Risk of campylobacteriosis from low-throughput poultry slaughterhouses
This report estimates the difference in risk of campylobacteriosis for products from low-throughput and high-throughput poultry slaughterhouses in the UK
Campylobacter is the most common cause of bacterial foodborne illness in the UK. Every year there are an estimated 300,000 foodborne cases in the UK, of which more than half are related to poultry meat.
Campylobacter naturally lives in the guts of poultry. Undercooked chicken meat is the main source of exposure to Campylobacter. Thorough cooking kills Campylobacter. Cross-contamination of other food or work surfaces during preparation or storage of chicken can also cause illness.
Campylobacter levels are routinely monitored in chicken carcases that are processed in high-throughput slaughterhouses, but this testing is not currently carried out in some low-throughput slaughterhouses. Each high-throughput slaughterhouse processes more than 7.5 million birds per year and each low-throughput slaughterhouse processes less than 7.5 million birds per year. Of the 1 billion birds that are slaughtered annually in the UK, around 5% come from low-throughout slaughterhouses. This report estimates the difference in risk of campylobacteriosis for products from low-throughput and high-throughput poultry slaughterhouses in the UK. This was necessary work to assist the FSA in establishing an appropriate level of sampling for low-throughput slaughterhouses.
We considered the whole pathway of the chicken from farm to fork using the scientific literature, data from our own survey of Campylobacter in slaughterhouses (FS9990010), and business data and information on UK levels of infection. Campylobacter levels over a 3-month period (September to December 2021) from chicken processed by low and high-throughput slaughterhouses were the main data used for our comparison. We could find no data on differences in the supply of birds to low- versus high-throughput abattoirs, and no data on differences in the use of the meat after leaving the slaughterhouses.
Based on analysis of the limited survey data available, we could not detect a significant difference between the proportion of highly contaminated samples from low- and high-throughput slaughterhouses. We also could not detect a significant difference in Campylobacter levels in slaughterhouses that perform religious slaughter versus those that do not.
Based on the number of chickens per year that are processed by low and high-throughput slaughterhouses, we estimated the number of Campylobacter cases in the UK annually that are likely linked to low- and high-throughput slaughterhouses respectively. Based on the evidence available, we conclude that the frequency of occurrence of campylobacteriosis in the total UK population from chicken produced in low-throughput slaughterhouses is medium and for high-throughput slaughterhouses is high, with a medium uncertainty, as a direct consequence of the relative volume of chicken produced by each type of plant. The severity of campylobacteriosis is low, with low uncertainty. This assumes that the proportion of the total domestic consumption of chicken meat originating from low-throughput slaughterhouses does not change.
The current sampling regime requires samples to be taken once a week. If more than 15 out of 50 of samples have high levels of Campylobacter, this is considered a failure and mitigations need to be put in place. We predicted that if samples are taken once every two weeks or once every four weeks instead, that would still allow us to identify some slaughterhouses failing to comply with the 15/50 exceedance rate. However, identifying issues will take longer and may not detect some failing slaughterhouses.
Sampling requirements are not consistently applied in low-throughput slaughterhouses, and we did not have access to data on the steps taken when slaughterhouses recorded high levels of Campylobacter. Therefore, it was not possible to state the effect of changes in sampling requirements on per-portion risk. However, due to the small proportion of total poultry meat consumed in the UK that is produced at low-throughput slaughterhouses, changes to the official sampling requirements at low-throughput slaughterhouses are unlikely to result in a large difference in the frequency of occurrence of campylobacteriosis in the UK population.
Campylobacter is the most common cause of bacterial gastroenteritis in the UK. Every year there are an estimated 300,000 foodborne cases in the UK, of which more than half are related to poultry meat.
Poultry is the main reservoir for Campylobacter and undercooked poultry presents a risk to the consumer of becoming infected with Campylobacter, while thorough cooking kills Campylobacter. Infection may also result as a consequence of cross-contamination during preparation or storage of chicken.
Slaughterhouses are classified as either low-throughput (≤7.5 million birds per year) or high-throughput (>7.5 million birds per year). Campylobacter levels are routinely monitored in chicken carcases that are processed in high-throughput slaughterhouses. Established process hygiene criteria (PHC) state the samples submitted by slaughterhouses currently should not exceed 1,000 CFU/g Campylobacter in more than 30% of samples submitted. The microbiological criteria regulation is the same for high-throughput and low-throughput slaughterhouses, however, testing is not currently carried out in all low-throughput slaughterhouses due to the financial burden of routine testing. This work was commissioned to assist the FSA to make a risk-based decision on whether a tailored-made sampling regime for small-throughput slaughterhouses would be appropriate.
We considered the whole pathway of the chicken from farm to fork using scientific literature, data from own survey of Campylobacter in slaughterhouses, in addition to business data and information regarding UK levels of infection from Campylobacter.
Overall, there was no significant difference between the proportion of highly contaminated samples (>1,000 CFU/g) gathered from low and high-throughput slaughterhouses. Using the number of chickens per year that are processed by low and high-throughput slaughterhouses, we estimated that high-throughput slaughterhouses contribute a significantly larger number of Campylobacter cases due to their volume. Currently, most chicken on sale in the UK is produced in high-throughput plants. All else being equal, small improvements to large plants will have a bigger impact on the overall risk to the UK consumer population than large changes to a far smaller plants.
A number of uncertainties and evidence gaps were identified during this risk assessment. We had no information as to the method in which the poultry were reared prior to arriving at the slaughterhouse and are aware that evidence suggests that this can directly affect Campylobacter levels at slaughter. Data on low-throughput abattoirs were only available for a limited period of three months and at the end of slaughter. There was no information available as to the onward processing of meat handled by slaughterhouses, and we therefore assumed that low and high-throughput slaughterhouses contribute equally to retail and hospitality etc. In addition, we assumed that only UK slaughtered chicken is consumed in the UK.
In conclusion, with currently available data it is not possible to identify any difference between the current per portion risk of Campylobacteriosis to consumers for low and high-throughput slaughterhouses. We also conclude that the frequency of occurrence of campylobacteriosis in the total UK population from chicken produced in low-throughput slaughterhouses is medium and for high-throughput slaughterhouses, this is high. The uncertainty associated with this frequency is medium. The risk assessment concludes that the severity of Campylobacter infection is low, with low uncertainty. This assumes that the proportion of the total domestic consumption of chicken meat originating from low-throughput slaughterhouses does not change.
The current sampling regime requires samples to be taken once a week. If more than 15 out of 50 samples have high levels of Campylobacter, this is considered a failure and mitigations need to be put in place. We predicted that if samples are taken once every two weeks or once every 4 weeks instead, that would still allow us to identify some slaughterhouses failing to comply with the 15/50 exceedance rate (71% and 57%, respectively). However, identifying issues will take longer and may not detect some failing slaughterhouses, and may affect behaviours in the plant, for example, less frequent sampling may affect standards during processing.
There is a lack of consistency in the application of sampling requirements in low-throughput slaughterhouses and a lack of information on the corrective actions taken in the event of an exceedance. Therefore, it is not possible to differentiate the effect on per-portion risk of changes to current sampling requirements. However, due to the small proportion of total poultry meat consumed in the UK that is produced at low-throughput slaughterhouses, changes to the official sampling requirements at low-throughput slaughterhouses are unlikely to result in a large change in the total number of cases of campylobacteriosis in the UK population.
This evidence will assist FSA risk managers to establish appropriate and proportionate levels of Campylobacter sampling for low-throughput slaughterhouses. A two-dimensional risk framework was used in this work, where risk is expressed in terms of both probability and impact in a two-dimensional manner, in addition to improvements in the communication of uncertainty (ACMSF, 2020).
1.1 Scope of risk assessment
We aim to assess the per-portion risk, and population-level risk, to UK consumers posed by consumption of broiler meat from broiler carcases slaughtered in low-throughput slaughterhouses, using high-throughput slaughterhouses (footnote 1) as the baseline.
All broiler slaughterhouses must comply with the sampling and testing requirements of Retained Commission Regulation 2073/2005. If a certain proportion of samples have high Campylobacter levels, hygiene measures need to be implemented at the plant to reduce them. Annex I Chapter III of this regulation allows, on the basis of a risk analysis, small slaughterhouses producing fresh poultry meat in small quantities to be exempted from the prescribed sampling frequencies. This risk assessment will inform considerations of whether an exception from the prescribed sampling frequency can be applied.
The exposure assessment for this risk assessment was conducted by considering each step of the pathway from farm to fork in the production of broiler meat in the UK. Each step was treated as an individual module, with the factors affecting Campylobacter levels assessed. These modules were identified as farm, abattoir, retail and consumer.
In addition, we assess how the risk is affected by the following four sampling scenarios:
a) Sampling on a weekly basis as per current regulation
b) Not sampling/testing to ascertain compliance with the Campylobacter Process Hygiene Criteria (PHC)
c) Sampling every other week as is permitted when establishments can demonstrate compliance with the Campylobacter PHC for a continuous period of 52 weeks
d) Sampling at a rate of once every 4 weeks
In each of these scenarios, sampling can be assumed to mean sampling carried out according to the PHC. For Campylobacter, the requirements are for there to be a maximum number of samples with high levels (more than 1,000 CFU/g) in 10 consecutive sampling sessions (that is 50 samples). The current criterion accepts up to 15/50 samples with high levels of Campylobacter spp. to be compliant. For the risk assessment, the criterion of 15/50 will remain the same regardless of the frequency of testing i.e. whether the sampling sessions are carried out over a 10, 20 or 40 week period.
1.2 Legislation
Retained Commission Regulation 2073/2005 includes criteria for the Campylobacter PHC in Annex I, Chapter 2. Within this Annex, Table 2.1 point 9 states that “all broiler slaughterhouses must comply with the sampling and testing requirements”. The requirements are that 50 samples are derived from 10 consecutive sampling sessions. Each sample consists of least 3 pooled neck skins from carcases after chilling. This means a minimum of 15 broiler carcases are required in each sampling session.
Since January 2020, no more than 15 samples out of 50 should exceed 1,000 CFU/g Campylobacter. From the 1st of January 2025, no more than 10 samples out of 50 should exceed 1,000 CFU/g Campylobacter.
The legislation also states that an exceedance requires the following actions to be taken: improvements in slaughter hygiene; review of process controls of animals' origin and of the biosecurity measures in the farms of origin.
However, the annex allows for the central authority, on the basis of a risk analysis, to authorise small slaughterhouses producing fresh poultry meat in small quantities to be exempted from the prescribed sampling frequencies.
Campylobacter species are Gram-negative spiral, rod-shaped, or curved bacteria which do not sporulate. There are more than 20 species of Campylobacter, and the most common pathogenic species causing gastroenteritis in humans are C. jejuni and C. coli. Other species, such as C. concisus, C. lari, C. hyointestinalis and C. ureolyticus, may be rarely involved in gastroenteritis (Kaakoush, Mitchell and Man, 2015). Campylobacter is the most common cause of bacterial gastroenteritis in the UK, with an estimated 300,000 cases in England and Wales annually (Holland and Mahmoudzadeh, 2020).
Infection with Campylobacter typically leads to diarrhoea (frequently bloody), abdominal pain, fever, headache, nausea and/or vomiting. In rare cases, it can also lead to long term complications such as reactive arthritis and Guillain-Barré syndrome (ACMSF, 2019).
The main reservoir of Campylobacter is poultry but it can also live in the gastrointestinal tract of mammals including livestock and pets, such as cats and dogs (Kaakoush et al., 2015). A recent study found that approximately 70% of C. jejuni and almost 50% of C. coli infections were linked to chicken as the source (Oxford University, 2021). Undercooked poultry meat presents a risk of campylobacteriosis and while thorough cooking kills Campylobacter, infection may also result as a consequence of cross-contamination during preparation or storage of chicken.
Implementation of controls during poultry slaughter is thought to reduce contamination of carcases, leading to a reduced public health risk (EFSA Panel on Biological Hazards (BIOHAZ), 2011). Measures such as appropriately cleaning and disinfecting equipment like evisceration machines, and processes like scalding, steam-ultrasound treatment and chilling can decrease the Campylobacter contamination on carcases (Rasschaert et al., 2020).
The EU Commission established process hygiene criteria (PHC) for Campylobacter spp. on broiler carcases to indicate the acceptable functioning of the slaughter process and increase the number of carcases that comply with microbiological criteria with a critical limit of 1,000 CFU/g Campylobacter spp (footnote 1). The PHC requires the Food Business Operator (FBO) to test 5 pooled samples of 15 neck skins, once a week, for Campylobacter spp. If more than 15 samples out of 50 have high levels of Campylobacter in a period of 10 consecutive weeks, this is considered unsatisfactory and actions need to be taken, such as improvements in slaughter hygiene, review of process controls, of animals' origin and of the biosecurity measures in the farms of origin.
Low-throughput broiler slaughterhouses are disproportionately impacted economically by the current sampling requirements (FSA, 2019a). This report lists the evidence gathered for the campylobacteriosis disease burden attributable to low-throughput broiler slaughterhouses in comparison to high-throughput plants and provides recommendations for alternative sampling schemes.
- raw or undercooked meat, especially poultry.
- unpasteurised milk
- untreated water
3.1 Cases and outbreaks
The Infectious Intestinal Disease study determined that Campylobacter was the most common bacterial pathogen isolated from the stools of patients reporting infectious intestinal disease, with an underreporting factor of 9.3 (Tam et al., 2012). The study estimated that Campylobacter caused 500,000 cases per year and was the most common foodborne pathogen in the UK. A further study refined the figure to 300,000 foodborne cases in the UK in 2018 (Holland and Mahmoudzadeh, 2020).
Campylobacter rates reported in the Advisory Committee of the Microbiological Safety of Food (ACMSF) Epidemiology of Foodborne Infections Group meeting showed a fairly constant trend in recent years, with reduced reporting in 2020 likely due to the COVID-19 pandemic (Figure 1). In 2021, 67,588 cases were reported in the UK.
Figure 1: Rate of reported Campylobacter infections by country per 100,000 population 2012 – 2021 (Epidemiology of Foodborne Infections Group, 2022, unpublished data).
Although most campylobacteriosis cases are sporadic, Holland et al. reported Campylobacter being associated with 147 outbreaks with 2950 cases, and 36,895 hospital discharges between 2001 and 2016 (Holland et al., 2020). Deaths from foodborne disease are not routinely recorded and when death occurs from infectious intestinal disease the pathogen is not always specified. Despite this, Campylobacter is the pathogen most often mentioned on a death certificate, when the underlying cause is an infectious intestinal disease (Holland et al., 2020).
3.2 Disease characterisation
The infectious dose of Campylobacter has been reported to be as low as 500 cells (Robinson, 1981), however the probability of infection at low doses is very low. A recent overview of challenge studies found that the infective dose required to infect 50% of the population is 3,300 cells (Teunis et al., 2018).
The incubation period for Campylobacter is usually 2 to 5 days with a range of 1 to 11 days.
The most common clinical symptoms of Campylobacter infections are diarrhoea (frequently bloody), abdominal pain, fever, headache, nausea and/or vomiting. These symptoms typically last 3 to 6 days. Gastroenteritis induced by C. coli is clinically indistinguishable to that of C. jejuni, but patients infected with other Campylobacter spp. report milder symptoms (Kaakoush et al., 2015). The estimated hospitalisation rate for campylobacteriosis in the UK is around 1%, which is less than other bacterial gastrointestinal pathogens such as Salmonella and Shiga toxin-producing Escherichia coli (O’Brien et al., 2016).
Campylobacter infection can lead to long term complications such as reactive arthritis (9 in every 1,000 cases), Guillain-Barré syndrome (1 in every 1,000 cases) and other rare late consequences, such as Miller Fisher syndrome, haemolytic uremic syndrome, inflammatory bowel disease and functional gastrointestinal disorders (ACMSF, 2019).
Campylobacter infections are equally common in males and females, with infants and children in the 0–4 years age group more likely to be affected. It is more prevalent during the summer months.
The pathway of broilers from farm to fork is complex and includes multiple stages where the risk of Campylobacter contamination and/or cross-contamination may occur. We break down the exposure pathway into four key stages: production at the farm, processing at the slaughterhouse, post-processing at retail and home-preparation by the consumer. Each module contains variables likely to influence the presence of Campylobacter in poultry, summarised in the following sections. In this report, we focus on the differences in the production chain of low and high-throughput slaughterhouses. Semi-quantitative tools were used to give an approximate estimate of the number of illnesses and the Campylobacter risk (per portion and at the UK population level) from chicken produced by low-throughput poultry slaughterhouses in comparison to high-throughput poultry slaughterhouses.
Figure 2: The exposure pathway for this risk assessment, broken down into four key modules
- Farm
- Slaughterhouse
- Retail
- Consumer
4.1 Farm module
4.1.1 Factors affecting Campylobacter levels at a farm level
At the farm level, a number of factors have been found to affect the probability of contamination of a portion of broiler meat with Campylobacter. These include biosecurity procedures, organic farming methods, the practice of thinning, partial de-population, seasonality, and the age of the bird at slaughter, as summarised in a recent FSA-funded study on Campylobacter levels during the farm module of poultry production, FS307037 (Ausvet Europe et al., 2022).
Thinning
A major contributor to increased Campylobacter levels in poultry houses is thinning. Thinning is the removing of unwanted birds from flocks and is widely used by most commercial producers (Allen et al., 2008). This process may increase Campylobacter levels for two reasons; contamination by farm workers during the process (biosecurity hazard) and the stress it puts on the birds. In a study by Georgiev et al., even flocks raised with good levels of biosecurity had increased levels of Campylobacter of up to 54.7% after thinning and at processing, and carcases from flocks that were thinned were twice as likely to have Campylobacter than those that were not (Georgiev, Beauvais and Guitian, 2017).
Biosecurity
Farms with poor biosecurity practices were also found to have an increased risk of Campylobacter contamination. A conventional poultry house, that is modern and well maintained and with limited access, is considered to have good biosecurity (EFSA Panel on Biological Hazards (BIOHAZ), 2011). Common breaches of biosecurity measures occur through vectors such as vermin, insects or humans. Farm workers in particular have been reported to be a major source of Campylobacter spread via poor hygiene practices and contaminated clothing and boots (Battersby, Whyte and Bolton, 2016).
Organic farming
Studies show mixed results on the effects of organic farming procedures on the risk of Campylobacter colonisation in flocks. Organic farms are considered to have poor biosecurity due to exposure of the poultry to the outside environment, leading to transmission routes from wild birds and other wild animals (Ausvet Europe et al., 2022). Studies in Denmark have shown that while conventional and indoor broiler flocks have an infection rate of 36.7% (positive samples from 29 out of 79 flocks tested) and 49.2% (positive samples from 29 out of 59 flocks tested) respectively, organic flocks had an infection rate of 100% (positive samples from 22 out of 22 flocks tested) (Heuer et al., 2001). Furthermore, in Denmark, the prevalence of Campylobacter contamination in conventional carcases was found to be 19.7% while in organic carcases this was found to be higher at 54.2%.
Similar studies have not been carried out in the UK, however, our survey of low-throughput slaughterhouses found that in contrast to this, organic carcases and conventional carcases had a similar levels of samples with high Campylobacter levels (24.3% vs 26.6% respectively). A survey of chicken at major and non-major retailer stores also found no statistical difference in the percentage of highly contaminated samples between those obtained from free-range and organically reared birds and those reared under a standard regime (PHE, 2021; Jorgensen et al., 2019).
Seasonality
Seasonal variation of Campylobacter levels is also frequently reported. In the UK, prevalence of Campylobacter in flocks was found to increase between July and September. This peak was more clearly evident in the south, thought to be due to warmer climate (Jorgensen et al., 2011).
Bird age
The age of the flock has been found to correlate with increasing Campylobacter levels. Conventionally produced birds are consistently reported to have higher levels of Campylobacter contamination by the end of the production cycle compared to younger birds (EFSA Panel on Biological Hazards (BIOHAZ) et al., 2020).
Transport
Crates used to transport live poultry to slaughterhouses can be contaminated with Campylobacter spp. and provide a risk of cross-contamination between flocks (Hastings et al., 2011).
Other factors for consideration
As part of the AusVet Europe et al., 2022 study, two workshops were held to discuss the findings of their literature search with key representatives from the UK poultry industry. Additional risk factors were identified at these meetings, including the effect of stocking density. Also, a need for additional information regarding organic versus conventional production methods was highlighted, as well as information on the effect of bird age on contamination levels and the effect of breeder flock.
4.1.2 Effect of controls applied at farm level
Some effective controls that could be applied at farm level in response to an exceedance, are outlined below and have been discussed at length in a recent EFSA report (EFSA Panel on Biological Hazards (BIOHAZ) et al., 2020). It is of note that an FSA funded study estimated that on-farm factors were 3.5x more important at influencing levels of Campylobacter spp. in neck skins than slaughterhouse factors (Hutchison et al., 2016).
Addition of disinfectants to drinking water and avoiding drinkers that allow standing water
One significant source of Campylobacter on farms is contaminated drinking water. It has been reported that adding organic acids, chlorine-based biocides or hydrogen peroxide to the drinking water could reduce the risk of Campylobacter-positive flocks by up to 55% (EFSA). In the UK, chlorination of drinking water has been found to be effective (Ellis-Iversen et al., 2009), while acidification and hydrogen peroxide have also been reported to be successful in France and Spain, respectively (Torralbo et al., 2014; V. Allain et al., 2014). Drinker types that allow for standing water are also associated with increased risk. One study found that removing drinking devices that included trays/cups etc reduced the risk of Campylobacter contamination in water sources by up to 78% (Näther et al., 2009).
Effective rodent control and proximity to other animals
Another common source of Campylobacter contamination on farms is rodents, with some studies estimating that effective rodent control can decrease prevalence in flocks by up to 19% (McDowell et al., 2008; V. Allain et al., 2014). This has been found for both indoor and outdoor flocks (Huneau-Salaün et al., 2007).
As well as rodents on farms, other animals in adjacent fields have been speculated to be a source of Campylobacter contamination. Several studies have sequenced Campylobacter found in both broilers and animals in the surrounding area and identified them as the same strains, although the direction of spread is often hard to determine (Weis et al., 2016).
Employing few and well-trained staff
Another commonly accepted source of Campylobacter contamination on farms is from farm workers (including maintenance staff and handlers), often via poor hygiene techniques and contaminated footwear (Battersby, Whyte and Bolton, 2016). Several studies have shown infection decreases with increased education of staff on good hygiene practices (Ansari-Lari et al., 2011; Van Limbergen et al., 2018). Furthermore, limiting the number of farm workers with access to the flock was also found to be effective. For example, studies in Denmark and France concluded that having more than one farm worker managing a flock was sufficient to significantly increase the risk of Campylobacter infection (Refrégier-Petton et al., 2001; Chowdhury et al., 2012).
Hygiene anterooms at broiler house entrance
The presence of an anteroom (a room between the outside door and the entry to the housing unit) on farms are an important addition to farm control measures and are effective at reducing Campylobacter risk when used along with good hygiene practices. The anterooms allow staff to put on clean overalls/change footwear/wash hands etc. before entering the production unit. They have been shown to result in between 5% and 13% reduction in the Campylobacter prevalence only, however, when kept clean and used correctly (McDowell et al., 2008; Borck Høg et al., 2016).
Supply of birds with full crops
Another factor identified in a slaughterhouse study as responsible for cross-contamination is the supply of birds with full crops (IPSOS Mori, 2016). Farmers are encouraged to leave enough time before the last feed and transport to the slaughterhouse, to ensure the crop is empty, which presents less chance of cross-contamination during evisceration.
4.1.3 Differences in the Campylobacter levels of birds supplied to low-throughout and high-throughput premises
Following a farm to fork approach, ideally Campylobacter levels in birds supplied to low- and high-throughput slaughterhouses would be compared. However, these data were not available. Instead, an attempt was made to identify the proportion of different types of poultry processed in the two types of slaughterhouses, specifically; conventional, organic, free range and the types of cages and/or barns used. The literature suggests there is a difference in Campylobacter risk for birds reared under different conditions.
Although some slaughterhouses provided these details, the information was limited and often slaughterhouses receive a mixture of differently reared flocks. It was therefore not possible to compile a reliable and comprehensive list to enable the comparison of birds supplied to low-throughput slaughterhouses with birds supplied to high-throughput slaughterhouses for the purposes of this report (uncertainty).
With the data available, it was not possible to assess any difference in the Campylobacter levels between broilers being sent to low and high-throughput slaughterhouses that we can quantify in this module.
4.2 Slaughterhouse module
4.2.1 Factors affecting changes in Campylobacter levels during slaughter
At the slaughterhouse level, a number of factors have been found to affect the probability and levels of contamination of a portion of broiler meat with Campylobacter. These include how process steps such as scalding, washing, chilling, cutting, defeathering and evisceration are carried out.
The recent FS307037 study indicated an increase in prevalence of contamination as well as the level of contamination per product during slaughter (Ausvet Europe et al., 2022).
Scalding and washing:
Studies have shown that scalding can lead to a 2 log decrease in Campylobacter levels, however some evidence suggests that Campylobacter may survive in scalding water due to the presence of organic matter (Rasschaert et al., 2020). Other studies have shown that kosher abattoirs often have higher levels of contamination (94%) compared to conventional abattoirs (32%); one reason being due to the fact defeathering is carried out using cold water, rather than scalding methods (Guirin et al., 2020).
Defeathering and evisceration:
Defeathering puts pressure on the carcase which may lead to increased defecation and therefore possible contamination (Rasschaert et al., 2020). Evisceration may also rupture the intestines if machinery isn’t adjusted adequately to bird size. Batches of chickens with <10% ruptured intestines have significantly lower levels of Campylobacter compared to those with >10% (Rasschaert et al., 2020).
he FS307037 study found that defeathering and evisceration increased the risk of cross-contamination of flocks which had been negative for Campylobacter, potentially due to cross-contamination and/or contamination associated with faecal content leakage (Ausvet Europe et al., 2022). This was consistent with much of the literature, such as (Allen et al., 2007) and (Dogan et al., 2019) which estimated Campylobacter prevalence at the end of the slaughterhouse process to be 60% and 30% respectively.
Chilling
Air-chilling (the only type practised for broiler carcases) has been shown to result in a significant reduction of 0.83 log10 CFU/g (Rosenquist et al., 2006).
Other considerations
It should be noted that neck skin samples are likely to be more highly contaminated than breast skin (Hutchison et al., 2016).
4.2.2 Effect of controls applied at slaughterhouse level
If the proportion of samples with high Campylobacter levels exceeds 15/50 over a ten-week period, the PHC requires interventions to be put in place to reduce this.
An FSA-funded study on “Reducing Campylobacter cross-contamination during poultry processing” (FS9990010) looked at the practical control strategies that can be used within slaughterhouses to reduce cross-contamination of poultry with Campylobacter (Corry et al., 2017). This survey revealed that techniques used between different chicken slaughterhouses were similar and that the cleaning and disinfecting methods were effective against Campylobacter. It is noted that cleaning and disinfecting was only possible between shifts (overnight) or at the weekend and that cross-contamination between carcases on the line was unavoidable (Corry et al., 2017).
The rubber fingers of the plucking and evisceration equipment as well as the conveyer belts have been found to be key contamination points even after cleaning (Rasschaert et al., 2020). This may be due to the presence of organic matter which may protect Campylobacter spp. or the pathogen may form biofilms with Pseudomonads for protection (Rasschaert et al., 2020). Chillers have also been found to be a source of cross-contamination as they are seldom empty between batches and they are very hard to clean (Hutchison et al., 2016).
The most effective Campylobacter reduction methods were end-product treatment of the fully processed carcases (Corry et al., 2017). Steam treatment for 15 seconds was found to reduce levels by 1.28 log10 CFU/g on breast skin and 0.53 log10 CFU/g on neck skin. Heat treatment with steam or hot water has been previously shown to be effective in studies (Corry et al., 2007; James et al., 2007).
Processing of Campylobacter negative flocks after positive flocks was not found to have a significant effect on Campylobacter levels (Corry et al., 2017).
A review of the effects of transport and slaughter on Campylobacter spp. levels found that the use of steam-ultrasound treatment on carcases was effective (Rasschaert et al., 2020).
4.2.3 Probability that action is taken as a result of an exceedance
Following a farm to fork approach, we tried to gather evidence to understand the actions being taken as a result of failing PHC requirements (having more than 15/50 samples with high levels of Campylobacter over a 10-week period). Currently, no enforcement actions are taken as a result of slaughterhouses failing to sample or failing the PHC requirements (FSA, 2022). Interventions are left to the discretion of the slaughterhouse, although it should be noted that major retailers can apply pressure on the plants to provide poultry with low levels of Campylobacter (Antic, 2022).
4.2.4 Sampling from low and high-throughput slaughterhouses
The total throughput of UK slaughterhouses based on 2021 data is shown in Table 1, with individual throughout data in Appendix Section 8.2. For the purposes of this assessment, the definition of a low-throughput slaughterhouse is one that processes 7,500,000 birds a year or fewer; high-throughput slaughterhouses process more than 7,500,000 birds (FSA, 2019b). There were 38 low-throughput slaughterhouses and 22 high-throughput slaughterhouses registered in the UK, although only 34 in total have provided Campylobacter samples (uncertainty).
Table 1: Annual throughput of poultry (units) in low and high-throughput slaughterhouses in 2021
Low-throughput (%) | High-throughput (%) | Combined |
---|---|---|
53,630,892 (5%) | 965,216,124 (95%) | 1,018,847,016 |
In order to compare low and high-throughput slaughterhouses, 50 samples from some low-throughput slaughterhouse were taken over an approximately 10-week period from September to December 2021 by the FSA (see Section 8.1 for a description of the sampling and Annex 1 for the raw data) to supplement Campylobacter sampling data provided to the FSA by FBOs. In brief, a sample consists of 26 grams from 3 pooled neck skins obtained after slaughter and after chilling. If neck skin was not available, a swab of the carcase was used instead. Five samples are taken at random each week from 15 birds from the same batch on a given day. While the regulation requires 50 samples to be submitted over a 10-week period, some slaughterhouses perform and submit more sample results to the FSA.
Seventeen slaughterhouses of each type submitted results over this 10-week period. Data from the FSA survey contains enumeration of Campylobacter levels, while data submitted by slaughterhouse FBOs only contains information on whether samples had Campylobacter levels above or below 1,000 CFU/g.
The number of samples in the low-throughput slaughterhouse group was 934 across 17 slaughterhouses, as part of the FSA survey and the regular PHC reporting protocol. The high-throughput slaughterhouses reported 1972 results across 17 slaughterhouses as part of the regular PHC reporting protocol. Table 2 shows the percentage of samples (neck skin only and swab) taken in both low and high-throughput slaughterhouses that had high levels of Campylobacter.
Table 2: Number and percentage of total samples taken in low-throughput and high-throughput slaughterhouses that had high (>1,000 CFU/g) and low (<1,000 CFU/g) levels of Campylobacter over the 10-week period of study
Samples | Low-throughput | High-throughput |
---|---|---|
Samples above 1,000 CFU/g | 197 (21%) | 352 (18%) |
Samples below 1,000 CFU/g | 737 (79%) | 1620 (82%) |
Total samples | 934 (100%) | 1972 (100%) |
4.2.4.1 Campylobacter results over 10-week period - pooled
Given that slaughterhouses can be said to have “passed” or “failed” the PHC criteria, a binomial process can be used to model the outcome of testing for both types of slaughterhouse.
The prevalence of samples with high Campylobacter levels in low-throughput and high-throughput slaughterhouses was modelled using a beta distribution. The modelling confirms that, when pooled, the percentage of highly contaminated samples was not significantly different (Figure 2). For slaughterhouses who had submitted over 60 samples for assessment, only 60 random results were assessed. This was done in order to reduce the risk of bias from an individual plant submitting many samples in this period and thus skewing the pooled results. The number of samples assessed were 844 for low and 915 for high-throughput slaughterhouses. 22% of samples from low-throughput slaughterhouses had high contamination levels compared to 22% of high-throughput slaughterhouses.
As shown in Figure 2, the distributions of prevalence overlap quite closely, and there is no significant difference at the 5% level between the two types of plant when the results are pooled.
Figure 3: Distributions for the modelled prevalence of highly contaminated samples in low and high-throughput slaughterhouses. A maximum of 60 sample results were randomly selected for each slaughterhouse. Results were available from 17 low and 17 high-throughput slaughterhouses.
4.2.4.2 Enumeration of Campylobacter levels from low-throughput slaughterhouses
Campylobacter enumeration was provided for results sampled by the FSA from low-throughput slaughterhouses. This consisted of 501 samples – of which 161 (33%) did not have detectable Campylobacter levels. A histogram of the log-transformed values is shown in Figure 4 (top). Poultry with high levels of Campylobacter poses the most risk to consumers, as it is more likely that ingestion of undercooked material will deliver a dose large enough to cause infection.
A log-normal distribution is a good approximation for modelling the samples with detectable Campylobacter levels seen at this type of slaughterhouse, as indicated by the Bayesian Information Criterion (Figure 4 - bottom).
Figure 4: Histogram of Campylobacter levels in low-throughput slaughterhouses sampled by the FSA (top). The initial bar represents samples below the limit of detection (33% of samples). Distribution fit for Campylobacter contamination in low-throughput slaughterhouses (bottom). The best fit was the lognormal distribution. The samples below the limit of detection were removed prior to distribution fitting.
4.2.4.3 Campylobacter exceedances over 10-week period
When looking at individual slaughterhouses, more than half of low and high-throughput plants had compliant samples over the 10-week period in 2021.
The percentage of samples with high Campylobacter levels in individual low and high-throughput slaughterhouses are reported in Figure 4. Within the low-throughput category, 5 plants out of 17 exceed the 30% level, while in the high-throughput category, 3 out of 17 exceed this level.
There is a range of exceedances across the slaughterhouses, with 4 plants (S, AA, AC and AZ) reporting no samples above 1,000 CFU/g in the 10-week recording period whilst others having in more than 60% of their samples exceeding Campylobacter counts of 1,000 CFU/g (plants AK and AW). AK is a low-throughput plant and AW is a high-throughput plant.
Figure 5: Bar plots to show the percentage of all samples taken in low (top) and high-throughput (bottom) slaughterhouses that exceed 1,000 CFU/g Campylobacter over 10 weeks. The red line represents the 30% “accepted level of exceedance” according to current regulation.
4.2.4.4 Effect of slaughterhouses type - Halal and non-Halal
It was possible to identify certain slaughterhouses approved for religious slaughter which produce Halal or Kosher products, as they require a specific certification for this technique (Table 3). This was used to assess whether slaughterhouses of a certain type are more or less likely to have high levels of Campylobacter.
Table 3: The number and percentages of Halal, Kosher and non-Halal/Kosher slaughterhouses
Slaughterhouse type | Low-throughput slaughterhouses | High-throughput slaughterhouses |
---|---|---|
Halal | 9 (24%) | 9 (41%) |
Kosher | 1 (3%) | 0 (0%) |
Non-Halal/Kosher | 28 (74%) | 13 (59%) |
Total | 38 (100%) | 22 (100%) |
The type of slaughterhouse (Kosher/Halal and non-Kosher/Halal) was plotted in Figure 5, along with the percentage of samples that exceeded 1,000 CFU/g Campylobacter, to see if there is any clustering effect due to slaughterhouse type. The data used was all available data for slaughterhouses of both sizes – ranging from 10 weeks’ worth of sampling to 2 years.
Figure 6: Percentage of samples exceeding 1,000 CFU/g Campylobacter from UK slaughterhouses.
4.2.5 Estimate of contaminated poultry on UK market
It is possible, from the 10-week sampling data, to estimate of the total number of chickens originating from low and high-throughput slaughterhouses with high levels of Campylobacter per year.
The yearly throughput of the individual slaughterhouses is given in the Appendix – Section 8.2. All sampling data available from 2020 onwards was used to estimate the proportion of highly contaminated carcases from individual slaughterhouses, and multiplied with the yearly throughput to roughly estimate the contribution of each type of slaughterhouse to highly contaminated poultry on the market.
Low-throughput slaughterhouses processed 53,630,892 birds in 2021 compared with 965,216,124 birds in high-throughput slaughterhouses. From the data available on the proportion of highly contaminated carcases (Section 4.2.4.1) we estimate that low-throughput slaughterhouses contribute 12 million highly contaminated birds each year compared to 212 million birds from high-throughput slaughterhouses. Given that the proportion of highly contaminated carcases is roughly the same for low and high-throughput slaughterhouses, the volume of production is the main factor influencing the number of highly contaminated carcases on the market. This does not take into account potential variations due to risk mitigations applied, further processing, seasonal variation, etc. as data are not available (uncertainty).
4.2.6 Differences in the Campylobacter levels of poultry meat leaving low throughput and high-throughput abattoirs
As noted in the previous section, there was limited data to assess differences in the Campylobacter levels between poultry being processed by low- and high-throughput slaughterhouses during the individual stages of processing. Furthermore, although data were gathered on the levels of Campylobacter contamination after slaughter but before retail, no data were available on the actions that were taken as a result of exceeding the target threshold. In addition, the data that were collected at low-throughput abattoirs were collected over a limited period and may not be fully representative.
We could find no significant difference in the proportion of high levels of Campylobacter contamination between poultry produced in low- and high-throughput slaughterhouses at the point of testing. Given these limitations, we are not able to differentiate between two possible explanations for this result.
The first possible explanation is that the level of contamination on birds entering both types of plant is similar and that there are no differences in the effects of processing at the different plant sizes. The second possible explanation is that the levels of contamination are different upon entry, but that differences exist between the effects of processing at each types of plant, possibly including risk management activities in response to PHC results, and that the net effect of these two differences results in similar overall levels of contamination. The first scenario may be more likely as on-farm factors were found to be more important at influencing levels of Campylobacter spp. in neck skins than slaughterhouse factors (Hutchison et al., 2016). Therefore, it’s less likely that activities in a slaughterhouse have as much of an effect on Campylobacter levels as the on-farm factors.
Differentiating between these scenarios is not possible with the data that are currently available, but might become possible if additional evidence was gathered on the prevalence of Campylobacter in birds arriving at plants before slaughter or on the type and timing of interventions implemented at individual plants.
4.3 Retail module
4.3.1 Factors and controls affecting Campylobacter levels at retail
This module explores the effect of retail processing and storage on levels of Campylobacter in poultry.
Processing of poultry after slaughter can affect the levels of Campylobacter on the meat. Temperature is one such key factor, with refrigeration, and freezing especially, leading to a decrease in pathogen levels. Campylobacter spp. are highly sensitive to freezing temperatures, which is a well-known mitigation measure for chicken contaminated with the pathogen applied in countries such as Iceland (Tustin et al., 2011), Norway and Denmark (Nastasijevic et al., 2020). At refrigeration temperatures, a slower decrease in pathogen levels over time can be seen (ACMSF, 2019). Additional reduction can be seen in Campylobacter levels on chicken stored in oxygen-containing gas mixtures (Boysen, Knøchel and Rosenquist, 2007) – modified atmosphere packaged raw poultry at retail often includes oxygen.
It is extremely unlikely for Campylobacter to grow on processed raw poultry as its optimum growth range is around 40°C (Davis and DiRita, 2008).
4.3.2 Consumer supply chain
Once poultry has been slaughtered, it can be sold to retailers who supply raw chicken directly to consumers, or FBOs who cook the chicken before supplying it to consumers (either in ready meals or restaurants, or other catering), or it is frozen or exported.
Following slaughter, it was not possible to find information on who the poultry from low and high-throughput slaughterhouses is supplied to (uncertainty). The websites of low-throughput slaughterhouses suggest that they are suppliers of a premium product that is primarily used by local restaurants and butchers. However, there are no quantitative data available to support this statement, and it is unclear if this is true for all low-throughput slaughterhouses. This distinction could affect the risk – for example, chicken in ready-meals is less likely to cause campylobacteriosis due to being cooked at the manufacturer’s and cooked while sealed at the consumer’s, compared to raw chicken purchased by consumers. Freezing chicken will also decrease the risk as it significantly affects Campylobacter levels.
There may also be a difference in the level of processing carried out between low and high-throughput slaughterhouses, in terms of selling whole chickens compared to cuts such as breasts, thighs etc. The additional processing steps involved in selling cuts of meat could also affect the Campylobacter levels due to cross contamination. Again, insufficient information was available on processing practices of specific slaughterhouses to be able to quantify this risk (uncertainty).
4.3.3 Predicted decrease at retail
In this section, the focus is on Campylobacter sampling data from raw chicken sold at retailers, to understand how levels of the pathogen change at this step of the exposure pathway. Laboratory-based experiments are first used to predict the effects of refrigeration before comparing these with observed Campylobacter enumeration in retail chicken.
ComBase is a database and predictive microbiological model (Baranyi and Tamplin, 2004). Plots of ComBase data were generated to visualise the reduction in Campylobacter levels of raw chicken held at refrigeration temperatures within its shelf-life by retailers and UK consumers. A variety of temperatures were investigated – this is based on the fact that domestic refrigerators in the UK run at higher than the recommended temperature of between 1 and 5°C (Evans and Redmond, 2016) (Biglia et al., 2018).
ComBase data on Campylobacter levels in chicken broiler breast and chicken broth across different temperatures (4°C and 12°C) and (4°C, 5°C, 10°C, and 15°C) were used to estimate log10 CFU/g changes over time. Campylobacter levels in chicken broiler breast decreased by around 1 log10 CFU/g after 12 hours at 4°C (Figure 7). In comparison, Campylobacter levels tend to decrease by 1 log10 CFU/g after 6-hour storage at 12°C (Figure 7). Storage at 12°C effectively decreased Campylobacter presence on the chicken broiler breast by 2 log10 CFU/g after 15 hours.
Experiments in chicken broth produced more variable results (Figure 8). A similar trend of more Campylobacter death was observed as the temperature increased. Campylobacter levels also took longer to decrease by 1 log10 CFU/g in chicken broth - around 50 hours of storage at 4, 5, 10 and 12°C (Figure 8). Naturally, the decrease observed in chicken breast is taken to be more representative of the real-life scenario at retail.
Figure 7: Change in Campylobacter levels in chicken broiler breast at 4°C (A) and 12°C (B) over time. Data from ComBase (Baranyi and Tamplin, 2004). Different coloured lines refer to different samples
Figure 8: Change in Campylobacter levels in chicken broth at 4°C (A), 5°C (B), 10°C (C) and 15°C (D) over time. Data from ComBase (Baranyi and Tamplin, 2004). Different coloured lines refer to different samples.
4.3.4 Sampling results at large and small retailers
The FSA and major retailers carry out surveys of Campylobacter levels on chicken at retail. There were no data available on whether poultry from low-throughput slaughterhouses is more likely to be sold at large or small retailers (uncertainty). The difference in Campylobacter levels found at large and small retailers is discussed nevertheless, in case such information becomes available in future.
Surveys of whole chicken at retail found that a higher proportion of samples from small retailers had high levels of Campylobacter compared to those from large retailers, but did not find a cause of these differences (PHE, 2021). The difference could not be explained by remaining shelf-life, chicken weights, time of year sampled or type of chicken rearing (free-range, organic, etc).
Data from years 4, 5 and 6 of the “Microbiological survey of Campylobacter contamination in fresh whole UK-produced chilled chickens at retail sale” (FSA-funded project FS102121), was used to model the levels of Campylobacter found on Halal and non-Halal retail chickens at large retailers (year 4) and small retailers (years 4, 5 and 6). There were not enough data points for Kosher retailers to be included in this analysis.
The results, including the percentage that fall in the undetectable and high Campylobacter categories, are in Table 4 below. There are similar proportions of highly contaminated samples from Halal and non-Halal chicken. As noted by PHE, large retailers have a smaller proportion of highly contaminated chicken samples than small retailers (5% vs 12%). Large retailers also have more samples with undetectable levels of Campylobacter compared to small retailers (48% vs 39%).
Table 4: Number of results below the limit of detection, or >1,000 CFU/g Campylobacter in large and small retailers, broken down into Halal and non-Halal categories
Retailer | Below limit of detectoin | >1,000 CFU/g Campylobacter | Number of total results |
---|---|---|---|
Small, Halal | 275 (43%) | 84 (13%) | 641 |
Small, Non-Halal | 1225 (38%) | 383 (12%) | 3200 |
Small (all) | 1500 (39%) | 467 (12%) | 3841 |
Large, Halal | 8 (35%) | 46 (5%) | 932 |
Large, Non-Halal | 447 (48%) | 46 (5%) | 932 |
Large (all) | 455 (48%) | 50 (5%) | 955 |
Halal (all) | 283 (43%) | 88 (13%) | 664 |
Non-Halal (all) | 1672 (40%) | 429 (10%) | 4132 |
Figure 8 and Figure 9 show the distribution of the levels of Campylobacter in raw whole chicken from large, and small retailers, and by Halal and non-Halal categories. A lognormal distribution was chosen as best fitting (compared to uniform, normal and Weibull fits), given the AIC/BIC scores. Due to the heavy skew of the raw data, it was log-transformed before distribution fitting.
Figure 9: Campylobacter levels in whole chicken from large and small retailers. The best fitting distribution for the data is the lognormal. Samples with undetectable Campylobacter levels are not included.
Figure 10: Campylobacter levels at retail in Halal and non-Halal whole chicken. The best fitting distribution for the data is the lognormal. Samples with undetectable Campylobacter levels are not included.
Of the chicken that had detectable levels of Campylobacter, it was noticeable that retail chicken had lower levels compared to those measured after slaughter (Figure 10). This is presumably due to the influence of cold storage, as predicted by the ComBase data presented in the previous section (Section 4.3.3). The percentage of samples that did not have detectable levels of Campylobacter also increased at retail, from 33% (low-throughput slaughterhouses) to 39% (small retailers) and 48% (large retailers).
Figure 11: Fitted log normal distributions for Campylobacter levels sampled at low-throughput slaughterhouses, small retailers and large retailers. Chicken sampled at retail level had lower levels of contamination than at the slaughterhouse.
4.3.5 Differences in the Campylobacter levels of products at retail originating from low-throughput and high-throughput abattoirs
Campylobacter levels in chicken decrease following slaughter, as measured at retail and evidenced by experimental studies, likely due to the pathogen’s sensitivity to refrigeration temperatures.
The proportion of highly contaminated samples at retail is similar in Halal and non-Halal chicken. Large retailers had a smaller proportion of highly contaminated chicken samples (5%) compared to small retailers (12%).
No information was found on the proportions of poultry meat from low- and high-throughput slaughterhouses used in different sectors (for example, catering, large and small retailers, ready-meals etc).
Therefore, although the available data indicate a difference in the proportion of chickens with high levels of Campylobacter contamination sold at major versus non-major retailers, in the absence of information on the relative volumes of chicken sold through each of these types of retailer that originated from low-throughput versus high-throughput abattoirs, it was not possible to assess whether a difference in risk exists.
4.4 Consumer module
4.4.1 Factors affecting Campylobacter levels due to consumer behaviour
Poultry with high levels of Campylobacter will pose the highest risk of campylobacteriosis for consumers. Thorough cooking will eliminate the pathogen, however, cross-contamination of kitchen surfaces and ready-to-eat foods may also cause illness. Certain behaviours such as freezing poultry and washing raw chicken will affect the risk.
While data for the UK were not available, a quantitative risk assessment for antimicrobial resistant Salmonella in poultry estimated that 50% of Canadian consumers freeze their chicken (Collineau et al., 2020). A UK study found that, 67% of consumers were observed to wash their hands with soap immediately after handling raw chicken (Didier et al., 2021).
According to a behavioural study in the US, 45% of participants washed raw chicken (a potential source of cross-contamination), and in 17% of cases, the internal temperature of the chicken dish was less than 70°C. Oven cooking was found to result in the lowest proportion of undercooking of chicken, compared to grilling, frying and boiling on top of the stove (Bruhn, 2014).
4.4.2 Differences in Campylobacter levels at consumption
Chicken is the foremost cause of campylobacteriosis in the UK (Oxford University, 2021). It should be noted that these cases of illness linked with chicken are not necessarily direct cases through consumption of chicken, and could be due to cross-contamination or other sources of exposure. In this report, we assume that all cases of campylobacteriosis linked with chicken are caused by chickens that are slaughtered in the UK, not including imports. We also do not have information on whether chicken from low-throughput slaughterhouses reaches a different subpopulation of consumers, who are likely to treat it differently (uncertainty).
To determine the number of cases that can be directly attributed to chicken, we have used the recently completed surveillance and source attribution research (Oxford University, 2021). This identified that 90% of Campylobacter cases are caused by C. jejuni, with 70% able to be linked to chicken as the source. The remaining 10% of Campylobacter cases are predominantly caused by C. coli, around 50% of which are associated with chicken.
Using this, and the total number of campylobacteriosis cases from the 2018 burden of Foodborne Disease (Holland and Mahmoudzadeh, 2020), we can estimate the number of Campylobacter infections linked to chicken as the source (Table 5). This was done by estimating the total number of Campylobacter cases linked to chicken from the frequency of C. jejuni and C. coli attribution, and then attributing the number of campylobacteriosis cases to low and high-throughput slaughterhouses by their proportional market share.
This estimate assumes that all cases of campylobacteriosis linked with chicken are caused by chickens slaughtered in the UK, as we don’t have sufficient evidence on the rates of contamination of fresh imported chicken or the levels in frozen chicken when it reaches the consumer.
Table 5: The total number of Campylobacter cases in 2018, and an estimate of the number that can be attributed to chicken.
Cases | Median number of cases | Lower 95% CI | Upper 95% CI |
---|---|---|---|
2018 Campylobacter cases | 299,392 | 127,128 | 571,332 |
C. jejuni cases attributable to chicken | 188,616 | 80,090 | 35,993 |
Cases from other species of Campylobacter attributable to chicken |
14,969 | 6,356 | 28,566 |
Total Campylobacter cases attributable to chicken | 203,586 | 86,447 | 388,505 |
Campylobacter cases attributable to low-throughput slaughterhouses | 10,771 | 4,573 | 20,554 |
Campylobacter cases attributable to high-throughput slaughterhouses | 192,815 | 81.873 | 367,951 |
4.4.3 Differences in Campylobacter levels of products in the home
Because we were unable to find any information on differences in the products manufactured with chicken from low- versus high-throughput abattoirs, or in the volume of chicken products sold through different types of retail outlets, it was not possible to assess whether consumer behaviours will differentially affect the probability of exposure to Campylobacter via poultry produced in low and high-throughput slaughterhouses. Assuming all else being equal, the yearly throughput has the only impact on risk at a population level.
This risk assessment was commissioned to understand the differences in risk from Campylobacter contamination/cross-contamination in slaughterhouses with a low-throughput compared to slaughterhouses with a large throughput and to determine the subsequent risk to human health and the UK population.
The Campylobacter Process Hygiene Criteria were introduced based on the results of a quantitative risk assessment model (Vose Consulting (US) LLC, 2011) that ranked several interventions based on their efficacy for Campylobacter reduction (Retained Commission Regulation (EU) 2017/1495). The EFSA opinion stated that “Theoretically, a public health risk reduction > 50% or > 90% at the EU level could be achieved if all batches that are sold as fresh meat would comply with microbiological criteria with a critical limit of 1000 or 500 CFU/gram of neck and breast skin, respectively” (EFSA Panel on Biological Hazards (BIOHAZ), 2011). Other control options throughout the poultry meat chain are given in Table 2 in Nastasijevic et al., 2020.
The risk pathway for Campylobacter in poultry can be broken down into different stages of the farm to fork process: production (farm), processing (slaughterhouse), post-processing (retail), and home preparation (consumer), where the pathogen levels can increase/decrease.
With regards to the farm module, data from slaughterhouses in relation to different types of poultry processed in slaughterhouses such as conventional, organic, free range, type of cages etc. were limited (uncertainty). Therefore, it was not possible to assess this in this risk assessment.
With regards to Campylobacter levels in slaughterhouses, the literature suggests defeathering and evisceration processes increase the risk of contamination. Controls usually implemented during poultry slaughter to reduce carcase contamination include cleaning and disinfecting equipment such as evisceration machines in addition to the processes of scalding, stream treatment and chilling.
Campylobacter samples were available from 17 low-throughput and 17 high-throughput abattoirs over a 10-week period. Overall, there was no significant difference in the number of highly contaminated samples from low (22%) and high (22%) throughput slaughterhouses after standardisation for number of samples. Enumeration data were available for some low-throughput plants, but high-throughput plants only provide the number of samples above and below 1,000 CFU/g. No data were provided by 26 slaughterhouses.
In terms of individual slaughterhouses and their Campylobacter levels over a 10-week period, the low and high-throughput plants performed in similar ways. Low-throughput slaughterhouses had 5 plants out of 17 with high exceedance levels according to legislation while high-throughput plants had 3 out of 17 exceeding this level. One low-throughput and one high-throughput slaughterhouse had slightly above 60% of their samples exceeding 1,000 CFU/g – the legislation states that this should be no more than 30% or 15 out of 50 samples.
There was also no significant difference between proportions of samples with high levels of Campylobacter from slaughterhouses classed as Halal (30%) and non-Halal (35%) plants.
Most importantly, we were not able to determine whether an exceedance results in mitigative action and specifically what action (uncertainty), whether on-farm or at the abattoir. Therefore, we could not estimate the likely effect of mitigations on Campylobacter levels (uncertainty).
Information was not readily available on the onward distribution of chicken from low and high-throughput slaughterhouses (uncertainty). This distinction could affect the risk – for example, chicken in ready-meals is less likely to cause campylobacteriosis due to being cooked at the manufacturer’s and cooked while sealed at the consumer’s, compared to raw chicken purchased by consumers.
Other surveys of whole chicken at retail found that there was a difference in the proportion of samples with high levels of Campylobacter from small and large retailers but did not find a cause of these differences. However, we were unable to obtain information on the proportion of chicken sold at small and large retailers originating from low-throughput and high-throughput abattoirs. In general, the cold storage chain for fresh retail chicken results in a decrease in Campylobacter levels, estimated to be at least 1 log10 CFU/g.
Whole chicken at small retailers is significantly more likely to have high levels of Campylobacter contamination, compared to that sampled at large retailers. However, we do not have information on whether small retailers are more likely to be supplied by low or high-throughput slaughterhouses (uncertainty).
This risk assessment has only considered chicken slaughtered in the UK as imported chicken is out of scope.
Consumers may be exposed to Campylobacter directly through poultry but also through cross-contamination from other sources of exposure for example, from cooking surfaces. Campylobacter are able to persist both in the environment and in contaminated foods, despite being highly sensitive to atmospheric oxygen concentrations. Washing raw chicken is a key contributor to cross-contamination in domestic settings. Heat treatment which results in a temperature of 70°C for 2 minutes (or equivalent) throughout the part of the product that is slowest to heat would be sufficient to eliminate Campylobacter spp. from the product.
Using data on yearly campylobacteriosis cases (Holland and Mahmoudzadeh, 2020) and the proportion of campylobacteriosis cases attributable to chicken (Oxford University, 2021), we have estimated that 204,000 Campylobacter cases come from chicken, with 11,000 attributed to low-throughput slaughterhouses and 193,000 attributed to high-throughput slaughterhouses.
This strategic risk assessment concluded that given that the proportion of highly contaminated chickens was not significantly different between low and high-throughput slaughterhouses, and under the assumption that the downstream of the slaughterhouses, everything was the same, there is no difference in risk per portion of chicken from each type of slaughterhouse.
One important point to note is that because the proportion of slaughterhouses with high levels of exceedance was not significantly different, the throughput is the main influencing factor when determining the risk to human health and the UK population. We estimated that a total of 9 million highly contaminated birds from small slaughterhouses went to retail each year compared to 168 million from large slaughterhouses. Therefore, Campylobacter cases are much more likely to be linked to chicken produced in large slaughterhouses.
5.1 Risk estimate
Based on suggestions in the ACMSF work on multidimensional representation of risks (ACMSF, 2020), the frequency of occurrence of campylobacteriosis in the UK population from chicken produced in low-throughput slaughterhouses is medium and for high-throughput slaughterhouses is high (see Table 6 for interpretation of the qualitative categories). The uncertainty associated with this probability is medium (see Table 7 for interpretation of the qualitative categories). The risk assessment concludes that the severity of Campylobacter infection is low (see Table 8 for interpretation of the qualitative categories) with low uncertainty.
On a per-portion basis, the frequency of campylobacteriosis from chicken produced in low-throughput slaughterhouses is the same as for high-throughput slaughterhouses.
A number of uncertainties and evidence gaps were identified during this risk assessment. We had no information as to the method in which the poultry were reared prior to arriving at the slaughterhouse and are aware that evidence suggests that this can directly affect Campylobacter levels at slaughter. There was no information available as to the onward processing of meat handled by slaughterhouses, we therefore assumed that low and high-throughput slaughterhouses contribute equally to retail and hospitality etc.
In order to reduce the Campylobacter load on poultry, interventions at the farm and slaughterhouse level in the UK could be assessed for their efficacy to find the methods with the biggest impact. A simpler study could involve gathering information from slaughterhouses with consistently low levels of Campylobacter and sharing their methods as good practice.
Table 6: definition of qualitative categories for probability of occurrence
Frequency | Interpretation |
---|---|
Negligible | So rare that it does not merit to be considered |
Very low | Very rare but cannot be excluded |
Low | Rare but does occur |
Medium | Occurs regularly |
High | Occurs very often |
Very high | Events occur almost certainly |
Table 7: definitions of qualitative categories for expressing uncertainty
Uncertainty category | Interpretation |
---|---|
Low | There are solid and complete data available; strong evidence is provided in multiple references; authors report similar conclusions |
Medium | There are some but no complete data available; evidence is provided in small number of references; authors report conclusions that vary from one another |
High | There are scarce or no data; evidence is not provided in references but rather in unpublished reports or based on observations, or personal communication; authors report conclusions that vary considerably between them. |
Table 8: definitions of qualitative categories for severity of consequence
Severity category | Interpretation |
---|---|
Negligible | No effects, or so mild they do not merit to be considered |
Low | Mild illness: not usually life-threatening, usually no sequelae, normally of short duration, symptoms are self-limiting (for example, transient diarrhoea) |
Medium | Moderate illness: incapacitating but not usually life-threatening, sequelae rare, moderate duration (for example, diarrhoea requiring hospitalisation) |
High | Severe illness: causing life-threatening or substantial sequelae or illness of long duration (for example, chronic hepatitis) |
5.2 Sampling effect on risk
Part of the scope of this risk assessment is to examine how sampling frequency in low-throughput abattoirs affects the risk, in particular, these four sampling scenarios:
a) Sampling on a weekly basis as per current regulation
b) Not sampling/testing to ascertain compliance with the PHC
c) Sampling every other week
d) Sampling at a rate of once every 4 weeks
Currently, some low-throughput abattoirs submit PHC samples to the FSA and some do not, or do so infrequently.
Regarding the effect of the different proposed sampling scenarios on risk: sampling, in itself, does not directly impact public health unless it triggers control measures that are effective at reducing the frequency or level of Campylobacter contamination. After exceedance of the target threshold there are recommendations for voluntary actions that, in certain combinations, have been found effective, although that effectiveness varies depending on plant-specific factors and their interaction. Given the data gaps that currently exist concerning the probability of voluntary action in the event of exceedance, the types of actions taken either at slaughter or on-farm, and their effectiveness, it is not possible to estimate the reduction in risk such voluntary measures currently produce.
If no testing is undertaken at low-throughput abattoirs the probability of taking voluntary actions as a result of exceedance is automatically zero, although actions may be taken for other reasons. Some low-throughout abattoirs are not testing, therefore the opportunity is lost for any additional measures to be taken. Removing a sampling requirement that is not currently adhered to will not change the risk to public health. Lack of enforcement of mitigations upon failing to comply with the 30% exceedance rate would also mean there is no change in the level of risk.
Taking the same number of samples over a longer period of time (options c and d) would still have some value, as they will still enable identification of high Campylobacter contamination. However, as shown below it is likely to result in substantial differences in the classification of the plants at given points in time, both suggesting that no issue exists when sampling at a normal frequency would suggest an issue exists, as well as the opposite, and delaying the identification of issues.
It is possible to illustrate what results a reduced sampling scheme would have produced, using sampling data from plants that have failed the PHC criteria at some point (Figure 12). For instance, if half the weeks of sampling were to be removed from the original dataset, it would not have been possible to detect 4/14 (29%) of plants that had initially failed to meet the PHC target at some point (second column in Figure 13, Figure 14, Figure 15, Figure 16) at all. If three quarters of the weeks of sampling are removed from the original dataset, it would not have been possible to detect 6/14 (43%) of plants that had initially failed to meet the PHC target at some point (third column in Figure 13, Figure 14, Figure 15, Figure 16) at all. This also assumes that there would be no effect of sampling frequency on behaviours in the plant, for example, that there is no possibility that awareness of less frequent sampling might lead to reduced standards during processing.
It is still possible to detect slaughterhouses that consistently fail, under reduced sampling, such as plants Y, AK, AL, and AW, . It is also possible for a slaughterhouse to perform worse (for example, have a high proportion of samples over 1,000 CFU/g) with a reduced sampling scheme – see plant AK in Figure 13.
Since the rolling average calculation will only be made once every four weeks rather than every week, it would also take longer for issues of high Campylobacter levels to be detected.
In conclusion, because of a lack of consistency in the application of sampling requirements in low-throughput slaughterhouses and a lack of information on the probability and nature of corrective actions taken in the event of an exceedance, it is not possible to differentiate the effect on per-portion risk of changes to current sampling requirements. However, due to the small proportion of total poultry meat consumed in the UK that is produced at low-throughput slaughterhouses, changes to the official requirements for sampling at low-throughput slaughterhouses are unlikely to result in a large change in the total number of cases of campylobacteriosis in the UK population.
Figure 12: Slaughterhouses that at some point failed to meet the PHC target during a 10-week rolling average over 2020-2022. The x axis states the first week of the rolling window, with week 1 of 2020 counting as week 1, week 1 of 2021 counting as week 53 and so on.
Figure 13: Modelling reduced sampling in slaughterhouses. The first column shows the proportion of samples with high levels of Campylobacter at different slaughterhouses that failed the PHC criteria at some point. The effect of reducing the number of samples collected by half is shown in the second column and three-quarters reduction in the third column. The x axis states the first week of the rolling window, with week 1 of 2020 counting as week 1, week 1 of 2021 counting as week 53 and so on.
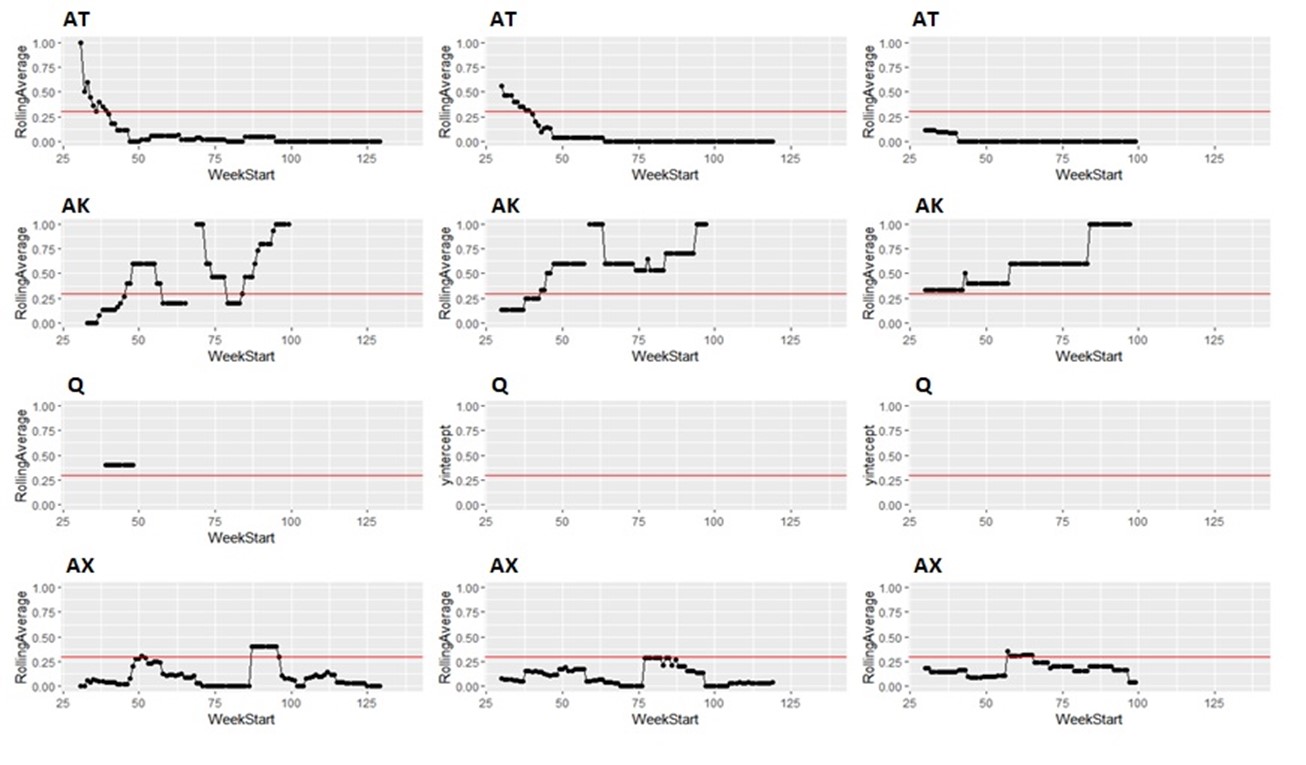
Figure 14: Modelling reduced sampling in slaughterhouses. The first column shows the proportion of samples with high levels of Campylobacter at different slaughterhouses that failed the PHC criteria at some point. The effect of reducing the number of samples collected by half is shown in the second column and three-quarters reduction in the third column. The x axis states the first week of the rolling window, with week 1 of 2020 counting as week 1, week 1 of 2021 counting as week 53 and so on.
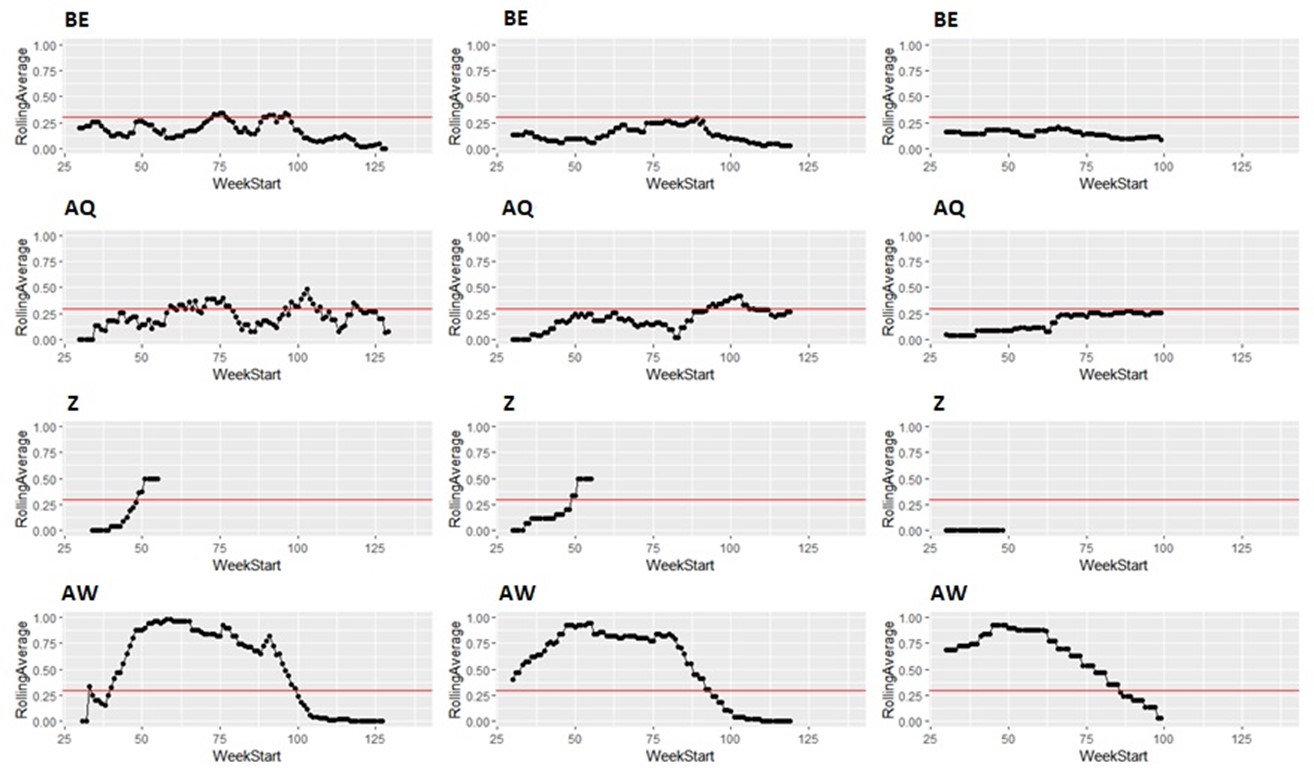
Figure 15: Modelling reduced sampling in slaughterhouses. The first column shows the proportion of samples with high levels of Campylobacter at different slaughterhouses that failed the PHC criteria at some point. The effect of reducing the number of samples collected by half is shown in the second column and three-quarters reduction in the third column. The x axis states the first week of the rolling window, with week 1 of 2020 counting as week 1, week 1 of 2021 counting as week 53 and so on.
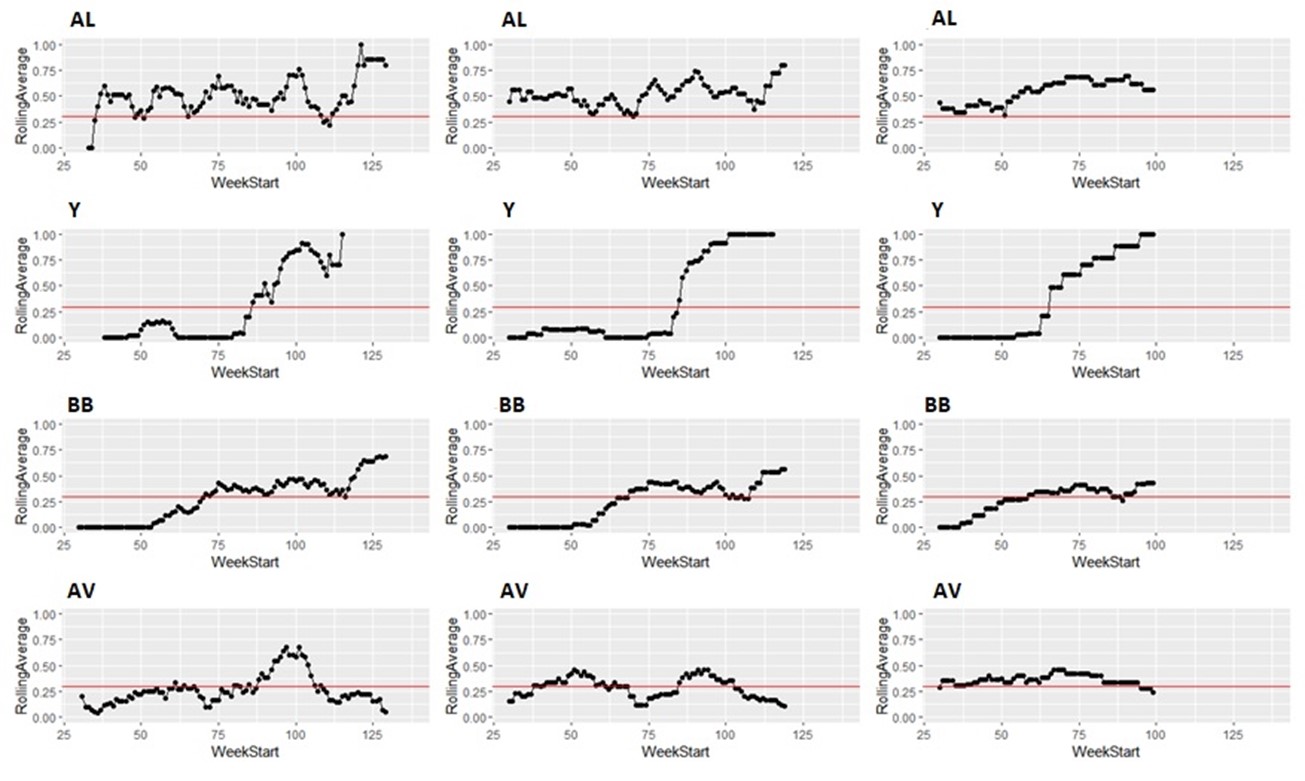
Figure 16: Modelling reduced sampling in slaughterhouses. The first column shows the proportion of samples with high levels of Campylobacter at different slaughterhouses that failed the PHC criteria at some point. The effect of reducing the number of samples collected by half is shown in the second column and three-quarters reduction in the third column. The x axis states the first week of the rolling window, with week 1 of 2020 counting as week 1, week 1 of 2021 counting as week 53 and so on.
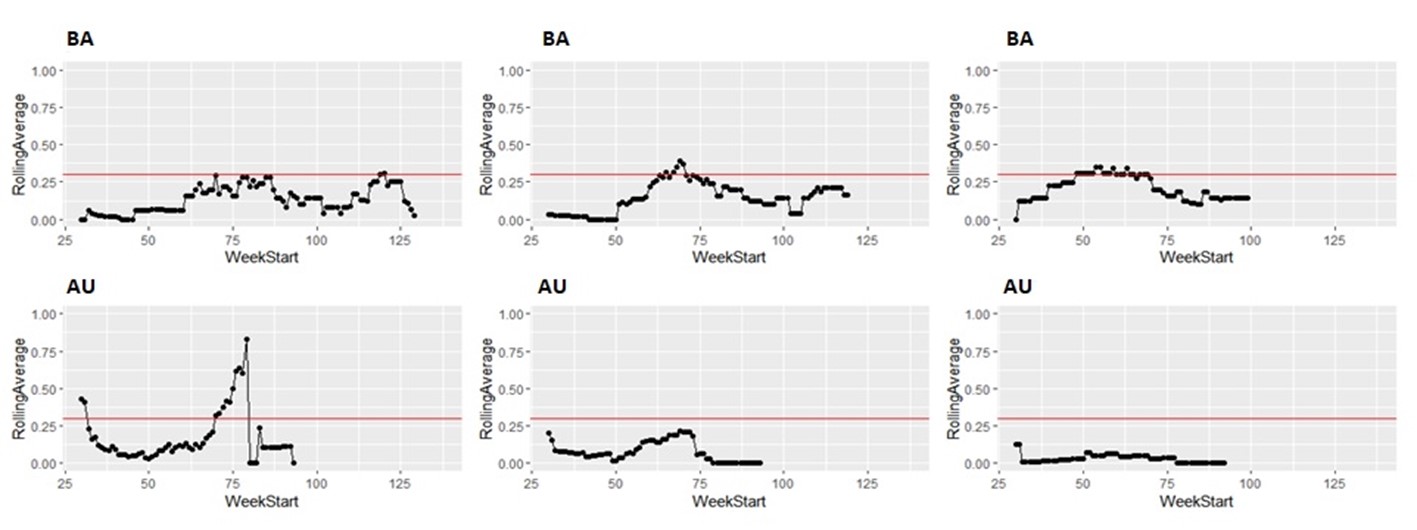
5.3 Uncertainties and assumptions
The following are key uncertainties or data gaps in order of importance:
- differences in onward processing and supply of carcases provided by low and high-throughput slaughterhouses to other businesses
- differences in the rearing of poultry provided to low and high-throughput slaughterhouses
- the distribution of Campylobacter enumeration levels in high-throughput slaughterhouses
- the amount of poultry imported into the UK for UK consumption and exported by low and high-throughput slaughterhouses
- Campylobacter levels at the 5 high and 21 low-throughput slaughterhouses where no results were available
The following are assumptions made in this report:
- there is no difference in the poultry that is supplied to low- and high-throughput slaughterhouses
- carcases from low and high-throughput slaughterhouses are provided in similar proportions to retail, caterers, exporters etc.
- the distribution of detectable Campylobacter levels in high-throughput slaughterhouses is similar to that of low-throughput slaughterhouses
- there is no difference in the population of consumers eating chicken from high and low-throughput slaughterhouses
- that the proportion of the total domestic consumption of poultry meat originating from low-throughput slaughterhouses does not change
Data gaps
This report focuses predominantly on chicken as being most consumed – but the abattoirs in question also process turkey broilers.
5.4 Recommendations for future research
The most important evidence gap for reducing uncertainty in this assessment is gaining a better understanding of the probability that action is taken, and the nature of the action(s) taken, in response to exceedance, as well as their effectiveness. This will likely be achieved by a survey of the FBOs, official veterinarians and meat hygiene inspectors working at the premises.
It would also be useful to understand the differences in prevalence and levels of Campylobacter on poultry entering the slaughterhouse. This could be potentially achieved by combining information on the types of farms supplying each category of slaughterhouses, the farm management practices in use on each and information on the levels of Campylobacter on farm, or by additional microbiological sampling of chickens at entry into the slaughterhouse.
It would be useful to understand what products the outputs of each plant type are used for for example, chicken portions, whole chickens, retail, catering, etc. as well as how effectively each of these products are cooked; for example, meat thermometers are more likely to be used during commercial cooking steps. This would be achieved with an FBO survey.
- ACMSF (2019) Third report on Campylobacter. (Accessed: 16 September 2022).
- Allen, V.M. et al. (2007) ‘Campylobacter spp. contamination of chicken carcasses during processing in relation to flock colonisation’, International Journal of Food Microbiology, 113(1), pp. 54–61. Available at: https://doi.org/10.1016/j.ijfoodmicro.2006.07.011.
- Allen, V.M. et al. (2008) ‘Sources and Spread of Thermophilic Campylobacter spp. during Partial Depopulation of Broiler Chicken Flocks’, Journal of Food Protection, 71(2), pp. 264–270. Available at: https://doi.org/10.4315/0362-028X-71.2.264.
- Ansari-Lari, M. et al. (2011) ‘Prevalence and risk factors associated with campylobacter infections in broiler flocks in Shiraz, southern Iran’, International Journal of Food Microbiology, 144(3), pp. 475–479. Available at: https://doi.org/10.1016/j.ijfoodmicro.2010.11.003.
- Antic, D. (2022) ‘Personal communication’.
- Ausvet Europe et al. (2022) Modelling framework to quantify the risk of AMR exposure via food products - example of chicken and lettuce. Food Standards Agency. Available at: https://doi.org/10.46756/sci.fsa.qum110.
- Baranyi, J. and Tamplin, M.L. (2004) ‘ComBase: A Common Database on Microbial Responses to Food Environments’, Journal of Food Protection, 67(9), pp. 1967–1971. Available at: https://doi.org/10.4315/0362-028X-67.9.1967.
- Battersby, T., Whyte, P. and Bolton, D. (2016) ‘Protecting broilers against Campylobacter infection by preventing direct contact between farm staff and broilers’, Food Control, 69, pp. 346–351. Available at: https://doi.org/10.1016/j.foodcont.2016.04.053.
- Biglia, A. et al. (2018) ‘Temperature and energy performance of domestic cold appliances in households in England’, International Journal of Refrigeration, 87, pp. 172–184. Available at: https://doi.org/10.1016/j.ijrefrig.2017.10.022.
- Borck Høg, B. et al. (2016) ‘Farm specific risk factors for Campylobacter colonisation in Danish and Norwegian broilers’, Preventive Veterinary Medicine, 130, pp. 137–145. Available at: https://doi.org/10.1016/j.prevetmed.2016.04.002.
- Boysen, L., Knøchel, S. and Rosenquist, H. (2007) ‘Survival of Campylobacter jejuni in different gas mixtures’, FEMS Microbiology Letters, 266(2), pp. 152–157. Available at: https://doi.org/10.1111/j.1574-6968.2006.00525.x.
- Bruhn, C.M. (2014) ‘Chicken Preparation in the Home: An Observational Study’, Food Protection Trends, 34(5), pp. 318–330.
- Chowdhury, S. et al. (2012) ‘Risk factors for Campylobacter infection in Danish broiler chickens’, Poultry Science, 91(10), pp. 2701–2709. Available at: https://doi.org/10.3382/ps.2012-02412.
- Collineau, L. et al. (2020) ‘A farm-to-fork quantitative risk assessment model for Salmonella Heidelberg resistant to third-generation cephalosporins in broiler chickens in Canada’, International Journal of Food Microbiology, 330, p. 108559. Available at: https://doi.org/10.1016/j.ijfoodmicro.2020.108559.
- Corry, J. et al. (2017) ‘Reducing campylobacter cross-contamination during poultry processing’, p. 159.
- Corry, J.E.L. et al. (2007) ‘Surface pasteurisation of chicken carcasses using hot water’, Journal of Food Engineering, 79(3), pp. 913–919. Available at: https://doi.org/10.1016/j.jfoodeng.2006.03.018.
- Davis, L. and DiRita, V. (2008) ‘Growth and laboratory maintenance of Campylobacter jejuni’, Current Protocols in Microbiology, Chapter 8, p. Unit 8A.1.1-8A.1.7. Available at: https://doi.org/10.1002/9780471729259.mc08a01s10.
- Didier, P. et al. (2021) ‘Washing hands and risk of cross-contamination during chicken preparation among domestic practitioners in five European countries’, Food Control, 127, p. 108062. Available at: https://doi.org/10.1016/j.foodcont.2021.108062.
- Dogan, O.B. et al. (2019) ‘A quantitative microbial risk assessment model of Campylobacter in broiler chickens: Evaluating processing interventions’, Food Control, 100, pp. 97–110. Available at: https://doi.org/10.1016/j.foodcont.2019.01.003.
- EFSA Panel on Biological Hazards (BIOHAZ) (2011) ‘Scientific Opinion on Campylobacter in broiler meat production: control options and performance objectives and/or targets at different stages of the food chain’, EFSA Journal, 9(4), p. 2105. Available at: https://doi.org/10.2903/j.efsa.2011.2105.
- EFSA Panel on Biological Hazards (BIOHAZ) et al. (2020) ‘Update and review of control options for Campylobacter in broilers at primary production’, EFSA journal. European Food Safety Authority, 18(4), p. e06090. Available at: https://doi.org/10.2903/j.efsa.2020.6090.
- Ellis-Iversen, J. et al. (2009) ‘Risk factors for Campylobacter colonisation during rearing of broiler flocks in Great Britain’, Preventive Veterinary Medicine, 89(3–4), pp. 178–184. Available at: https://doi.org/10.1016/j.prevetmed.2009.02.004.
- EVANS, E.W. and REDMOND, E.C. (2016) ‘Time-Temperature Profiling of United Kingdom Consumers’ Domestic Refrigerators’, Journal of Food Protection, 79(12), pp. 2119–2127. Available at: https://doi.org/10.4315/0362-028X.JFP-16-270.
- FSA (2019a) Campylobacter Reduction Programme: Update, Food Standards Agency. (Accessed: 17 November 2022).
- FSA (2019b) Meat Industry Guide - Chapter 13.
- FSA (2022) ‘Personal communication’.
- Georgiev, M., Beauvais, W. and Guitian, J. (2017) ‘Effect of enhanced biosecurity and selected on-farm factors on Campylobacter colonization of chicken broilers’, Epidemiology and Infection, 145(3), pp. 553–567. Available at: https://doi.org/10.1017/S095026881600251X.
- Guirin, G.F. et al. (2020) ‘Prevalence of Campylobacter jejuni and Campylobacter coli from broilers at conventional and kosher abattoirs and retail stores’, Revista Argentina de Microbiología, 52(3), pp. 217–220. Available at: https://doi.org/10.1016/j.ram.2019.07.002.
- Hastings, R. et al. (2011) ‘Campylobacter genotypes from poultry transportation crates indicate a source of contamination and transmission’, Journal of Applied Microbiology, 110(1), pp. 266–276. Available at: https://doi.org/10.1111/j.1365-2672.2010.04883.x.
- Holland, D. et al. (2020) ‘Estimating deaths from foodborne disease in the UK for 11 key pathogens’, BMJ open gastroenterology, 7(1), p. e000377. Available at: https://doi.org/10.1136/bmjgast-2020-000377.
- Holland, D. and Mahmoudzadeh, N. (2020) Foodborne Disease Estimates for the United Kingdom in 2018. Food Standards Agency. Available at: https://doi.org/10.46756/sci.fsa.squ824.
- Huneau-Salaün, A. et al. (2007) ‘Risk factors for Campylobacter spp. colonization in French free-range broiler-chicken flocks at the end of the indoor rearing period’, Preventive Veterinary Medicine, 80(1), pp. 34–48. Available at: https://doi.org/10.1016/j.prevetmed.2007.02.001.
- Hutchison, M. et al. (2016) Monitoring of campylobacters in UK poultry slaughter batches and carcasses and the collection of information from primary production and processing for risk factor elucidation.(PDF)
- IPSOS Mori (2016) Trialling a modernised poultry inspection system in UK slaughterhouses.
- James, C. et al. (2007) ‘Decontamination of poultry carcasses using steam or hot water in combination with rapid cooling, chilling or freezing of carcass surfaces’, International Journal of Food Microbiology, 114(2), pp. 195–203. Available at: https://doi.org/10.1016/j.ijfoodmicro.2006.09.019.
- Jorgensen, F. et al. (2011) ‘Influence of Season and Geography on Campylobacter jejuni and C. coli Subtypes in Housed Broiler Flocks Reared in Great Britain’, Applied and Environmental Microbiology, 77(11), pp. 3741–3748. Available at: https://doi.org/10.1128/AEM.02444-10.
- Jorgensen, F. et al. (2019) ‘A microbiological survey of Campylobacter contamination in fresh whole UK-produced chilled chickens at retail sale’, p. 37. https://doi.org/10.46756/sci.fsa.xxz973
- Kaakoush, N.O. et al. (2015) ‘Global Epidemiology of Campylobacter Infection’, Clinical Microbiology Reviews, 28(3), pp. 687–720. Available at: https://doi.org/10.1128/CMR.00006-15.
- Kaakoush, N.O., Mitchell, H.M. and Man, S.M. (2015) ‘Chapter 67 - Campylobacter’, in Y.-W. Tang et al. (eds) Molecular Medical Microbiology (Second Edition). Boston: Academic Press, pp. 1187–1236. Available at: https://doi.org/10.1016/B978-0-12-397169-2.00067-6.
- McDowell, S.W.J. et al. (2008) ‘Campylobacter spp. in conventional broiler flocks in Northern Ireland: epidemiology and risk factors’, Preventive Veterinary Medicine, 84(3–4), pp. 261–276. Available at: https://doi.org/10.1016/j.prevetmed.2007.12.010.
- Nastasijevic, I. et al. (2020) ‘The European Union control strategy for Campylobacter spp. in the broiler meat chain’, Journal of Food Safety, 40(5), p. e12819. Available at: https://doi.org/10.1111/jfs.12819.
- Näther, G. et al. (2009) ‘Analysis of risk factors for Campylobacter species infection in broiler flocks’, Poultry Science, 88(6), pp. 1299–1305. Available at: https://doi.org/10.3382/ps.2008-00389.
- O’Brien, S.J. et al. (2016) ‘Modelling study to estimate the health burden of foodborne diseases: cases, general practice consultations and hospitalisations in the UK, 2009’, BMJ Open, 6(9), p. e011119. Available at: https://doi.org/10.1136/bmjopen-2016-011119.
- Oxford University (2021) ‘Enhanced molecular-based surveillance and source attribution of campylobacter infections in the UK’, Food Standards Agency [Preprint]. Available at: https://doi.org/10.46756/sci.fsa.ksj135.
- PHE (2021) ‘A microbiological survey of campylobacter contamination in fresh whole UK-produced chilled chickens at retail sale (Y6)’, Food Standards Agency [Preprint]. Available at: https://doi.org/10.46756/sci.fsa.xxz973.
- Rasschaert, G. et al. (2020) ‘Campylobacter contamination of broilers: the role of transport and slaughterhouse’, International Journal of Food Microbiology, 322, p. 108564. Available at: https://doi.org/10.1016/j.ijfoodmicro.2020.108564.
- Refrégier-Petton, J. et al. (2001) ‘Risk factors for Campylobacter spp. contamination in French broiler-chicken flocks at the end of the rearing period’, Preventive Veterinary Medicine, 50(1–2), pp. 89–100. Available at: https://doi.org/10.1016/s0167-5877(01)00220-3.
- Robinson, D.A. (1981) ‘Infective dose of Campylobacter jejuni in milk.’, BMJ, 282(6276), pp. 1584–1584. Available at: https://doi.org/10.1136/bmj.282.6276.1584.
- Rosenquist, H. et al. (2006) ‘The effect of slaughter operations on the contamination of chicken carcasses with thermotolerant Campylobacter’, International Journal of Food Microbiology, 108(2), pp. 226–232. Available at: https://doi.org/10.1016/j.ijfoodmicro.2005.12.007.
- Tam, C.C. et al. (2012) ‘Longitudinal study of infectious intestinal disease in the UK (IID2 study): incidence in the community and presenting to general practice’, Gut, 61(1), pp. 69–77. Available at: https://doi.org/10.1136/gut.2011.238386.
- Teunis, P.F.M. et al. (2018) ‘Acute illness from Campylobacter jejuni may require high doses while infection occurs at low doses’, Epidemics, 24, pp. 1–20. Available at: https://doi.org/10.1016/j.epidem.2018.02.001.
- Torralbo, A. et al. (2014) ‘Prevalence and risk factors of Campylobacter infection in broiler flocks from southern Spain’, Preventive Veterinary Medicine, 114(2), pp. 106–113. Available at: https://doi.org/10.1016/j.prevetmed.2014.01.019.
- Tustin, J. et al. (2011) ‘A national epidemic of campylobacteriosis in Iceland, lessons learned’, Zoonoses and Public Health, 58(6), pp. 440–447. Available at: https://doi.org/10.1111/j.1863-2378.2010.01387.x.
- V. Allain et al. (2014) ‘Prevalence of and risk factors for Campylobacter colonisation in broiler flocks at the end of the rearing period in France’, British poultry science, 55(4), pp. 452–459. Available at: https://doi.org/10.1080/00071668.2014.941788.
- Van Limbergen, T. et al. (2018) ‘Scoring biosecurity in European conventional broiler production’, POULTRY SCIENCE, 97(1), pp. 74–83. Available at: https://doi.org/10.3382/ps/pex296.
- Vose Consulting (US) LLC (2011) A quantitative microbiological risk assessment of Campylobacter in the broiler meat chain | EFSA. (Accessed: 6 October 2022).
- Weis, A.M. et al. (2016) ‘Genomic Comparison of Campylobacter spp. and Their Potential for Zoonotic Transmission between Birds, Primates, and Livestock’, Applied and Environmental Microbiology, 82(24), pp. 7165–7175. Available at: https://doi.org/10.1128/AEM.01746-16.
7.1 Sampling methods
Sampling results are provided in Annex I.
7.1.1 FSA survey
In order to answer the risk question, a survey of Campylobacter spp. in low-throughput poultry slaughterhouses that had not provided sampling results was set up. Sampling from the low-throughput slaughterhouses followed the Process Hygiene Criteria so as to match the sampling in high-throughput slaughterhouses. Sampling occurred weekly and was contracted out by FSA to Official Veterinarians and Campden BRI.
The samples were taken from the neck skin by the Official Veterinarian at the slaughterhouse after chilling of carcases. The samples were collected weekly for 10 weeks over September 2021 to December 2021 from 11 slaughterhouses.
15 neck skin samples were pooled into 5 x 26g samples for Campylobacter testing. Two plants did not provide neck skin samples – V and W – due to the type of processing employed, namely, skinning in feather. The carcases were swabbed instead. 5 ceca samples were also collected weekly from all plants. Plant S only provided caeca samples. The samples were sent to Campden BRI for testing. In brief:
Neck skins from a minimum of 15 poultry carcases were sampled at random after chilling during each sampling session. Before examination, the neck skin samples from at least three poultry carcases from the same flock of origin were pooled into one sample of 26 g.
Skinned in feather – not enough neck skin to sample, so swabbed instead
The samples were transported to the laboratory at a temperature not lower than 1 °C and not higher than 8 °C. The time between the sampling and testing for Campylobacter was less than 48 hours, in order to maintain sample integrity.
As laid out in the PHC, the 26 g test portion was transferred to nine volumes (234 ml) buffered peptone water at room temperature. The mixture was then treated in a stomacher or pulsifier for approximately one minute. Foaming was avoided by removing the air from the stomacher bag as much as possible. 10 ml (~ 1 g) of this initial suspension was then transferred to an empty sterile tube and 1 ml of the 10 ml was used for the enumeration of Campylobacter on selective plates.
Participating plants: B, H, J, M, N, O, P, Q, R, S, V, W, AF
7.1.2 FBO survey
FBOs are responsible for weekly testing and these need to follow the Process Hygiene Criteria. Results are reported to the FSA as:
- 100CFU/g or below
- above 1000CFU/g
- above 100CFU/g to 1000CFU/g
- 1000CFU/g or below
Full enumeration levels are not provided.
7.2 Slaughterhouse throughput
Table 10: Slaughterhouse throughput, 2021.* plants for which no samples are available.
Slaughterhouse Number | Throughput |
---|---|
A* | 140 |
B | 14,810 |
C* | 16,965 |
D* | 19,414 |
E* | 32,250 |
F* | 53,920 |
G* | 62,208 |
H | 96,711 |
I* | 104,065 |
J | 114,903 |
K* | 138,623 |
L* | 147,310 |
M | 149,828 |
N | 169,652 |
O* | 171,706 |
P* | 213,330 |
Q | 279,009 |
R | 344,612 |
S | 425,870 |
T* | 477,900 |
U* | 605,855 |
V | 774,193 |
W | 823,903 |
X* | 826,289 |
Y | 842,440 |
Z | 919,112 |
AA | 1,068,026 |
AB | 1,659,473 |
AC | 1,660,729 |
AD* | 1,692,356 |
AE | 1,725,677 |
AF | 2,739,544 |
AG* | 3,962,084 |
AH | 6,006,776 |
AI* | 6,045,432 |
AJ* |
6,082,674 |
AK | 6,207,361 |
AL | 6,955,742 |
AM* | 9,626,354 |
AN* | 14,992,071 |
AO | 16,531,082 |
AP | 16,905,125 |
AQ | 17,228,093 |
AR | 17,772,740 |
AS | 18,616,112 |
AT | 21,337,212 |
AU | 26,596,402 |
AV | 31,008,386 |
AW | 33,898,273 |
AX | 37,793,556 |
AY | 40,784,759 |
AZ | 47,479,148 |
BA | 47,742,107 |
BB | 50,303,391 |
BC | 50,780,751 |
BD | 65,690,264 |
BE | 93,045,048 |
BF | 94,389,252 |
BG | 103,360,123 |
BH | 109,275,875 |
7.3 Estimate of contaminated poultry on market
Table 11: Estimate of highly contaminated poultry per year from high-throughput slaughterhouses, based on multiplying throughput data with the observed prevalence of high Campylobacter levels.
Slaughterhouse approval number | Proportion samples exceeding 1,000CFU/g | Throughput per year | Estimated highly contaminated poultry per year |
---|---|---|---|
AZ | 0 | 47,479,148 | 0 |
BD | 0.02857143 | 65,690,264 | 1,876,865 |
AT | 0.03076923 | 21,337,212 | 656,530 |
AP | 0.08 | 16,905,125 | 1,352,410 |
AQ | 0.11235955 | 17,288,093 | 1,942,482 |
BF | 0.17777778 | 94,389,252 | 16,780,312 |
AS | 0.18181818 | 18,616,112 | 3,384,748 |
BC | 0.18888889 | 50,780,751 | 9,591,920 |
AU | 0.20689655 | 26,596,402 | 5,502,704 |
BA | 0.21111111 | 47,742,107 | 10,078,889 |
AO | 0.21538462 | 16,531,082 | 3,560,541 |
BE | 0.22352941 | 93,045,048 | 20,798,305 |
BH | 0.25690608 | 109,275,875 | 28,073,637 |
AX | 0.26086957 | 37,793,556 | 9,859,189 |
AV | 0.32 | 31,008,386 | 9,922,684 |
BB | 0.46268657 | 50,303,391 | 23,274,703 |
AW | 0.63291139 | 33,898,273 | 21,454,603 |
Total | - | 778,680,077 | 168,100,520 |
Table 12: Estimate of highly contaminated poultry per year from low-throughput slaughterhouses, based on multiplying throughput data with the observed prevalence of high Campylobacter levels.
Slaughterhouse approval number | Proportion samples exceeding 1000CFU/g | Throughput per year | Estimated highly contaminated poultry per year |
---|---|---|---|
AK | 0.625 | 6,207,361 | 3,879,601 |
AL | 0.4285 | 6,955,742 | 2,980,535 |
B | 0.42 | 14,810 | 6,220 |
J | 0.4035 | 114,903 | 46,363 |
Q | 0.34 | 279,009 | 94,863 |
H | 0.3279 | 96,711 | 31,712 |
V | 0.3 | 774,193 | 232,258 |
Y | 0.25 | 842,440 | 210,610 |
AH | 0.2308 | 6,006,776 | 1,386,364 |
N | 0.2 | 169,652 | 33,930 |
W | 0.18 | 823,903 | 148,303 |
R | 0.14 | 344,612 | 48,246 |
M | 0.12 | 149,828 | 17,979 |
AF | 0.1 | 2,739,544 | 273,954 |
AC | 0 | 1,660,729 | - |
AA | 0 | 1,068,026 | - |
S | 0 | 425,870 | - |
Total | - | 28,674,109 | 9,390,938 |