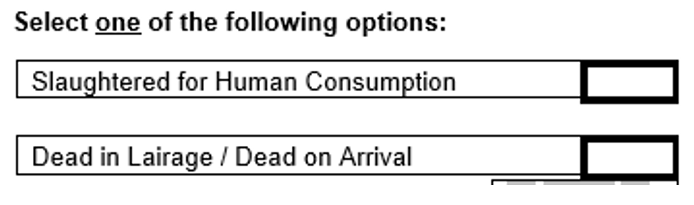
- the vendor name and address are the name of the dealer or farmer (not the slaughterhouse) that owned the animal prior to the arrival at the slaughterhouse
- Sheep intended to slaughter that do not have a flock mark or individual tag should not be sampled; any information missing must be recorded as ‘‘Not Known’’
- if the DIL/DOA sheep does not have a farmer’s mark, lot number, tattoo number or other mark the relevant data boxes should be left blank
- if breed cannot be reliably identified then the relevant data box should be annotated ‘‘Not Known’’
- it is important that boxes relating to teeth are completed as they confirm the age of the animal
- other identification present should be recorded.
4.2.3 Ear tag number
Take care when recording the number of the red ear tag as this is the link between the sample and the sample details which will be recorded on databases.
4.2.4 Form distribution and filing
Make a photocopy to be retained by the FSA in the OV office in plant for 12 months. The original TSE 6/2 should be despatched with the sample.
Retain the photocopies of each TSE 6/2 with the completed TSE 6/6 in the FSA office for matching against the test results.
4.3 NSP 61 (CSFS)
4.3.1 When and by whom?
An FSA officer must complete Section 2 of the NSP 61 form prior to despatch of CSFS samples.
Always protect forms against contamination (such as blood and tissue).
Note: The NSP 61 form is currently under review with APHA and will be added as an annex once published.
4.3.2 Form distribution and filing
Record if there is one or more DoA or DiL (details will be recorded in Section 2 of NSP 61 under the DIT/DIL samples column). If one, the pink copy of the NSP 61 will accompany the head. If more than one, a photocopy of the form will accompany the head for each DoA or DiL.
Protect forms against contamination (such as blood and tissue).
The separate copies of the form are to be sent as follows:
- yellow copy – to be retained by FSA in plant for 12 months
- blue copy – despatched with samples; this is for the TSE Testing Laboratory to send to APHA Weybridge
- white copy – despatched with samples to the TSE Testing Laboratory
- pink copy – despatched with DOA/DIL head(s) (if applicable)
- green copy – send in pre-printed envelope to ‘SSC, Membership Admin’
4.4 NSP 61A (CSFS)
4.4.1 When and by whom?
An FSA officer must complete columns 1 and 2 of the NSP 61A form prior to despatch of CSFS samples.
Always protect forms against contamination (such as blood and tissue).
Note: The NSP 61A form is currently under review with APHA and will be added as an annex once published.
4.4.2 Form completion
Form NSP 61A is not self-carbonated. Keep a photocopy of the original before sending it with the samples. There is no need to complete a TSE 6/2 for these animals.
Once the sample has been taken, record the sample number in column 1.
If any animal with an orange tag is found DoA or DiL, a tick is to be entered in column 2 (DIT/DIL) next to the animal’s details.
When the form has been completed, verify that every animal requiring testing has been sampled. If any animal is submitted for slaughter with an orange tag but is not included in the NSP 61A, record the details in the form.
4.4.3 Form distribution
Once completed make a second photocopy to be sent in the pre-printed envelope to ‘‘SSC Membership Admin’’.
4.4.4 Reporting discrepancies
Any discrepancy found between the information recorded on the NSP 61A and the animals presented must be reported to the SSC (Worcester) as follows:
SSC (Worcester) telephone: 01905 768741
OR
SSC Helpline: 0845 601 4858
OR
SSC fax number: 01905 768742
4.5 TSE 6/1: Weekly summary and deviation report (sheep and goats surveys / CSFS)
4.5.1 When and by whom?
By an FSA officer at the end of each week (Monday to Sunday).
Always protect forms against contamination (such as blood and tissue).
4.5.2 Weekly summary and deviations report: sheep survey
Complete Part 1 on the TSE 6/1, recording daily throughput and both daily and weekly surpluses and shortfalls.
Throughput information will be correlated against Defra’s statistical information.
Any weekly shortfall of samples must be carried forward to the following week and must be made up. The deviation should remain as close to zero as possible.
4.5.3 Weekly summary and deviations report: goat survey
We are currently not sampling goats so Part 2 of the form is not required to be completed.
4.5.4 Weekly summary and deviations report: CSFS
Complete Part 3 on the TSE 6/1 form, recording the number of samples collected on the relevant day(s).
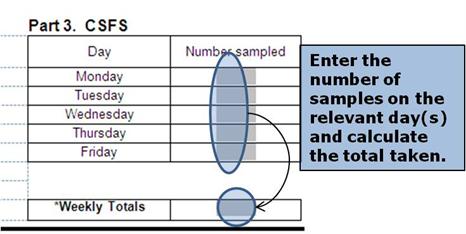
Note: CSFS samples must not be included with any normal samples recorded in Part 1 of the form.
4.5.5 Weekly summary and deviations report: general
Once completed, email a copy to the SLA and Contracts Team.
The deadline for submission is (except in exceptional circumstances agreed by SLA) 10am on the following Monday.
5. Annexes
N.B. These pages can only be accessed by FSA staff on FSA devices.
Annex 2: Hazard identification and control plan
Annex 3: Test categories for bovine brain stems
Annex 4: Sample despatch process
Annex 5: Sample TSE Testing Laboratory consumable order form
Annex 6: Sample notification of TSE samples sent to the TSE Testing Laboratory for testing
Revision log
Published: 11 January 2022
Last updated: 12 September 2023